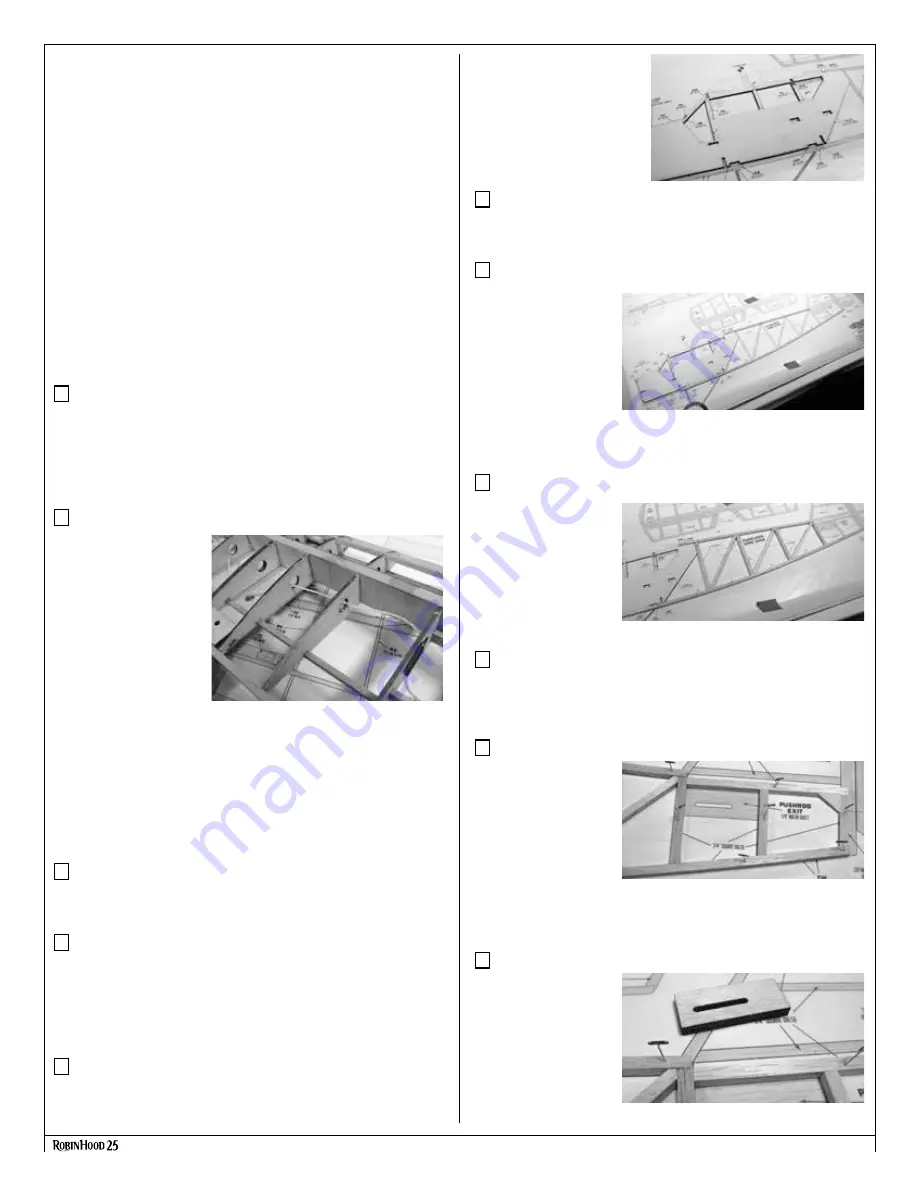
Construction Manual
www.oldschoolmodels.com
Page 7
and WH4 from the LP4 sheet. Also, cut a 1-1/4” length from the
included 1/4” dowel and round off one of the dowel’s ends.
These pieces all interlock together so we suggest dry fitting these
components the first time.
In the rounded part of the WH1’s and WH2 is a 1/4” dia. hole. Slide
the non-rounded end of the 1/4” dowel through one of the WH1’s
and push it through so it extends a 1/4” out of the opposite side.
Next push the WH2 on, and finally the other WH1. By lining up the
WH1’s and the WH2, you’ll see that their tabs will now slide into the
slots in WH3. Once WH3 is in position, the remaining tabs on WH2
can now be slid into WH4, and then into WH5, already installed on
the wing.
After you see how all these pieces go together, disassemble them
and re-assemble using glue. Make sure that the WH1’s and WH2
pieces are perfectly in line before the glue sets. Then make sure
that WH3 fits flat against WH4, and in turn, WH4 fits flat against
WH5 as you’re gluing them together.
Step 34 - Wing Assembly (sanding)
You’ll need to take a bit of the edges off the corners of WH3, as
it protrudes a bit from the curvature of the wing rib R2 on each
side. Also, do not sand down any of the WH1/WH2 assembly as
the wood that protrudes from the bottom of the wing’s surface is
needed for strength.
Step 35 - Wing Assembly (Optional strings)
This step is optional, but
could make the aileron
servo installation a bit
easier, once the wings
are covered. Cut two 12”
lengths of string, one for
the left wing, and one
for the right. Remember
that hole cut in the lower
sheeting, middle section
in step 30? Starting with the left wing panel, push the thread
through this hole, then through the circular holes in R2, R3, and
R4. The string will now extend from the servo bay, out through the
bottom of the wing. Tape both ends of the string so they won’t pull
out. Do the same for the right panel.
This completes assembly of the Robinhood 25 wing.
Now it’s time to start construction of the fuselage.
Prepare your work area
Now tape the fuselage side plan and a fresh piece of waxed paper
on your building board.
Step 36 - Fuselage Assembly
The fuselage sides are made by first constructing the right side,
then building the left side on top of the right side. Because of
this, you’ll need to pay attention to where pins are used during the
construction of the right side, so they won’t interfere with aligning
the left side parts.
Step 37 - Fuselage Assembly (FRS)
Construction starts with the right side of the fuselage. Locate FRS
from sheet LP1. Pin FRS in position over the plans, but do not pin
through the wood. Instead,
use a few pins around the
outside of FRS as shown in
the photo. Mark the side
facing up as “right” in small
letters, as a reference for
later.
Step 38 - Fuselage Assembly (top longeron)
Measure and cut the top longeron from 1/4” square strip. Pin in
position and glue to FRS.
Step 39 - Fuselage Assembly (bottom longeron)
Take one of the
complete 1/4” square
strips and begin to
pin in place to form
the bottom longeron,
working from the tail of
the fuselage, forward.
this piece is curved and
will require several pins along it’s length to hold in place. This piece
ends at F3. Once in position, glue to FRS.
Step 40 - Fuselage Assembly (vertical supports)
Measure and cut the
vertical support pieces
from 1/4” square strip,
using shorter lengths
first. Take care to match
the angles for a good
fit. Pin these in position
and glue into place.
Step 41 - Fuselage Assembly (diagonal supports)
Measure and cut the diagonal support pieces from 1/4” square
strip, using shorter lengths first. Take care to match the angles for a
good fit. Pin these in position and glue into place.
Step 42 - Fuselage Assembly (stab support)
Measure and cut the
horizontal support for
the stab and it’s two
vertical supports from
1/4” square strip. Pin in
position and glue into
place.
Remove two G gussets from BP3. Glue together to form a 1/4”
thick piece. Glue in place.
Step 43 - Fuselage Assembly (pushrod exit)
Locate two of the EXIT
pieces from sheet BP2.
Glue one on top of
the other, then pin in
position and glue into
place.