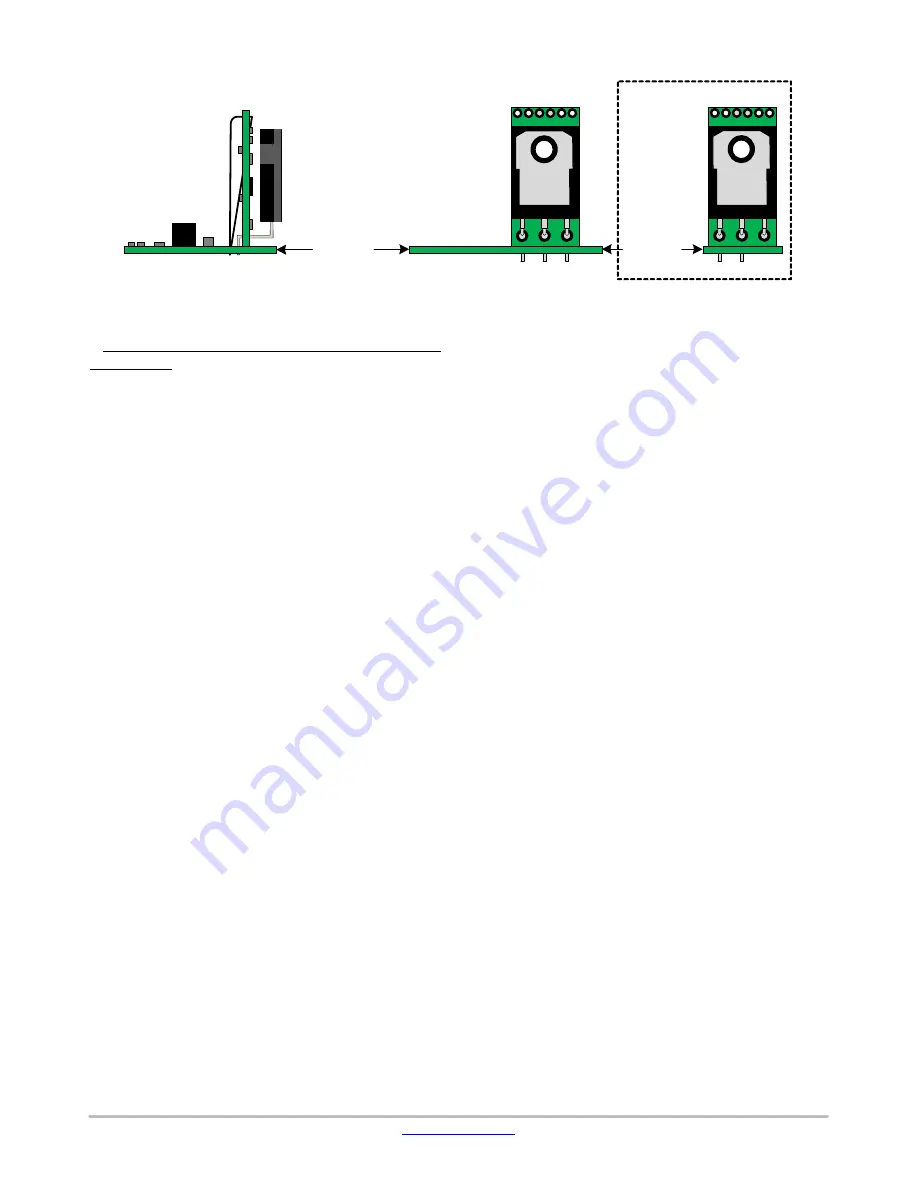
EVBUM2528/D
www.onsemi.com
9
Figure 11. Mini EVB Installation
−
Option 2
Mini EVB
T0
−
247
SiC
PWM Input
(flying lead)
S
T0
−
247
SiC
G
D
S
Mini EVB
Main PCB
T0
−
247
SiC
G
D
S
Mini EVB
Main PCB
T0
−
247
SiC
Option – Cut T0
−
247 gate lead
Side View
Back View
Recommended Procedure for Option 2 Mounting into an
Existing PCB
1. On the main PCB, isolate the gate drive to the
T0
−
247 SiC MOSFET. If the existing design
includes a gate drive resistor, removing it should
serve the purpose of isolating the gate drive to the
T0
−
247. If there is no series component between
the PWM signal source and the T0
−
247 gate lead,
the gate drive PCB track will need to be cut.
2. Measure the resistance between the PWM source
and the T0
−
247 gate lead (or PWM source to gate
drive transformer/isolator if applicable). Verify
reading is high impedance (open).
3. If a T0
−
247 discrete is installed in the main PCB,
remove it now.
4. Solder a flying lead of bus wire to the main PCB,
PWM signal. Make sure there is enough length of
the PWM input (flying lead) to reach through the
mini EVB plated thru
−
hole (J3 or J4)
5. For non
−
inverting PWM input logic, verify that
R5 (0
W
) is installed and R6 is removed. This is
the correct configuration of the mini EVB for
non
−
inverting PWM input logic.
6. For inverting PWM input logic, verify that R6
(0
W
) is installed and R5 is removed. This is the
correct configuration of the mini EVB for
inverting PWM input logic.
7. Make appropriate modifications to lead form the
T0
−
247 leads as shown in Figure 11. If the T0
−
247
leads are not long enough to provide sufficient
clearance between the mini EVB and T0
−
247 case
and allow the leads to pass through the mini EVB
and down through the main PCB, then extending
the lead length may be necessary.
8. After the T0
−
247 leads have been formed, check
for fit through the mini EVB and down into the
main PCB
9. Solder the T0
−
247 through just the mini EVB first
10. With the T0
−
247 installed into the mini EVB,
install and solder the T0
−
247 leads into the main
PCB
11. Solder the other end of the PWM input (flying
lead) to IN+ (J3) for non
−
inverting PWM
applications or IN
−
(J4) for inverting PWM
applications.
12. Using the same size bus wire, solder the remaining
connections between J1, J2, J5 and J8 of the mini
EVB to the appropriate locations on the main
PCB.
13. Solder flying leads from J6
−
7 for bias voltage to
the NCP51705. Note that J6
−
7 are across the
isolation boundary from J1
−
5 and J8.
Mounting into New PCB Design
The NCP51705, SiC Driver Mini EVB can also be used as
an iT0
−
247 “driver module” that can be
integrated into a new PCB design. The gate lead of the
T0
−
247 between the mini EVB and the main PCB is for
mechanical strength only. For main PCB layout, the gate
lead extends down through the main PCB and can be
soldered to an isolated plated thru
−
hole. As shown in
Figure 12, shoulder pins with appropriate flange are one
option that can be used as mounting pins between J1
−
8 of the
mini EVB and the main PCB. Another option, shown in
Figure 13
,
is to use a 100 mil center on center header which
is a row of pins through a plastic header. The plastic header
is used as a standoff for setting the mounting height between
the mini EVB and the main PCB. The hole pattern for
building a schematic library decal of the driver module is
shown in Figure 14
.