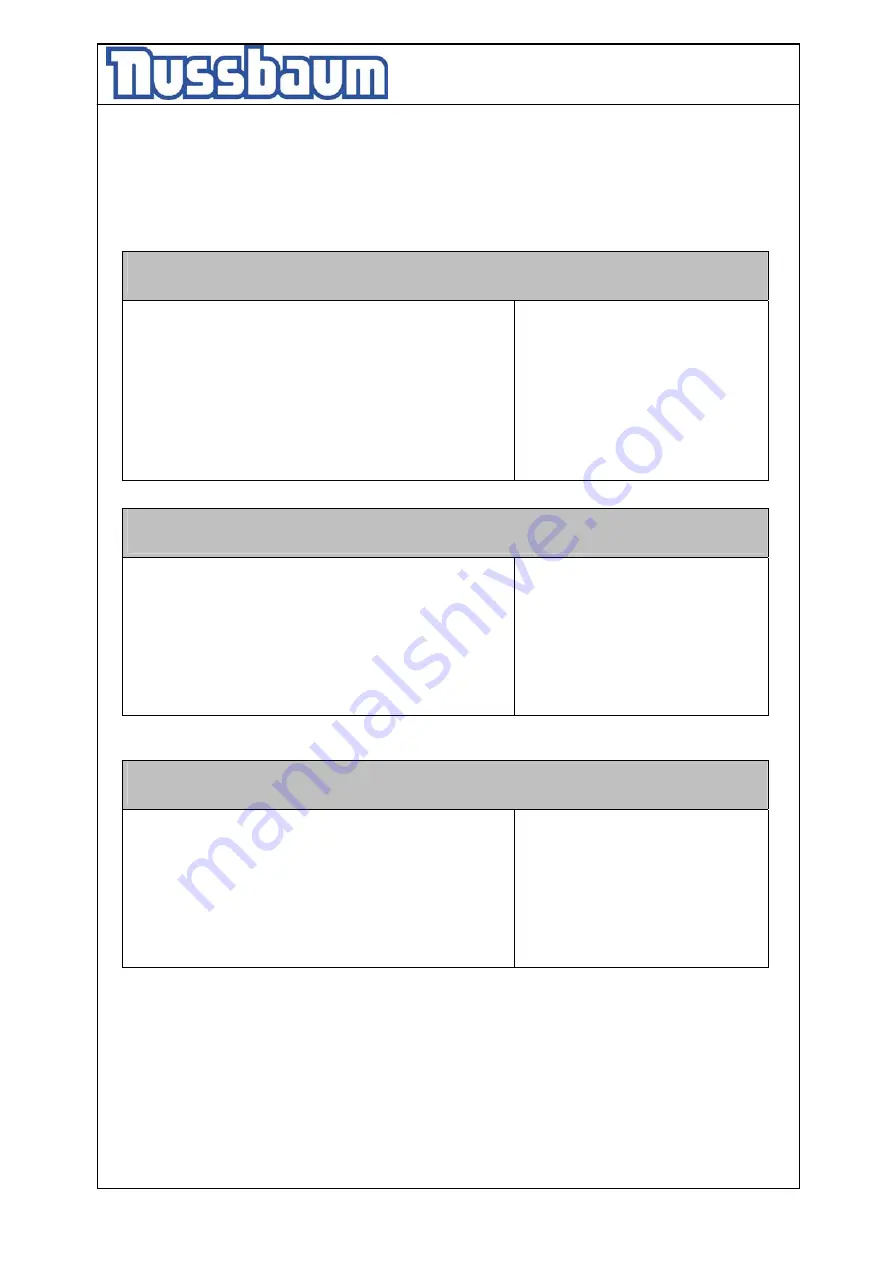
Operating Instruction and Documentation
UNI-LIFT 2500
- 14 -
6. Troubleshooting
If the lift does not work properly, the reason for this might be quite simple. Please check
the lift for the potential reasons mentioned on the following pages. If the cause of
trouble cannot be found, please call the technical service
.
Problem: Motor does not start!
Possible causes:
No power supply
main switch is not engaged or defective
fuse faulty
feed line is cut
thermal switch in the motor is active
Optional: Top-limit switch is faulty
Motor faulty
Solution:
check the power supply
check the main switch
check the fuse
check and repair it
let it cool down
Check the top-limit switch
Call the service partner
Problem: Motor starts, the lift does not raise!
Possible causes:
The vehicle is too heavy
The oil level is too low
Emergency lowering screw is not closed
Defective hydraulic valve
Gear pump is defective
Coupling from the motor is faulty
Solution:
unload the vehicle
refills
check the screws
Call the service partner
Call the service partner
Call the service partner
Problem: The automotive-lift does not lowered
Possible causes:
automotive-lift is on a obstacle
Hydraulic valve is faulty
Main fuse is faulty
The safety ratchet is locked
The lever or the valve is faulty
Optional CE-Stop limit switch is faulty
Solution:
(read chapter 6.1)
Kundendienst benachrichtigen
Sicherungen prüfen lassen
Raise the lift and lower again
Check the limit switch
6.1 Driving on an obstacle
If the slave side of the lift is running onto an obstacle during lowering and the hydraulic
tube has no more pressure, the pressure switch is activated and the lift stops self-instructed.
Raise the lift, push lever “lifting“ until the obstacle can be removed.
If the master side of the lift is running onto an obstacle during the lowering the lift stops
mechanically. Raise the lift, push lever “lifting“ until the obstacle can be removed.
Summary of Contents for UNI-LIFT 2500
Page 9: ...Operating Instruction and Documentation UNI LIFT 2500 9 2 5 Page for notice...
Page 11: ...Operating Instruction and Documentation UNI LIFT 2500 11 3 3 Data sheet...
Page 37: ...Operating Instruction and Documentation UNI LIFT 2500 37 Electrical diagram drawing...
Page 38: ...Operating Instruction and Documentation UNI LIFT 2500 38...
Page 39: ...Operating Instruction and Documentation UNI LIFT 2500 39...
Page 41: ...Operating Instruction and Documentation UNI LIFT 2500 41...
Page 42: ...Operating Instruction and Documentation UNI LIFT 2500 42...
Page 43: ...Operating Instruction and Documentation UNI LIFT 2500 43...
Page 44: ...Operating Instruction and Documentation UNI LIFT 2500 44 Hydraulic diagram drawing...