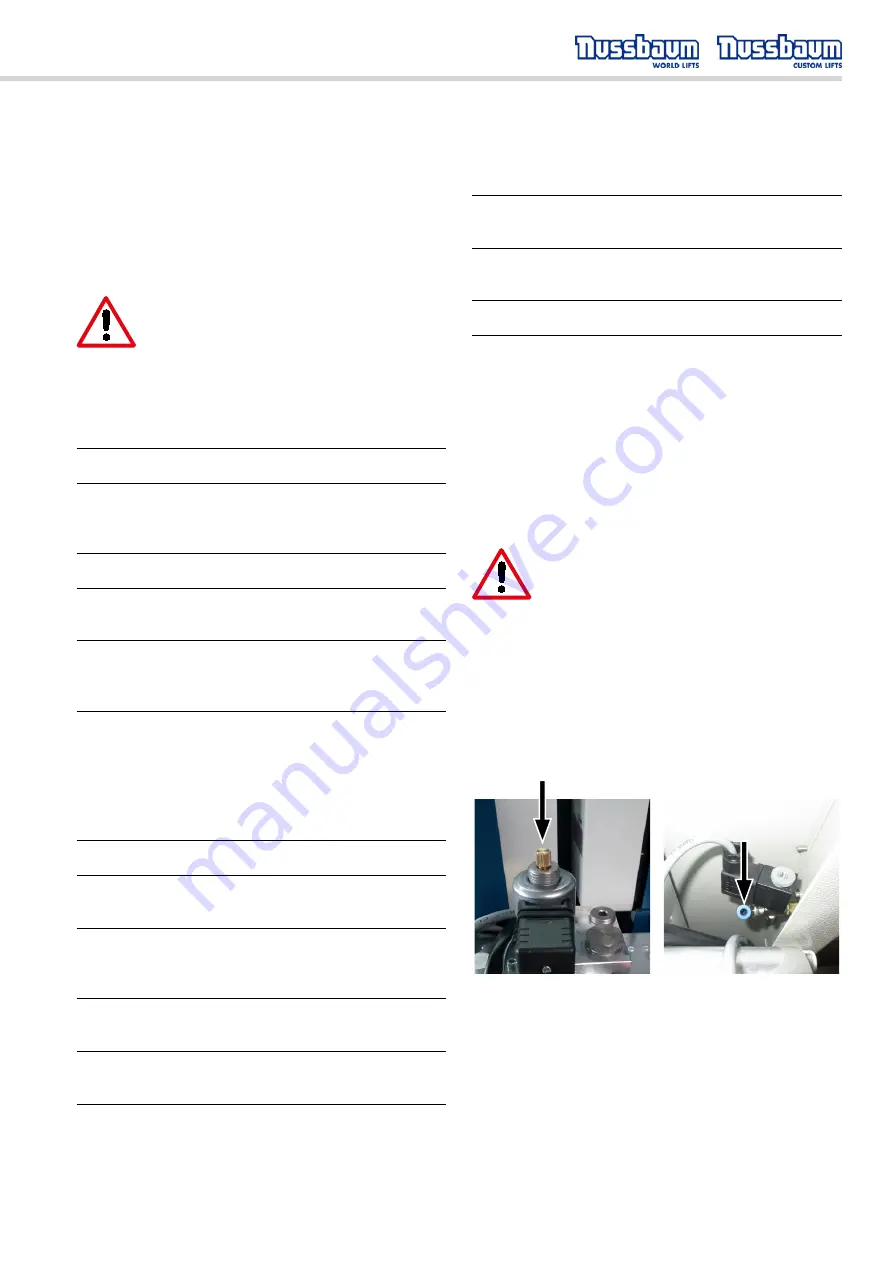
OPI_TOP LIFT TSK 8000_V3.2_EN
23
6 Behaviour in cases of error
Defective operational readiness of the lift may be
due to a simple error. Check the system for the list-
ed sources of error.
If the error cannot be removed after an inspection
to the named causes, then inform customer service
or your dealer.
Independent repair work on safety
devices of the lift and checking the
electrical system may only be done
by specialists.
Problem: Motor does not start
Possible causes:
Remedy:
No power supply
Check the power supply
The main switch is not
switched on, or is de-
fective
Check main switch
Defective fuse
Have fuses checked
Power supply interrupt-
ed
Inform customer service
Thermal fuse of the mo-
tor is active
Let motor cool (cooling
time dependent on am-
bient temperature)
Motor defective
Inform customer service
Problem: Motor starts, load is not lifted
Possible causes:
Remedy:
The vehicle is too heavy Unload vehicle
Hydraulic oil filling level
is too low
Refill hydraulic oil
The emergency dis-
charge screw is not
closed
Check the emergency
discharge screws
Hydraulic valve defec-
tive
Inform customer service
Mechanical pump de-
fective
Inform customer service
The coupling between
the motor and pump is
defective
Inform customer service
Problem: The lift cannot be lowered
Possible causes:
Remedy:
Lifting table is sitting on
an obstacle
See Section 6.1
Hydraulic valve defec-
tive
Inform customer service
Defective fuse
Have fuses checked
Push button defective
Check push button
6.1 Moving onto an obstacle
If the lift drive-on rail/lift arm moves onto an obstacle
during lowering, then it remains in position due to the
mechanical resistance. By pushing the "Lift" button,
the lift can be raised again to remove the object.
6.2
Emergency discharge with external unit
and safety latch
An emergency discharge is an ac-
cess into the lift controls and may only
be done by experienced specialists.
The emergency discharge must be
done in the following described se-
quence, otherwise it can lead to
damage and hazard to life and limb.
Any kind of external leakage is not
permitted and must immediately tak-
en care of. This is absolutely neces-
sary especially before an emergency
discharge.
Fig. 2a (left): Hydraulic emergency lowering, re-move cap and
open valve
Fig. 2b (right): Pneumatic air supply for actuating the ratchet
cylinders.
6.2.1 Defect of the hydraulic valve
If there is a defect in the hydraulic valve there is still
the option of moving the lift to its lowest position so
the vehicle can be drive off the lift.
1. Push the “Lower” button and the latches must
unlock.
Summary of Contents for TSK 8000
Page 2: ...2 OPI_TOP LIFT TSK 8000_V3 2_EN...
Page 4: ......
Page 9: ...OPI_TOP LIFT TSK 8000_V3 2_EN 9...
Page 20: ...20 OPI_TOP LIFT TSK 8000_V3 2_EN...
Page 44: ...44 OPI_TOP LIFT TSK 8000_V3 2_EN...
Page 45: ...TOP LIFT TSK 8000 Serial No Made in Germany Spare parts list...