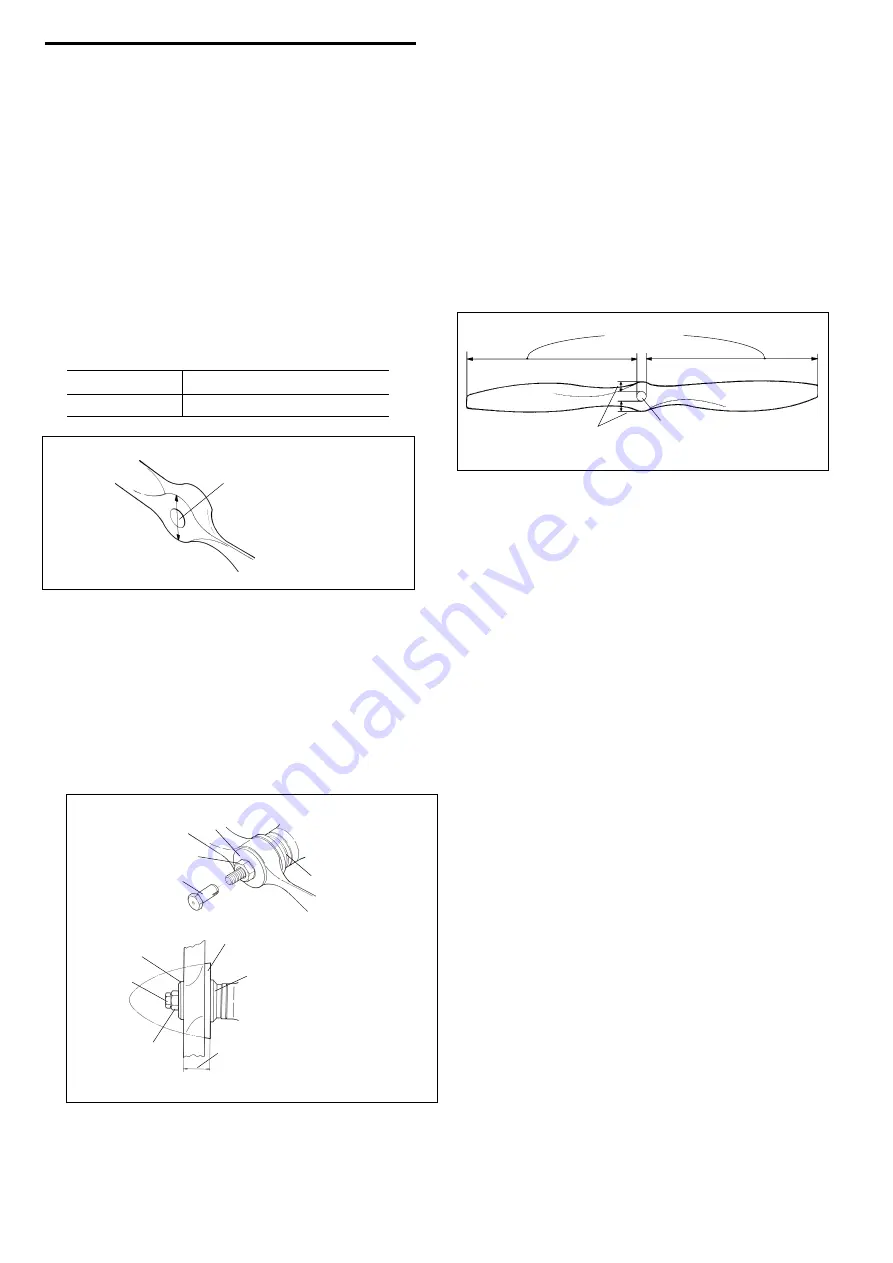
10
18x10-12, 20x8-10, 22x8
PROPELLER
The choice of propeller depends on the design and weight of
the aircraft and on the type of flying in which you will be
engaged. Determine the best size and type after practical
experimentation. As a starting point, refer to the props listed in
the accompanying table. Slightly larger, or even slightly
smaller, props than those shown in the table may be used, but
remember that propeller noise will increase if blade tip velocity
is raised, due to higher rpm or if a larger-diameter / lower-pitch
prop is used.
Make sure that the propeller is well balanced. An
unbalanced propeller and / or spinner can cause serious
vibration which may weaken parts of the airframe or
affect the safety of the radio-control system.
DO NOT forget the WARNINGS and NOTES on propeller
and spinner safety given on pages 2,3 and 4.
Warning:
Type
Size (DxP)
Sport/Scale
1.
PROPELLER & SPINNER ATTACHMENT
There is a risk, particularly with powerful four-stroke engines,
of the propeller flying off if the prop nut loosens due to
detonation ("knocking") in the combustion chamber when the
engine is operated too lean, or under an excessively heavy
load.
Obviously, this can be very hazardous. To eliminate such
dangers, the O.S. Safety Locknut Assembly was devised.
Install this as follows:
To be equal
To be equal
Ream to 12mm dia.
Fig. 8
Use a propeller that has a
hub of more than 40mm dia.
Fig. 9
Ream the propeller shaft hole to 12mm bore with an
appropriate reamer, checking that the hole is exactly
centered.
11
Install the prop to the engine shaft, followed by the retaining
washer and prop nut and tighten firmly with a 17mm
wrench. (not supplied).
2.
3. Add the special tapered and slotted locknut and secure
with a 12mm wrench while holding the prop nut with the
14mm wrench. (not supplied).
Propeller washer
Propeller washer
Propeller nut
Propeller nut
Locknut
Locknut
Drive hub
Drive hub
Back-plate of spinner
The Safety Propeller Locknut can
be used provided that the width is
between 21.5mm and 26mm.
Fig. 10
Make a habit of always checking the tightness of the
propeller before starting the engine. Remember that,
especially with wooden propellers, there is a tendency for
the material to shrink, or for it to be reduced by the
serrated face of the drive hub. Retighten the propeller nut
if necessary after loosening the Safety Propeller Locknut.
The locknut should be tightened firmly after retightening
the propeller nut.
NOTE: