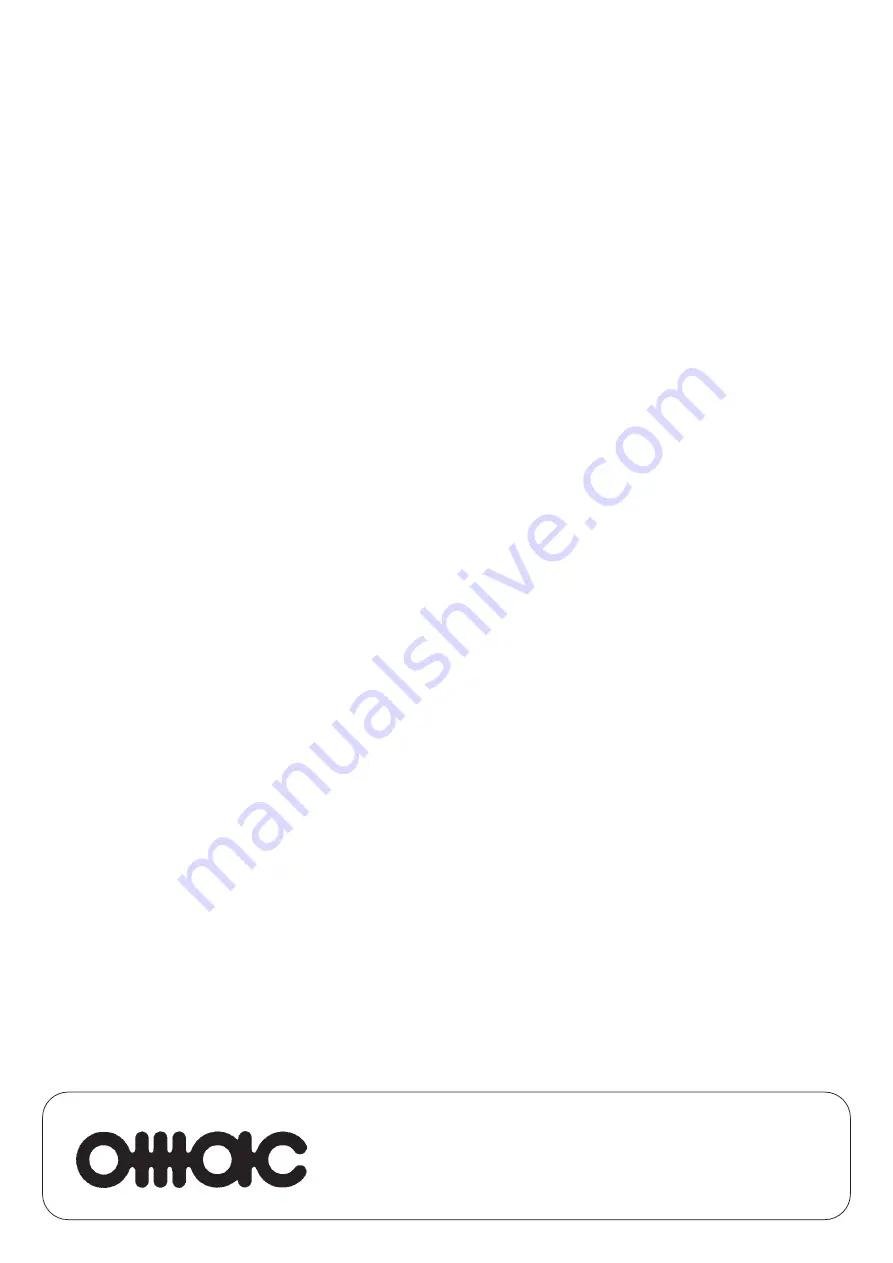
IT
ALGRAF - RUBIERA
(RE)
OMAC S.r.l. POMPE Via G. Falcone, 8 - 42048 RUBIERA (RE) - ITALY
TEL. 0522 629371-629923 - FAX 0522 628980
www.omacpompe.com - E-mail:[email protected]
Summary of Contents for B Series
Page 1: ...Installation operation and maintenance manual AUT N 810 EDIZ 07 01 ...
Page 36: ...36 Fig 21 Safety valve and hand by pass 3 BY PASS SAFETY VALVE ON PUMP COVER ...
Page 38: ...38 Fig 18 Pump type B105 B110 B115 ...
Page 39: ...39 Fig 19 Pump type B215 B220 B325 B330 B430 B440 ...
Page 40: ...40 Fig 20 Pump type B550 B660 B680 ...
Page 43: ...43 ...
Page 44: ...44 ...
Page 45: ...45 ...
Page 46: ...46 Fig 40 Cross section type B100 ...
Page 47: ...47 Fig 41 Pump type B100 ...
Page 50: ...50 ...
Page 51: ...51 ...