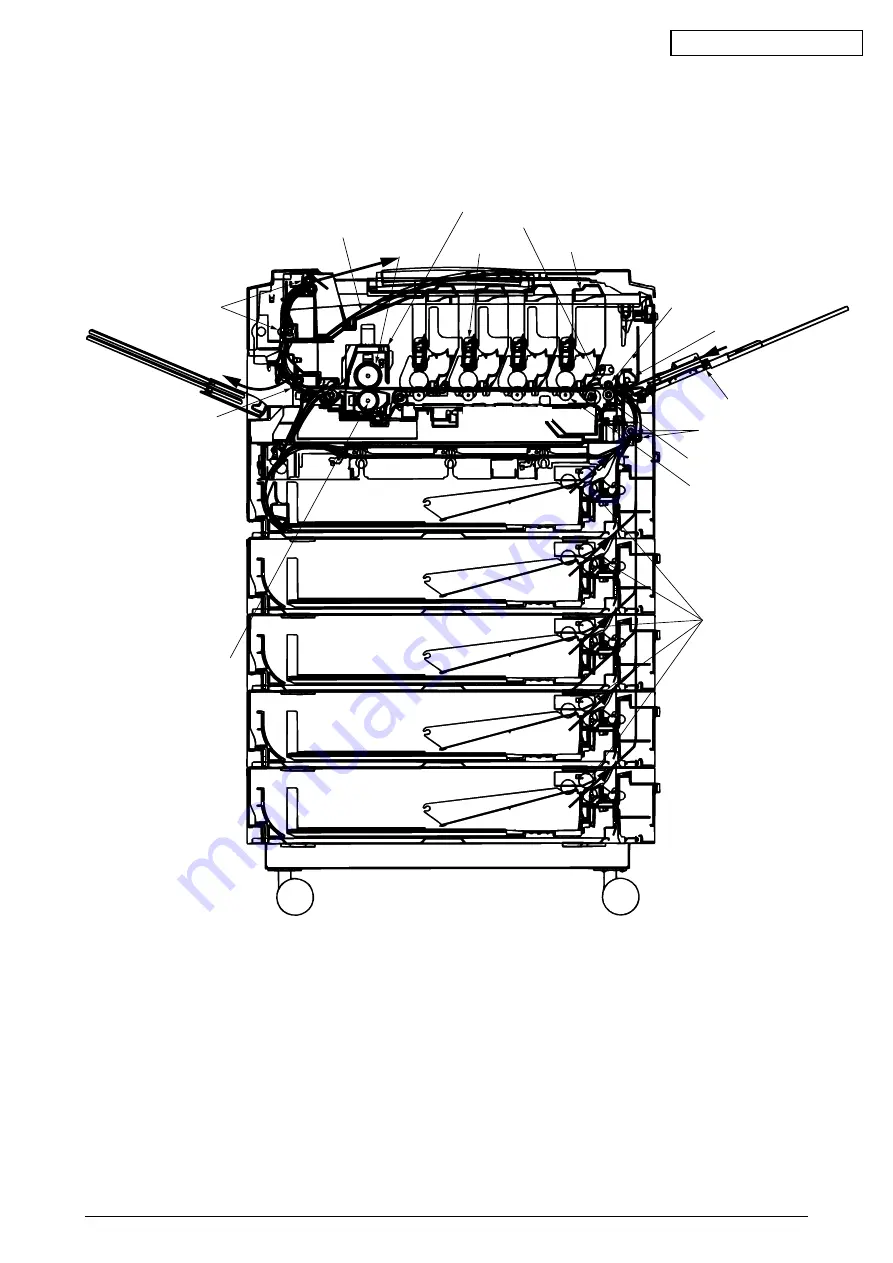
41956001TH Rev.1
26 /
Oki Data CONFIDENTIAL
2.4.2
Paper running process
Figure 2.5 shows how paper moves in the C9500/C9300.
Figure 2.5 Paper Route
Face-down stacker
Transfer roller
Backup roller
High-voltage power supply
Heat roller
Eject roller
Eject roller
Low-voltage power supply
4 x LED heads
4 x LED Units
Feed roller
Hopping roller
Cassette 1
Cassette 2
Cassette 3
Cassette 4
Cassette 5
Multipurpose tray
Registration roller Assy (B)
Registration roller Assy (B)
Registration roller Assy (A)
Cleaning blade
Fuser
Belt unit
Summary of Contents for C9300 Series
Page 48: ...41956001TH Rev 1 48 Oki Data CONFIDENTIAL 3 2 Parts Layout Figure 3 1 ...
Page 49: ...41956001TH Rev 1 49 Oki Data CONFIDENTIAL Figure 3 2 Top Cover Assy ...
Page 50: ...41956001TH Rev 1 50 Oki Data CONFIDENTIAL Figure 3 3 Printer Unit 1 2 ...
Page 51: ...41956001TH Rev 1 51 Oki Data CONFIDENTIAL Figure 3 4 Printer Unit 2 2 ...
Page 52: ...41956001TH Rev 1 52 Oki Data CONFIDENTIAL Figure 3 5 Cassette Guide Assy L R ...
Page 53: ...41956001TH Rev 1 53 Oki Data CONFIDENTIAL ...
Page 54: ...41956001TH Rev 1 54 Oki Data CONFIDENTIAL A B C D E A B C D E Figure 3 6 Duplex Unit ...
Page 112: ...41956001TH Rev 1 112 Oki Data CONFIDENTIAL Pattern 5 Pattern 6 Pattern 7 ...
Page 178: ...41956001TH Rev 1 178 Oki Data CONFIDENTIAL 37 26 33 38 32 39 38 31 34 35 36 27 Figure 8 1 3 3 ...