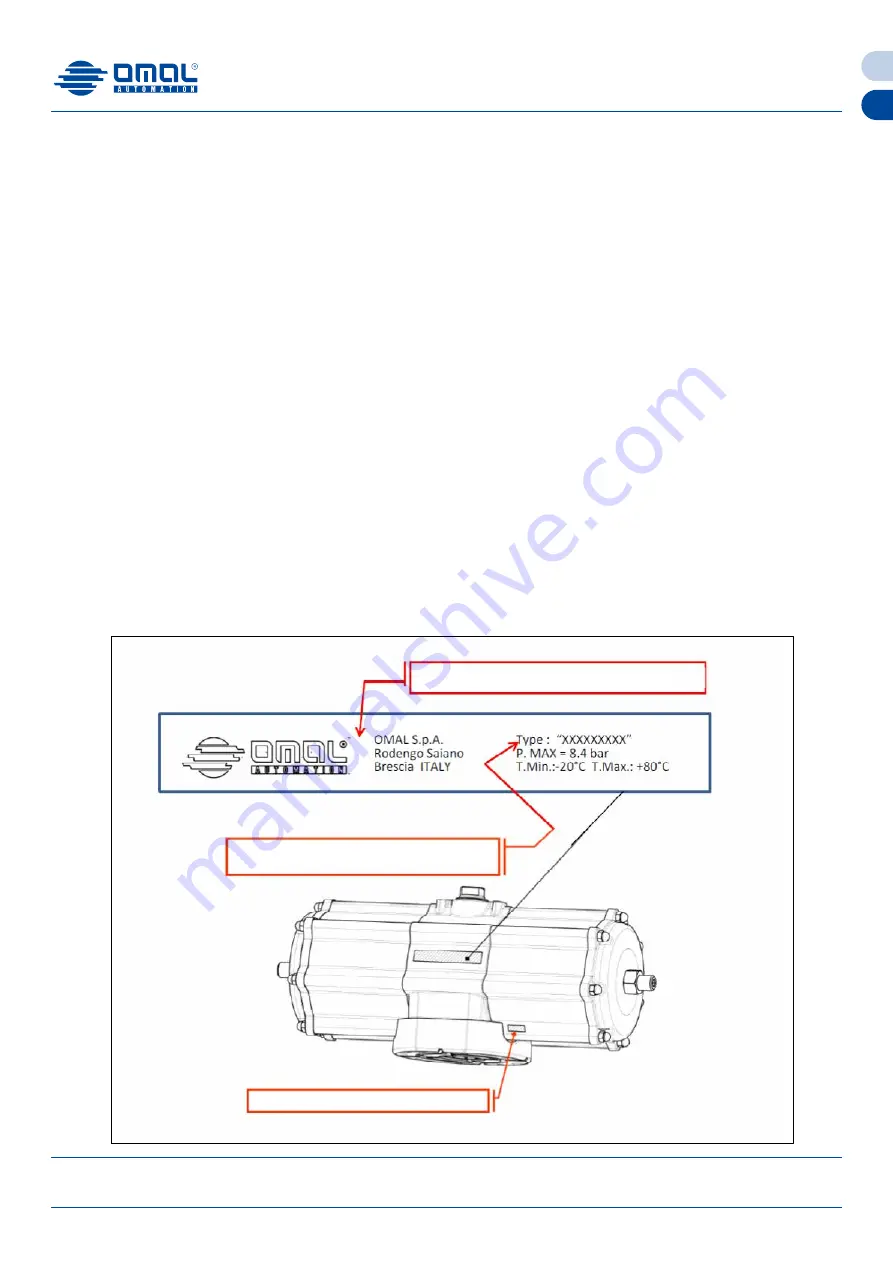
Rif. UMA800081C - 06/22
IT
EN
EN -
6
OMAL S.p.A.
Headquarters
: Via Ponte Nuovo, 11 - 25050 Rodengo Saiano (BS) Italy •
Production Site:
Via Brognolo, 12 - 25050 Passirano (BS) Italy
Ph.
+39 030 8900145 •
Fax
+39 030 8900423 • [email protected] •
www.omal.com
INSTRUCTION MANUAL
AGO: SCOTCH–YOKE PART TURN PNEUMATIC ACTUATOR
DA2880 - DA8000 - SR1440 - SR4000
g. Lubrification.
The actuators are lubricated, for normal working conditions, in the company. For maintenance or reassembly operations, OMAL S.p.A.
recommends the use of a lubricant such as TECNOLUBE SYNTHY POLYMER 402 or equivalent.
h. Functional Safety
The OMAL S.p.A. pneumatic actuators are also suitable for installations which require high level of functional reliability, up to SIL3, in
compliance with the IEC 61508 standard.
i. Wear protection of internal components
The cylinder is electrolysis nickel plated internally, in order to reduce roughness of the surface
to a minimum value and is protected with an oxidation treatment which is 20μm thick. The guides of the pistons are made of acetalic
resin. The use of steel bushes on the Scotch yoke system reduce backlash and confer very low friction sliding during operation.
j. External protection
The actuators are suitable both for indoors and outdoors. The aluminum body and the caps are protected against corrosion by an
oxidation treatment which is 20 µm thick; the shaft and cap screws are made of stainless steel.
This generally allows to meet the C4 safety class, for applications that require it, according to the standard EN 15714-3 section 4.4.3.
For applications in environments with aggressive type atmospheres that require a higher protection level than C4, the actuator must
be protected with a suitable varnishing treatment.
k. Marking and classification
The bodies of the OMAL S.p.A. actuators are marked, by means of laser engraving or a label, with the manufacturer’s logo and ad-
dress, the code or the serial number, the size, the output torque, the working pressure and the maximum working temperature and
the production date.
Marking of versions where the temperature is different from the standard one:
low temperature version: T. min.= -50°C T. max=60°C
high temperature version: T. min.= -20°C T. max=150°C
1) Logo and address of the manufacturer
2) Product code including the series “DA” the no-
minal torque “XXXX” and their type of flange “FXX”
3) Production date code “XX/XX”