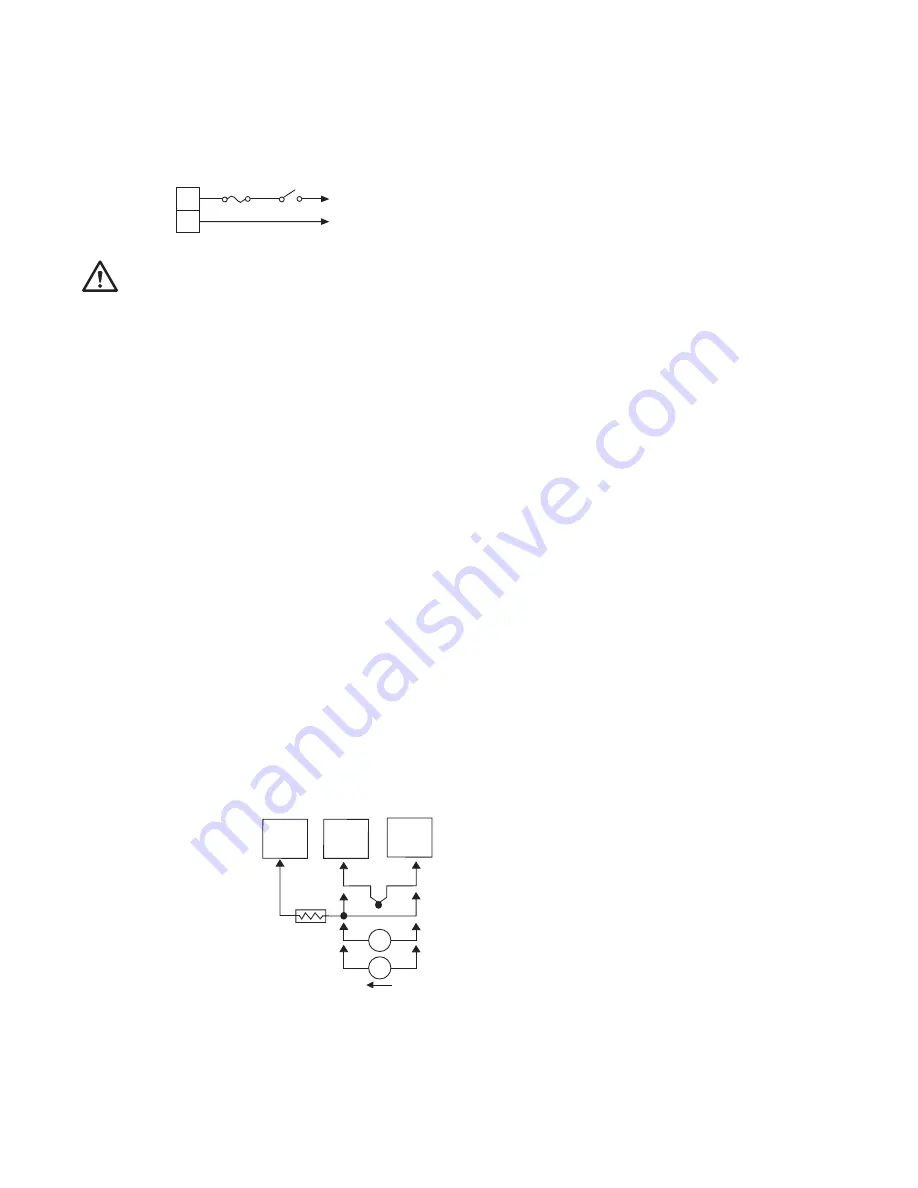
2-4 Power Wiring
2-4 Power Wiring
The controller is designed to operate at 11-26 VAC / VDC or 90-250 VAC. Check that the installation voltage
corresponds with the power rating indicated on the product label before connecting power to the controller. Near
the controller a fuse and a switch rated at 2A/250VAC should be equiped as shown in the following diagram.
The controller is designed to operate at 11-26 VAC / VDC or 90-250 VAC. Check that the installation voltage
corresponds with the power rating indicated on the product label before connecting power to the controller. Near
the controller a fuse and a switch rated at 2A/250VAC should be equiped as shown in the following diagram.
Figure 2.4 Power Supply Connections
Figure 2.4 Power Supply Connections
This equipment is designed for installation in an enclosure which provides adequate protection against
electric shock. The enclosure must be connected to earth ground.
Local requirements regarding electrical installation should be rigidly observed. Consideration should be given to
prevent from unauthorized person access to the power terminals.
This equipment is designed for installation in an enclosure which provides adequate protection against
electric shock. The enclosure must be connected to earth ground.
Local requirements regarding electrical installation should be rigidly observed. Consideration should be given to
prevent from unauthorized person access to the power terminals.
2-5 Sensor Installation Guidelines
2-5 Sensor Installation Guidelines
Proper sensor installation can eliminate many problems in a control system. The probe should be placed so that it
can detect any temperature change with minimal thermal lag. In a process that requires fairly constant heat output,
the probe should be placed close to the heater. In a process where the heat demand is variable, the probe should
be closed to the work area. Some experiments with probe location are often required to find this optimum position.
In a liquid process, addition of a stirrer will help to eliminate thermal lag. Since the thermocouple is basically a
point measuring device, placing more than one thermocouple in parallel can provide an average temperature
readout and produce better results in most air heated processes.
Proper sensor installation can eliminate many problems in a control system. The probe should be placed so that it
can detect any temperature change with minimal thermal lag. In a process that requires fairly constant heat output,
the probe should be placed close to the heater. In a process where the heat demand is variable, the probe should
be closed to the work area. Some experiments with probe location are often required to find this optimum position.
In a liquid process, addition of a stirrer will help to eliminate thermal lag. Since the thermocouple is basically a
point measuring device, placing more than one thermocouple in parallel can provide an average temperature
readout and produce better results in most air heated processes.
90
250 VAC or
11
26 VAC / VDC
~
~
Fuse
1
2
L
N
2A/250VAC
Proper sensor type is also a very important factor to obtain precise measurements. The sensor must have the
correct temperature range to meet the process requirements. In special processes the sensormight need to have
different requirements such as leak-proof, anti-vibration, antiseptic, etc.
Standard sensor limits of error are ±4 degrees F (± 2 degrees C ) or 0.75% of sensed temperature (half that for
special ) plus drift caused by improper protection or an over-temperature occurrence. This error is far greater than
controller error and cannot be corrected on the sensor except by proper selection and replacement.
Proper sensor type is also a very important factor to obtain precise measurements. The sensor must have the
correct temperature range to meet the process requirements. In special processes the sensormight need to have
different requirements such as leak-proof, anti-vibration, antiseptic, etc.
Standard sensor limits of error are ±4 degrees F (± 2 degrees C ) or 0.75% of sensed temperature (half that for
special ) plus drift caused by improper protection or an over-temperature occurrence. This error is far greater than
controller error and cannot be corrected on the sensor except by proper selection and replacement.
2-6 Sensor Input Wiring
2-6 Sensor Input Wiring
Figure 2.5 Sensor Input Wiring
Figure 2.5 Sensor Input Wiring
15
RTD
A
+
+
TC+
_
B
PTB
B
PTA
I
V
V+,mA+
PTB
_
TC
V ,mA
_
_
_
8
9
10