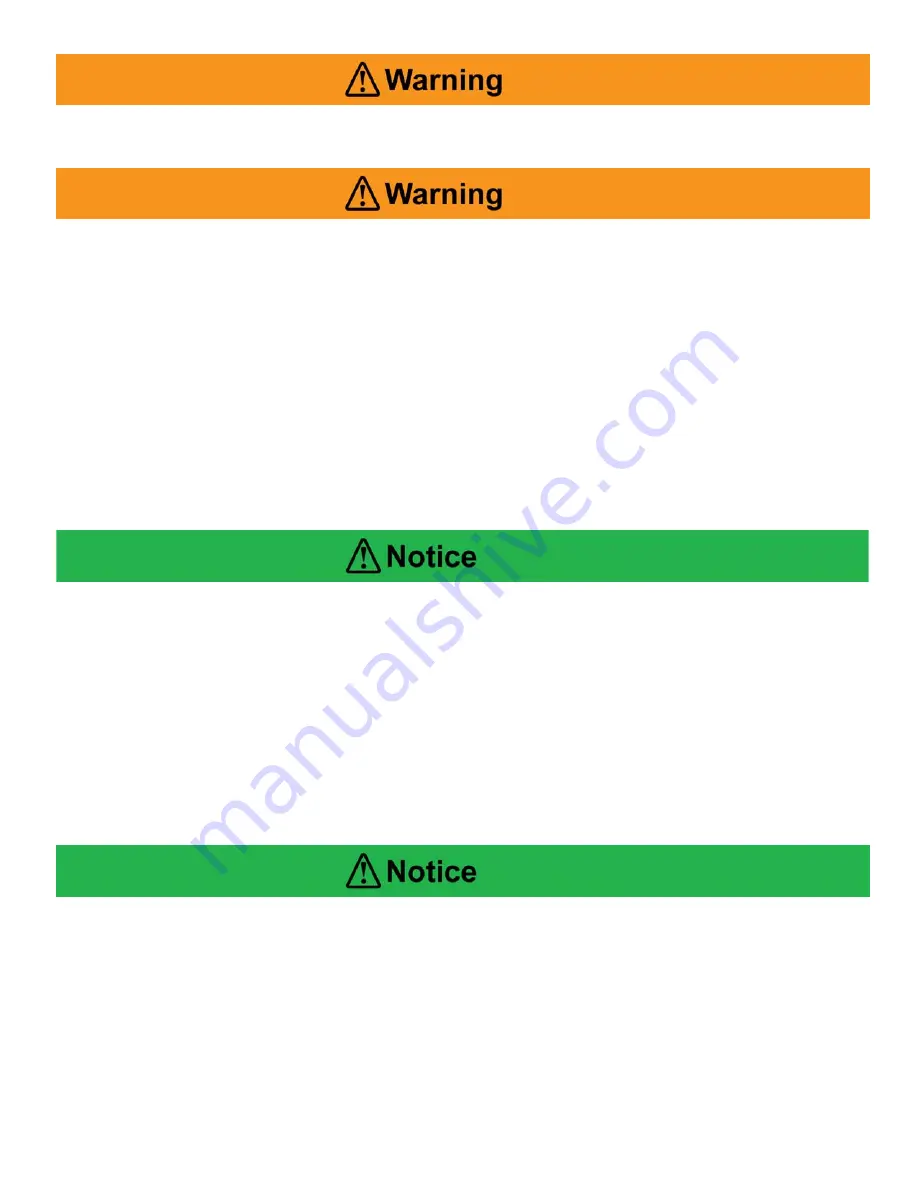
Open
Vertical
Electric
30
www.nuvair.com
Should the compressor, or a part of it, be out of service its parts must be rendered harmless
so they do not cause any danger.
Bear in mind that oil, filters or any other compressor part subject to differentiated waste
collection must be disposed of in compliance with the standards in force.
20.1 Waste Disposal
Use of the compressor generates
waste
that is classified as
special
. Bear in mind that
residues from industrial, agricultural, crafts, commercial and service activities not classified by
quality or quantity as urban waste must be treated as special waste. Deteriorated or obsolete
machines are also classified as special waste. Special attention must be paid to active carbon
filters as they cannot be included in urban waste: observe the waste disposal laws in force
where the compressor is used. Bear in mind that it is compulsory to record loading/unloading
of exhausted oils, special wastes and toxic-harmful wastes that derive from heavy/light industry
processes. Exhausted oils, special wastes and toxic-harmful waste must be collected by
authorized companies. It is especially important that exhausted oils be disposed of in
compliance with the laws in the country of use.
Disassembly and demolition must only be carried out by qualified personnel.
20.2 Dismantling the compressor
Dismantle the compressor in accordance with all the precautions imposed by the laws in force
in the country of use. Before demolishing request an inspection by the relevant authorities and
relative report. Disconnect the compressor from the electrical system. Eliminate any interfaces
the compressor may have with other machines, making sure that interfaces between remaining
machines are unaffected. Empty the tank containing the lubricating oil and store in compliance
with the laws in force. Proceed with disassembly of the individual compressor components and
group them together according to the materials they are made of: the compressor mainly
consists of steel, stainless steel, cast iron, aluminum and plastic parts. Then scrap the
machine in compliance with the laws in force in the country of use.
At every stage of demolition observe the safety regulations contained in this manual carefully.