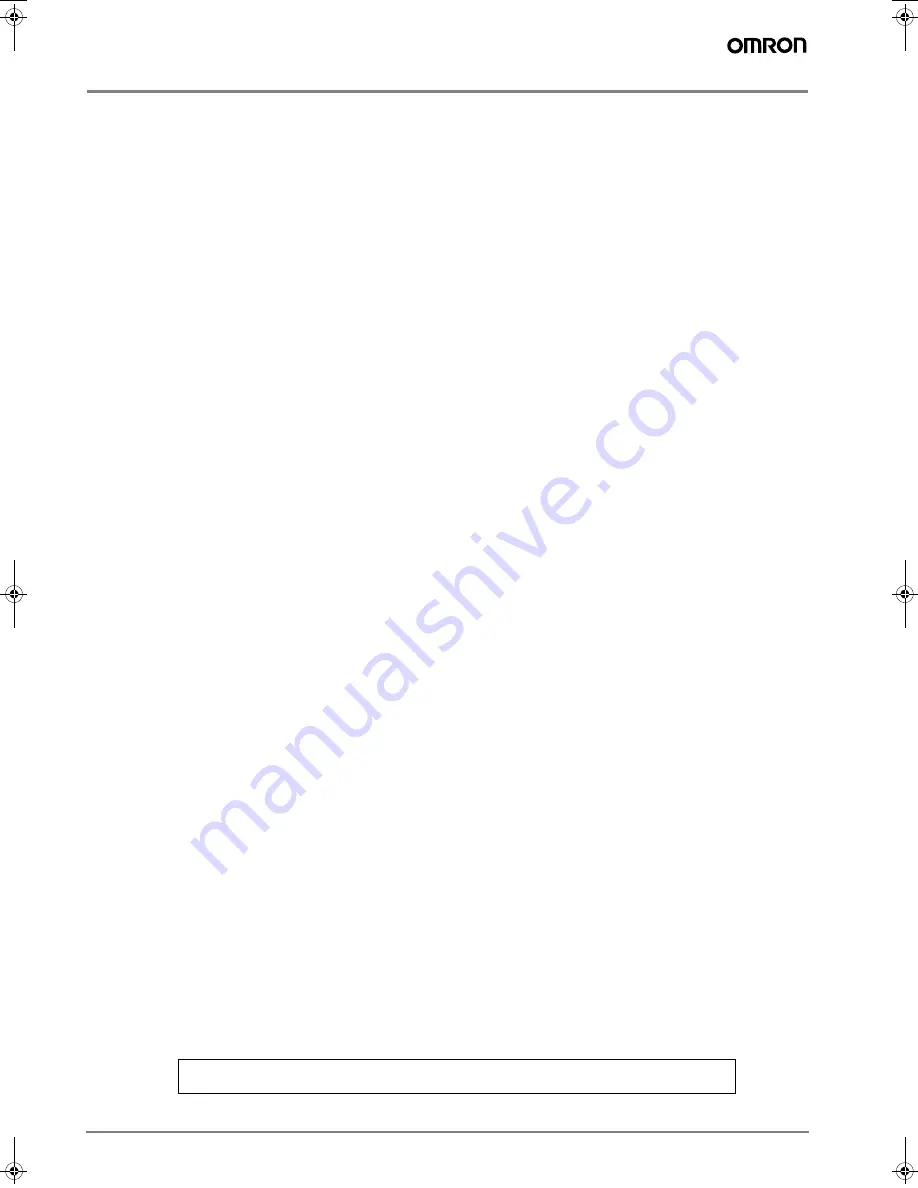
D-76
Inductive Sensors
Wiring
High-tension cables
Wiring through Metal Conduit:
If there is power or high-tension line near the cable of the
Proximity Sensor, wire the cable through an independent met-
al conduit to prevent against Proximity Sensor damage or
malfunction.
Mounting
Mounting the Sensor
The Proximity Sensor must be subjected to excessive shock
with a hammer when it is installed, otherwise the Proximity
Sensor may be damaged or lose its water-resistivity.
Maintenance and Inspection
Periodically perform the following checks to ensure stable op-
eration of the Proximity Sensor over a long period of time.
• Check for mounting position, dislocation, looseness or dis-
tortion of the Proximity Sensor and sensing objects.
• Check for loose wiring and connections, improper contacts
and line breakage.
• Check for attachment or accumulation of metal powder or
dust.
• Check for abnormal temperature conditions and other envi-
ronmental conditions.
Never disassemble or repair the Sensor.
Environment
Water Resistivity
Do not use the Proximity Sensor underwater, outdoors or in
the rain.
Operating Environment
Be sure to use the Proximity Sensor within its operating ambi-
ent temperature range and do not use the Proximity Sensor
outdoors so that its reliability and life expectancy can be main-
tained. Although the Proximity Sensor is water resistive, a
cover to protect the Proximity Sensor from water or water-sol-
uble machining oil is recommended so that its reliability and
life expectancy can be maintained.
Do not use the Proximity Sensor in an environment with
chemical gas (e.g., strong alkaline or acid gasses including ni-
tric, chromic and concentrated sulfuric acid gases).
Inrush Current
A load that has a large inrush current (e.g., a lamp or motor)
will damage the Proximity Sensor, in this case connect the
load to the Proximity Sensor through a Relay
In the interest of product improvement, specifications are subject to change without notice.
ALL DIMENSIONS SHOWN ARE IN MILLIMETERS.
To convert millimeters into inches, multiply by 0.03937. To convert grams into ounces, multiply by 0.03527.
Cat. No.
D01E-EN-02
F502-EN2-04.book Seite 76 Dienstag, 26. Juli 2005 5:48 17