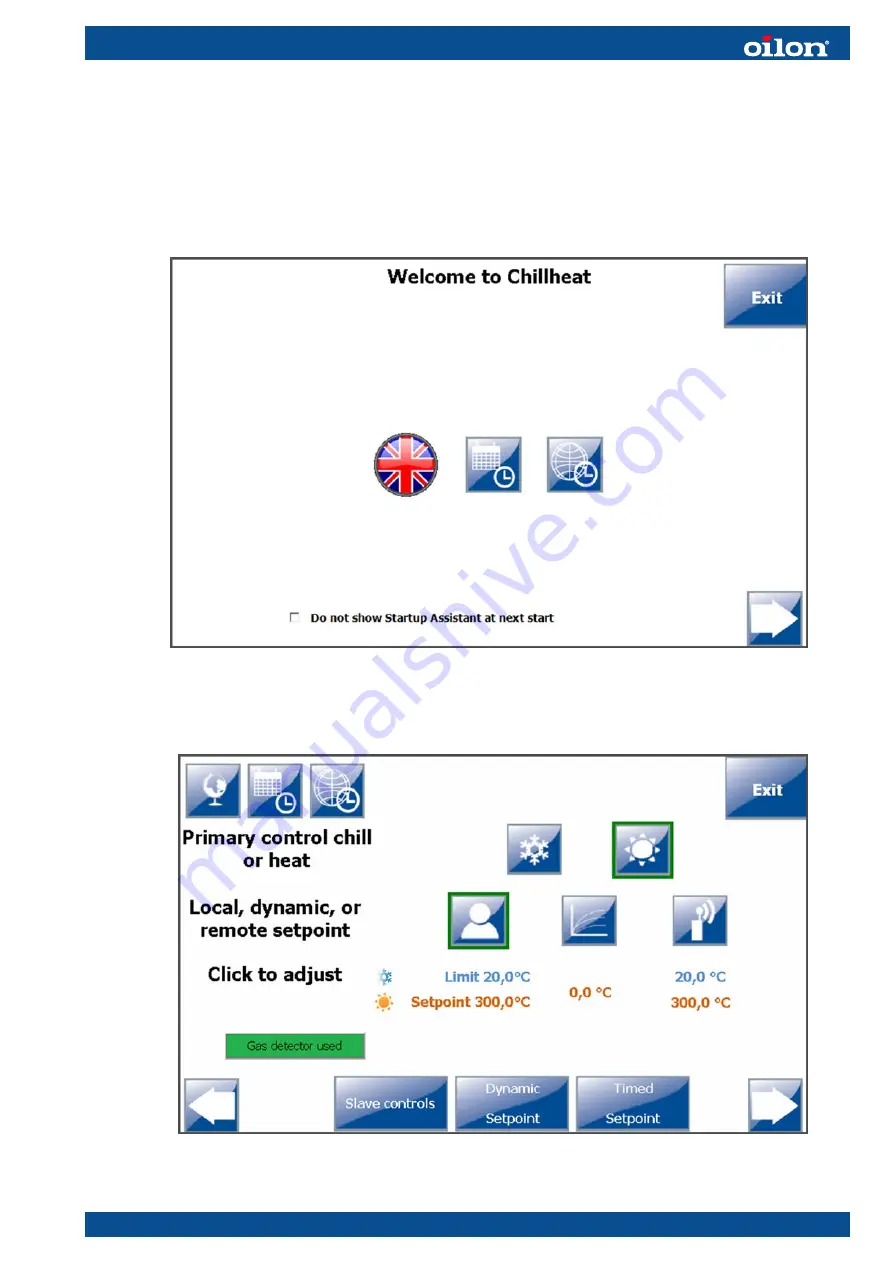
Reset and note down the initial setting.
12. Check that the communication interface is connected and correctly set up.
Refer to the instructions and settings in the Modbus communication list.
13. Check the settings of overcurrent protective devices.
4.7 First start-up
Set the language, time, and timezone.
Click arrow right to continue.
Set the power control options.
CHS01 1951EN
27 (63)