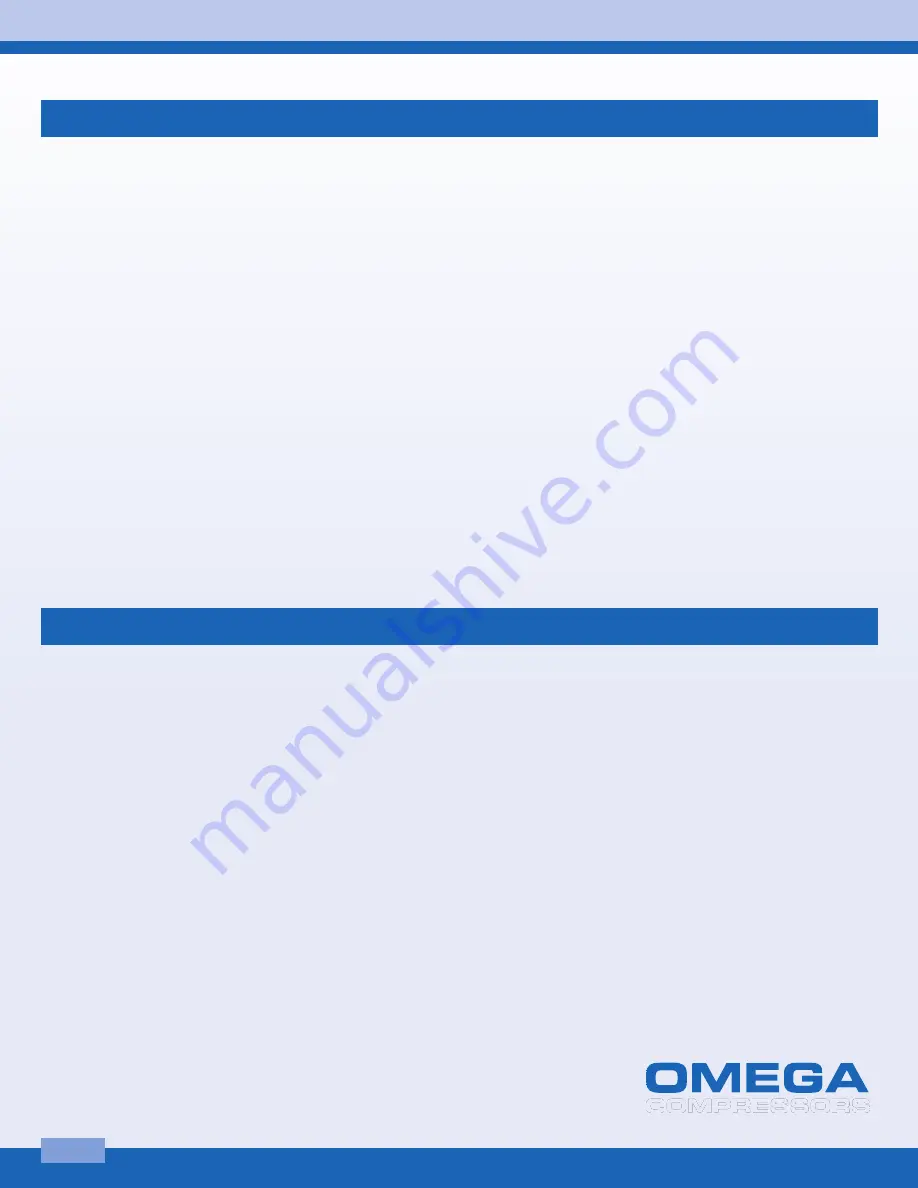
For us, it’s not just business. It’s personal.
INITIAL START-UP PROCEDURE
Do not attempt to operate the unit without fi rst checking whether there is oil in the pump. Add oil as required.
Serious damage may result from use without oil. See page for proper compressor lubrication.
1.)
Check to see that nuts and bolts are all snug. This must be done, as some fasteners may become loose in transit.
2.)
Check to see if the belt is installed properly, with proper tension.
3.)
Check belt tightness so that when pressure is applied at the centre, there is ½” slack.
4.)
Check that proper type and oil level is correct. See page 3 for proper compressor lubrication.
5.)
Check that compressor is fi xed on a strong, stable level base.
6.)
Check that oil breather is clean.
7.)
Check that air fi lter is clean.
8.)
Do not place any materials on or against the belt guard, or the compressor unit itself. Placing materials there
will limit the cooling of the compressor and could lead to premature failure.
9.)
Turn the compressor “on” momentarily by positioning the fused disconnect in the “on” position. Ensure that
the fl ywheel is turning in the correct position. See “PUMP ROTATION” (page 3). On compressors with three
phase power, adjust the wiring at the motor terminals if the rotation is incorrect. Refer to the wiring diagram
on or in the motor terminal box.
10.)
Open the air receiver outlet ball valve and start the unit. Ensure air is escaping to atmosphere. Allow the unit to
operate for a minimum of twenty minutes in this no-load condition to lubricate bearings and pistons.
11.)
After running the compressor unit for twenty minutes, close the ball valve, and allow the unit to reach
maximum operating pressure. Ensure that the compressor shuts down at the pre-set maximum pressure, and
the head pressure is released through either the pressure switch or the CPR on the front of the pump.
12.)
Check the air compressor and piping systems for air leaks, and correct as required.
13.)
Shut off all power to the air compressor before attempting any repair or maintenance.
14.)
Stop the compressor, and check the oil level in the crankcase. Add oil as required.
15.)
Your compressor is ready for use.
PREVENTATIVE MAINTENANCE
Before doing any maintenance or adjustments to your air compressor, the following safety precautions should be taken.
1.)
DISCONNECT ELECTRICAL POWER.
2.)
DRAIN AIR RECEIVER OF AIR PRESSURE.
DAILY CHECK LIST
1.)
Check Oil Level.
2.)
Drain Condensation from Air Receiver.
3.)
Check for Any Unusual Noise or Vibration.
4.)
Be Sure All Nuts and Bolts are Tight.
WEEKLY CHECK LIST
1.)
Clean Air Filter by Opening Air Filter Cap. Replace Filter if Necessary.
2.)
Check Oil Level and Top Up if Necessary.
QUARTERLY OR 300 HOUR CHECK LIST
1.)
Change Oil and Filter Element.
2.)
Check Condition and Alignment of Belt, Flywheel and Motor Pulley. Adjust Belt Tension if Necessary or Replace
Belt if Worn.
3.)
Check Safety Valve.
4.)
Check Pressure Switch Unloader to Ensure Compressor Head Unloads Whenever Motor Shuts Down.
5.)
Clean and Blow Off Pump Fins and Motor.
6.)
Inspect Air System for Leaks, by Applying Soapy Water to All Joints. Tighten Joints if Leakages are observed.
4
Summary of Contents for 23045
Page 11: ...9 MAINTENANCE LOG CHART...