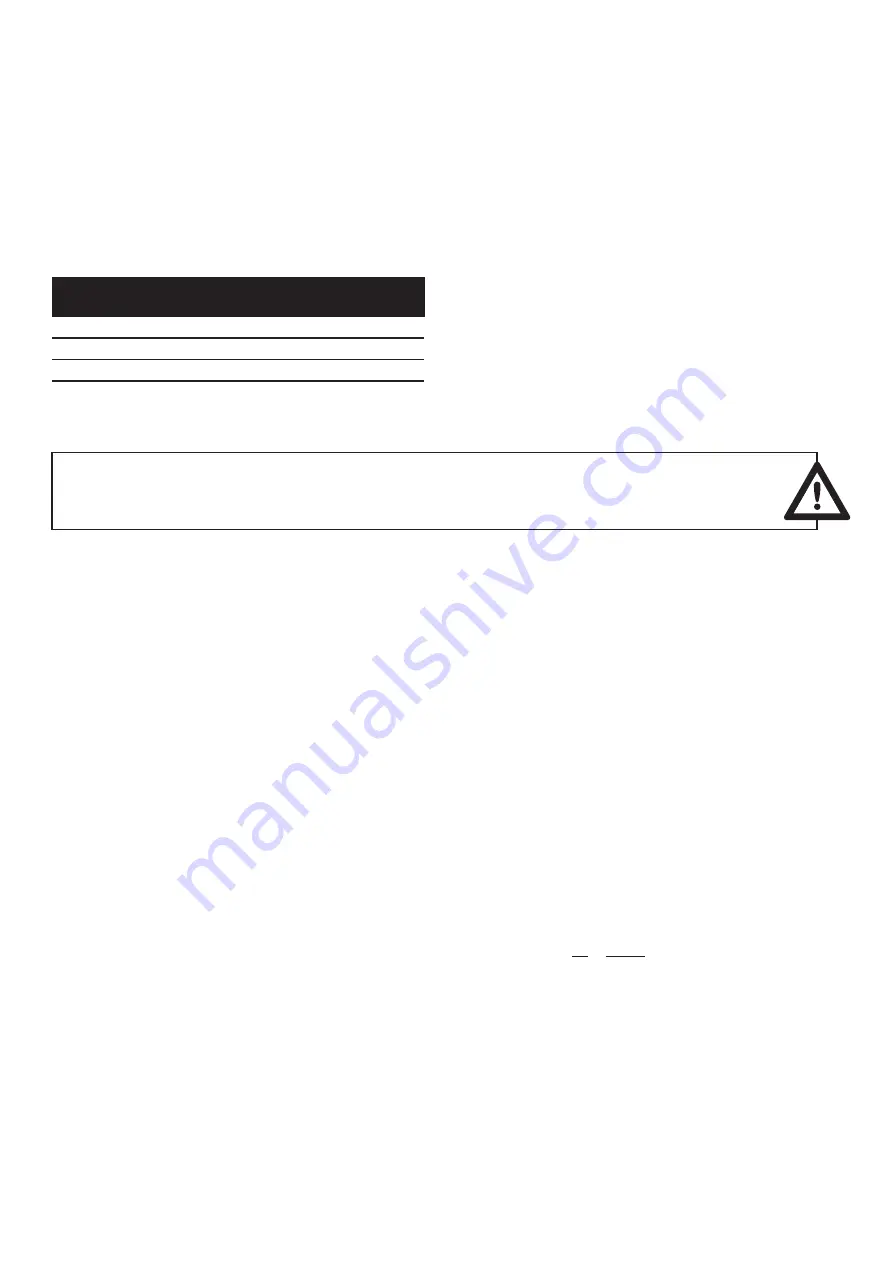
7
11. Fluid Filtering
Heavily contaminated fluids or foreign matter in the fluid can block, da-
mage, and even destroy the flow meter. In these cases, always install a
sufficiently large filter in front of the flow meter so that foreign particles and
solids are prevented from entering the measuring elements, thus preventing
damage to the flow meter. The required filtering depends on the size, bea-
ring, and design of the flow meter.
Flow meter size
Filter size for
ball bearing
FHG 1xx2
250 µm
FHG 1xx4
250 µm
FHG 1xx5
500 µm
FHG 1xx7
500 µm
Table 2: Upstream filters
The filter size for flow meters with slide bearings, in special designs, or with
specially adapted measuring element tolerances can be obtained from
Omega upon request.
Important:
A blocked flow meter is capable of stopping the entire flow.
An overpressure / bypass valve must be installed in the system side.
12. Sensor Electronics Function
The liquid to be measured flows through the rotor chambers in axial direc-
tion, resulting in an even rotation of the screw spindles.
This is done especially gentle and with very low resistance for the fluid to
be measured as well as pulsation-free and almost free of leaks due to the
specially designed fluidic profile geometry.
A magnet wheel permanently affixed to the rotors is scanned without
contact with a sensor module. The non-contact pick-up system consists of
two GMR bridges (sin /cos), which are located in a sensor unit in cartridge
design. It detects every movement of the sensing gear and routes the sin/
cos signals to the preamplifier electronics. The preamplifier electronics di-
gitise and amplify the sensor signals and multiply them by a high-resolution
interpolator using adjustable settings. The square wave signals phase-shif-
ted by 90° are bidirectional and can be utilised by any evaluating device
as well as computers and PLC controls.
The flow is proportional to the edges/pulse count and the flow rate is pro-
portional to the frequency. The adjustable interpolator can be used to ad-
just the resolution explicitly to the downstream connected evaluating unit
for obtaining highly precise measuring results of the entire system. This ap-
plies to the following application cases, for example:
• Measuring, controlling, and regulating high viscosity fluids
• Measuring, controlling, and regulating in lower flow ranges
• Measuring, controlling, and regulating when passing through zero
• Measuring, controlling, and regulating in both flow directions
• Measuring, controlling, metering, and filling of small volumes
The resolution is selectable in steps from factor 1 to 128. The frequency
range is from 0 to 100 kHz.
In case of a 1-channel evaluation, a separate directional signal is availa-
ble.
The preamplifier is protected against reverse polarity and incorrect con-
nection. It is designed for fluid temperatures of -30°C up to +120°C and is
mounted directly on the FHG flow meter.
The fluid volume passed through by one gear division of the sensing
wheel within the measuring element is divided by the set interpolation fac-
tor.
This forms the measurement volume per pulse (V
m
) with the defined unit
[cm³/pulse].
The frequency of the output signals can be calculated as follows:
Formula 1: Calculation of the output frequency with Q in l/min
Table 2, Formula 2, and the subsequent diagrams can be used to determine
the corresponding resolution or the corresponding IPF for the respective
application.
Adjustable interpolation factors IPF: 1, 2, 5, 10, 25, 32, 50, 64, 100, 128
f= Q x 1000
V
m
60