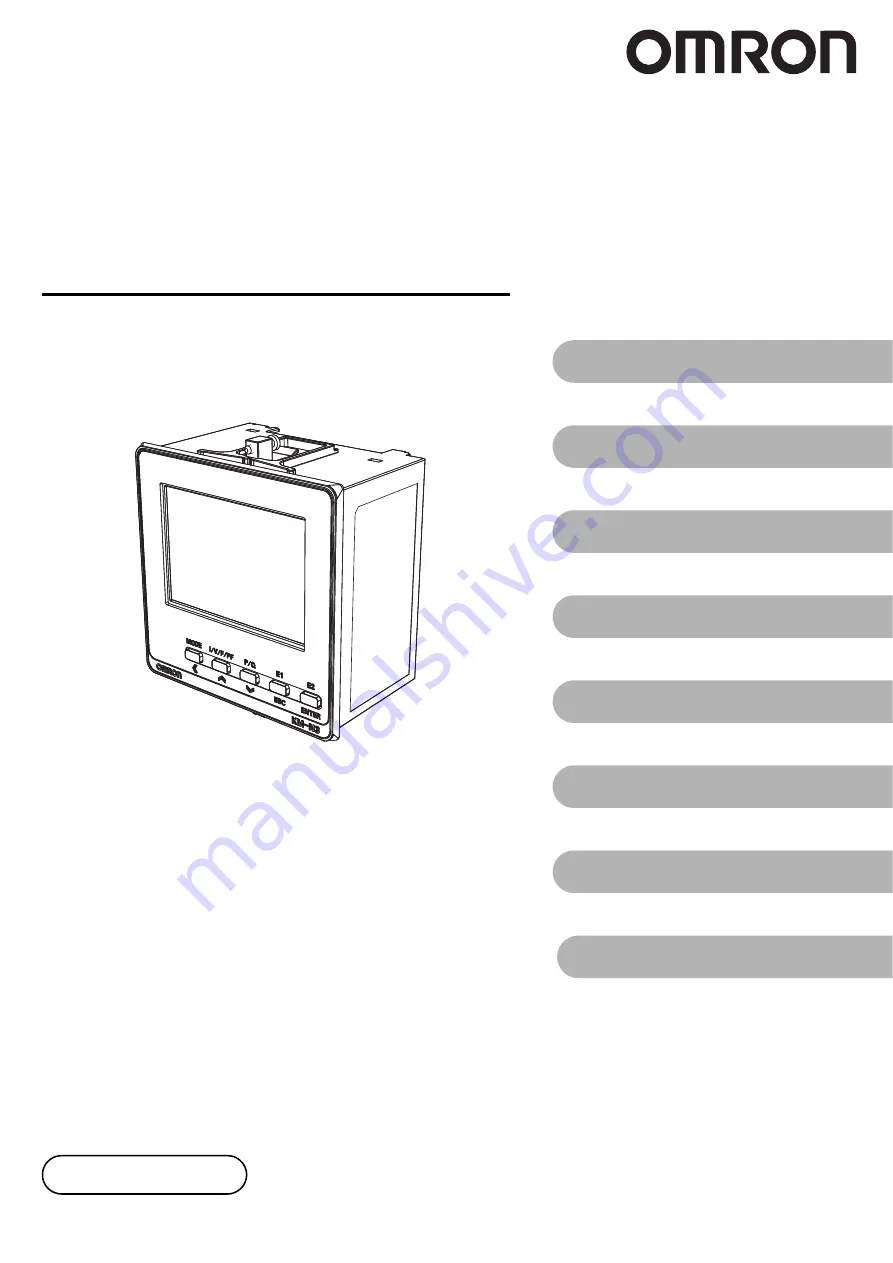
On-Panel Power Monitor
model
KM-N3-FLK
Users Manual
1. Overview of the unit
2. Installation and wiring
3. Basic use
4. Settings needed to measure
electricity
5. Other Functions
6. Detailed settings for communications
7. Troubleshooting
8. Appendices
Catalog no. N214-E1-02
Thank you for purchasing the On-panel Power Monitor, model KM-N3-
FLK (referred to as model KM-N3 in this manual).
This Users Manual describes the functions, performance, and
application methods needed for optimum use of the unit.
Please observe the following when using this unit.
• This product is designed for use by qualified personnel with a
knowledge of electrical systems.
• Before using the product, thoroughly read and understand this Users
Manual to ensure correct use.
• Keep this Users Manual in a safe location so that it is available for
reference whenever required.