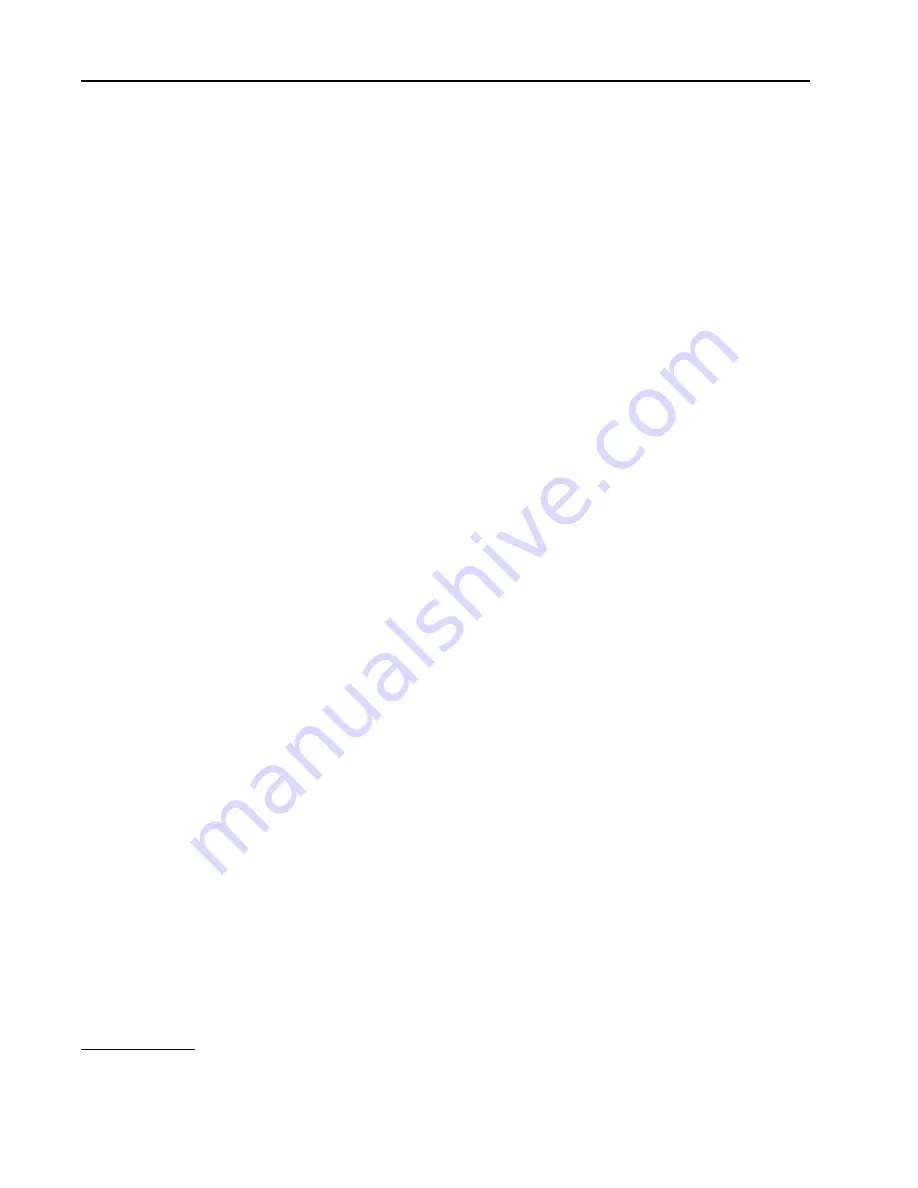
Volume VII–System Description
OMEGA EP Operations Manual
Page 2 of 35
The TC design takes advantage of the substantial infrastructure developed for the OMEGA
System and allows for the full compatibility of existing diagnostic instrumentation. The TC will support
six ten-inch-manipulator (TIM) diagnostic shuttles (three initially), a target positioning system (TPS),
a target viewing system (TVS), and other support items whose designs are based on their OMEGA
equivalents. The top and bottom ports are reserved for the future addition of a planar cryogenic target
system. The TC has two off-axis parabola inserter/manipulators (OAPI/M). These TIM-like devices are
used for the insertion and removal of the off-axis parabolas. Beam transport tubes from the GCC enter
the TC from the west and provide for sidelighting and backlighting target applications. The TAS also
supports the IR transport mirrors, FCC’s, PMA, UV end and target mirrors and the diagnostic pickoffs
for the four UV diagnostic packages. The UV alignment table (UVAT) is located on the Laser Bay floor,
south of the TAS.
1.6
Timing Systems
The Hardware Timing System (HTS) provides precision timing signals (see Table 1.4) that
synchronize the OMEGA EP subsystems to produce a laser pulse and acquire diagnostic data. End-
to-end synchronization is provided by the reference frequency generator (RFG) that drives the laser’s
master oscillator, the master timing generator (MTG), and the timing crates. The MTG provides derived
rates that are also distributed. Local timing stations known as “crates,” include programmable modules
that provide synchronized, precisely delayed rate and trigger signals. Figure 1.13 provides a simplified
block diagram showing the main components of the HTS and the paths of the timing signals. The timing
signals include (1) the video sweep signals that are synchronized with the master laser oscillator to allow
video cameras to capture the laser pulses, (2) trigger signals for the electro-optical devices that select
and shape optical pulses in the laser portion of the system, (3) trigger signals for the power conditioning
units that power the high-voltage flash lamps in the laser amplifiers, and (4) trigger signals for high-speed
diagnostic instruments for both laser-system and target-physics applications. The signals are distributed
throughout the facility and provided to equipment via colocated CAMAC
®4
rates. A software control
interface is provided to allow operators to select rates and set delays to these timing signals.
The RFG consists of a precision crystal oscillator, a distribution amplifier, and a series of passive
signal splitters mounted with control and monitor circuits in a standard 19-in. rack-mount enclosure
located in the Laser Sources Bay. The oscillator design ensures a frequency stability better than 1 ppm
during all operations. The RFG is the starting point for all the timing signals and produces a nominal
38-MHz sine wave whose frequency is doubled to drive the laser’s master oscillators. The RF signal
is distributed to the MTG and also to a rate regenerator module (RRM) in each of the timing crates
distributed throughout the laser systems. The 38-MHz RF and the other (digital) signals used by the
HTS are distributed throughout the facilities. The RRM in each crate accepts the RF signal, 0.1-Hz rate,
and T–10 and T–0 digital signals from the MTG. The RRM regenerates these signals and provides them
to quad-channel delay modules (QCDM’s). Each QCDM has four independent channels that can each
be set to implement a precision delay to one of the seven input signals. As many as 12 QCDM’s can be
installed in a crate with one RRM.
4
Computer automation and control (CAMAC) is a set of industry standards that defines mechanical, electrical, and
communications protocols. These allow standard and custom built functional modules to be provided with mechanical
support, electrical power, and a unique data-bus connection in standardized card cages known as CAMAC crates.
Summary of Contents for Volume VII-System Description
Page 38: ......