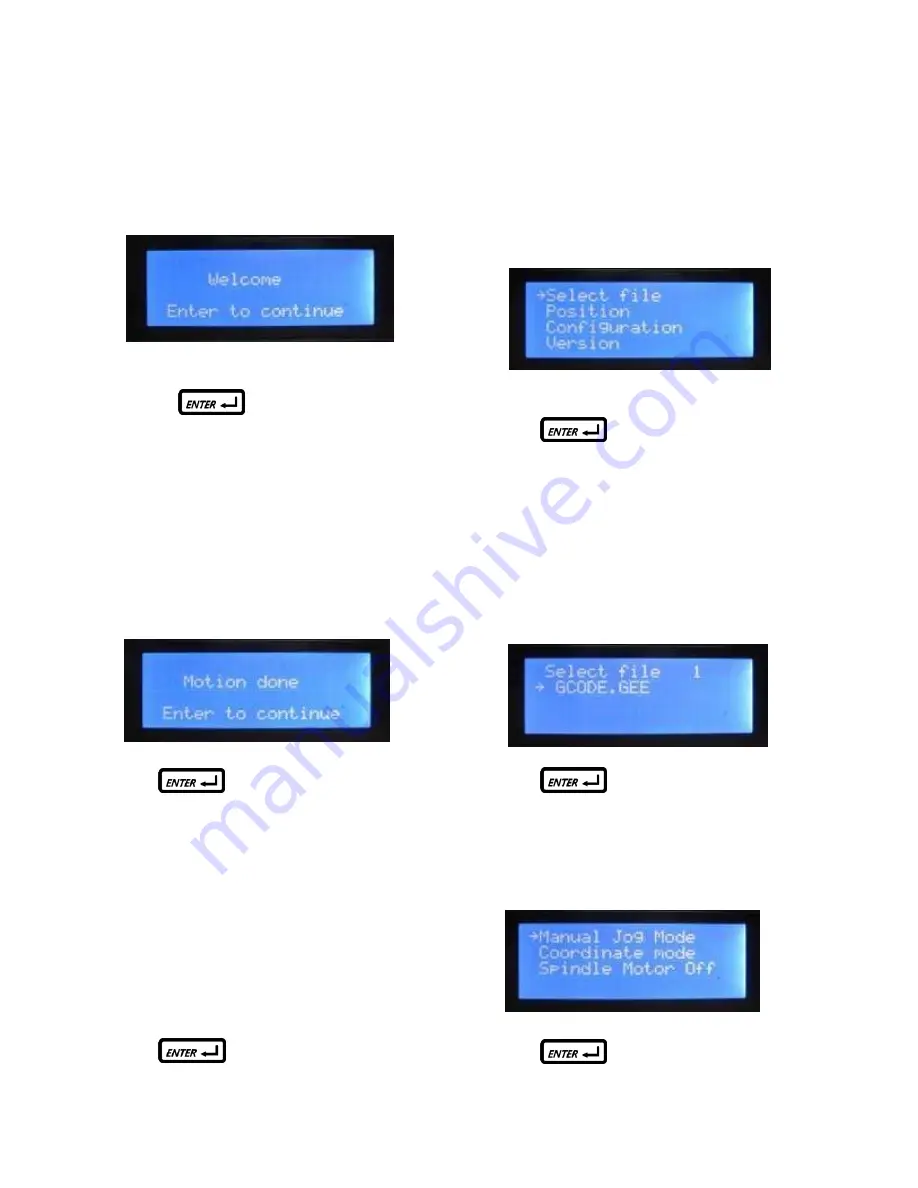
21
Setting Up To Carve (cont.)
Using the control panel
1
. When you first turn the machine on you will notice
the control panel display will read:
Pressing
on the keypad will automati-
cally start the spindle toward its home point (X=0,
Y=0, Z=0).
2
. After the spindle reaches its home point, the dis-
play will read:
Press
to continue.
3
. The next three screens will prompt you to check:
a. Is the ‘cutting tool’ is secure?
b. Is the ‘workpiece’ secure?
c. Is the flash drive in the ‘USB’ port?
Press
after confirming each of these.
4
. The next screen to appear is the main operating
screen as seen below. Use the arrow button on the
con
troller to set the cursor to ‘Select file’ as shown:
Press
to continue.
5
. Use the arrow buttons to scroll up or down to the
desired file as indicated by the cursor (this is the file
you converted from i-Picture and copied to the flash
drive)
. In this case the file is called ‘GCODE.GEE’
as shown:
Press
to continue.
6
. Select ‘Manual Jog Mode’ as show:
Press
to continue.
Summary of Contents for M1013
Page 37: ......