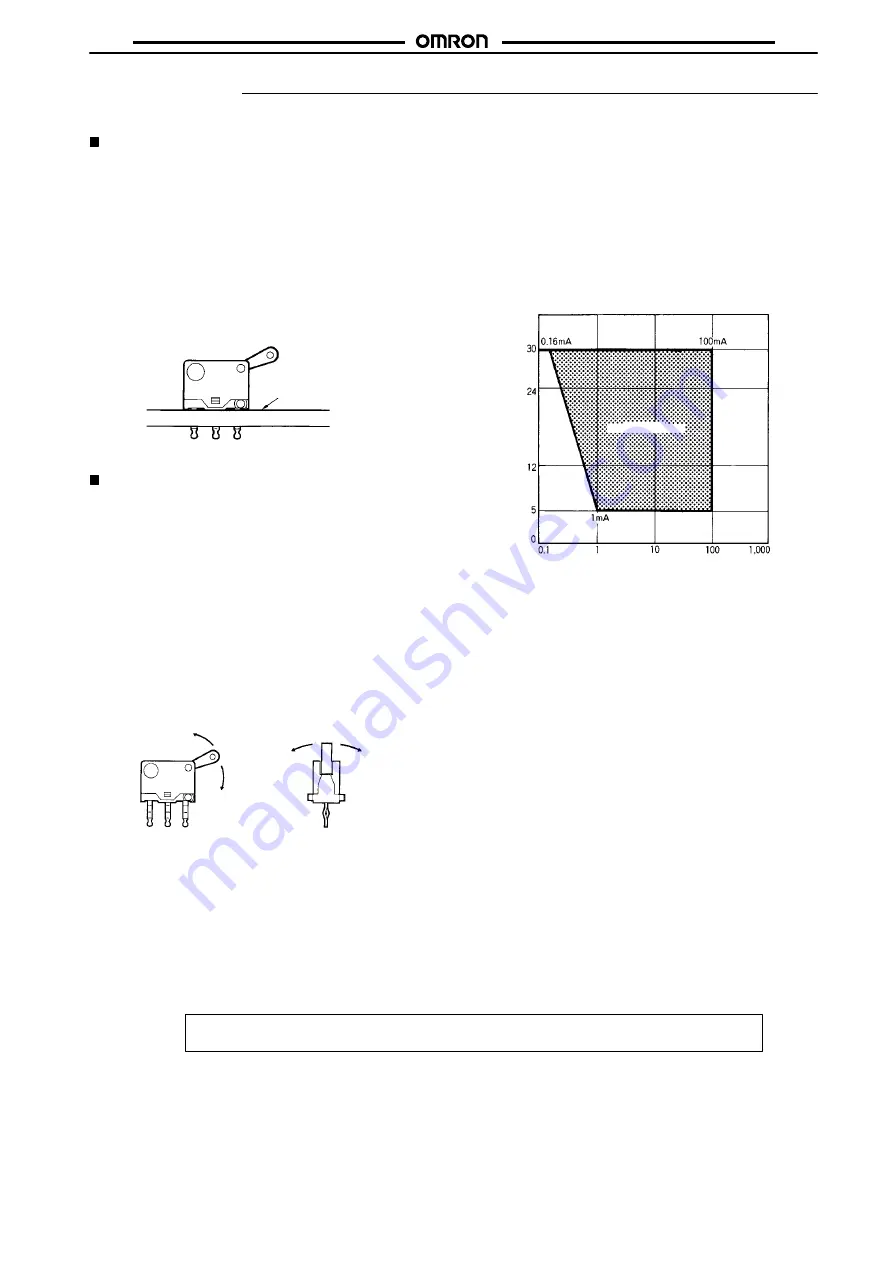
D3C
D3C
257
Precautions
Refer to pages 26 to 31 for common precautions.
Cautions
Terminal Connection
When soldering the lead wire to the terminal, first bind the lead wire
to the terminal and then apply the 6 (Sn) : 4 (Pb) solder to the termi-
nal. Complete soldering within 5 s at a soldering iron temperature of
260
°
C. Soldering at a temperature exceeding 260
°
C, soldering for
more than 5 s, or repeated soldering will degrade the Switch charac-
teristics.
When soldering the lead wire to the PCB terminal, pay careful atten-
tion so that the flux and solder liquid level does not exceed the PCB
level.
It is also recommended that you apply flux guard to the mounting
surface of the Switch.
Switch mounting surface
Correct Use
Mounting
Turn OFF the power supply before mounting or removing the
Switch, wiring, or performing maintenance or inspection. Failure to
do so may result in electric shock or burning.
Use M1.6 mounting screws with plane washers or spring washers to
securely mount the Switch. Tighten the screws to a torque of 4.9 to
9.8
10
–2
N
S
m {0.5 to 1 kgf
S
cm}.
Mount the Switch onto a flat surface. Mounting on an uneven sur-
face may cause deformation of the Switch, resulting in faulty opera-
tion or breakage in the housing.
Application of Operation Force to the Lever
Apply operation forces to the lever in its operating direction. Apply-
ing operating force to the lever in any other directions will damage
the Switch or cause malfunction.
Incorrect
Incorrect
Incorrect
Correct
Mounting Plate
Use materials other than ABS or polycarbonate for the mounting
plate. Since grease is used for the Switch, cracks may be caused if
grease from the Switch comes in contact with such materials.
Using Micro Loads
Using a model for ordinary loads to open or close the contact of a
micro load circuit may result in faulty contact. Use models that oper-
ate in the following range. However, even when using micro load
models within the operating range shown below, if inrush current oc-
curs when the contact is opened or closed, it may increase contact
wear and so decrease durability. Therefore, insert a contact protec-
tion circuit where necessary.
The minimum applicable load is the N-level reference value. This
value indicates the malfunction reference level for the reliability lev-
el of 60% (
λ
60). The equation,
λ
60 = 0.5
10
–6
/operations indi-
cates that the estimated malfunction rate is less than 1/2,000,000
operations with a reliability level of 60%.
Operating range
Inoperable
range
Current (mA)
V
oltage (V)
ALL DIMENSIONS SHOWN ARE IN MILLIMETERS.
To convert millimeters into inches, multiply by 0.03937. To convert grams into ounces, multiply by 0.03527.
Cat. No. C099-E1-02C