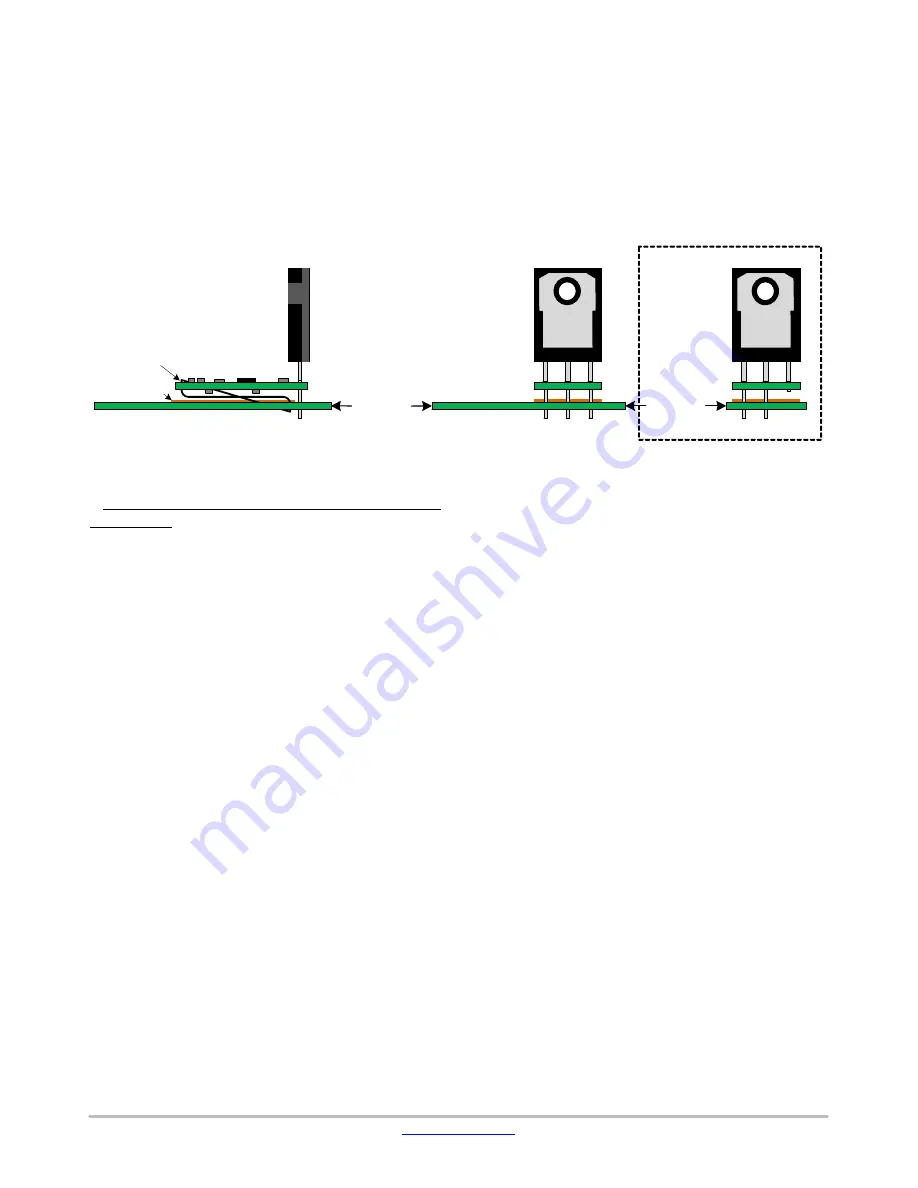
EVBUM2528/D
www.onsemi.com
8
EVB INSTALL CONFIGURATIONS
Mounting into Existing PCB
−
Option 1
The NCP51705, SiC Driver Mini EVB can be mounted
into an existing power board, shown as “Main PCB” in
Figure 10. If there are no components or low profile surface
mount components only, the mini EVB can be mounted
parallel to the main PCB as shown in Figure 10. The T0
−
247
,
SiC MOSFET leads would pass through the mini EVB
plated thru
−
holes and into the main PCB
.
Or, if necessary,
the gate lead of the T0
−
247, SiC MOSFET can be soldered
to the plated thru
−
hole on the mini EVB and cut so that it
does not contact the main PCB, as shown in the dotted box
in Figure 10
.
For mechanical strength, it is preferred that the
T0
−
247 gate lead pass through both PCB’s.
Figure 10. Mini EVB Installation
−
Option 1
Main PCB
Mini EVB
T0
−
247
SiC
PWM Input
(flying lead)
S
T0
−
247
SiC
G
D
S
Mini EVB
Kapton tape
Kapton tape
T0
−
247
SiC
G
D
S
Mini EVB
Main PCB
Option – Cut T0
−
247 gate lead
Side View
Back View
Recommended Procedure for Option 1 Mounting into an
Existing PCB
1. On the main PCB, isolate the gate drive to the
T0
−
247 SiC MOSFET. If the existing design
includes a gate drive resistor, removing it should
serve the purpose of isolating the gate drive to the
T0
−
247. If there is no series component between
the PWM signal source and the T0
−
247 gate lead,
the gate drive PCB track will need to be cut.
2. Measure the resistance between the PWM source
and the T0
−
247 gate lead (or PWM source to gate
drive transformer/isolator if applicable). Verify
reading is high impedance (open)
.
3. If a T0
−
247 discrete is installed in the main PCB,
remove it now.
4. Place Kapton or non
−
conductive tape over the
main PCB area directly beneath the mini EVB.
This is to avoid the possibility of having any
components on the bottom of the mini EVB touch
components or conductive surfaces on the main
PCB.
5. Solder a flying lead of bus wire to the main PCB,
PWM signal. Make sure there is enough length of
the PWM input (flying lead) to reach through the
mini EVB plated thru
−
hole (J3 or J4)
6. For non
−
inverting PWM input logic, verify that
R5 (0
W
) is installed and R6 is removed. This is
the correct configuration of the mini EVB for
non
−
inverting PWM input logic
.
7. For inverting PWM input logic, verify that R6
(0
W
) is installed and R5 is removed. This is the
correct configuration of the mini EVB for
inverting PWM input logic.
8. Solder the T0
−
247 through just the mini EVB first
9. With the T0
−
247 installed into the mini EVB,
install and solder the T0
−
247 leads into the main
PCB
10. Solder the other end of the PWM input (flying
lead) to IN+ (J3) for non
−
inverting PWM
applications or IN
−
(J4) for inverting PWM
applications.
11. Using the same size bus wire, solder the remaining
connections between J1, J2, J5 and J8 of the mini
EVB to the appropriate locations on the main
PCB.
12. Solder flying leads from J6
−
7 for bias voltage to
the NCP51705. Note that J6
−
7 are across the
isolation boundary from J1
−
5 and J8.
Mounting into Existing PCB
−
Option 2
If components mounted on the main PCB interfere with
mounting the mini EVB as described by Option 1
(Figure 10), the T0
−
247 leads can be formed (lead length
may need to be added) with the mini EVB mounted
perpendicular to the main PCB as shown in Figure 11, option
2. If required, both mounting options allow the application
of a heat sink to the T0
−
247 package. If high dV/dt is present
on the drain of the T0
−
247, the EVB should be angled, away
from being parallel to the T0
−
247, as much as possible.