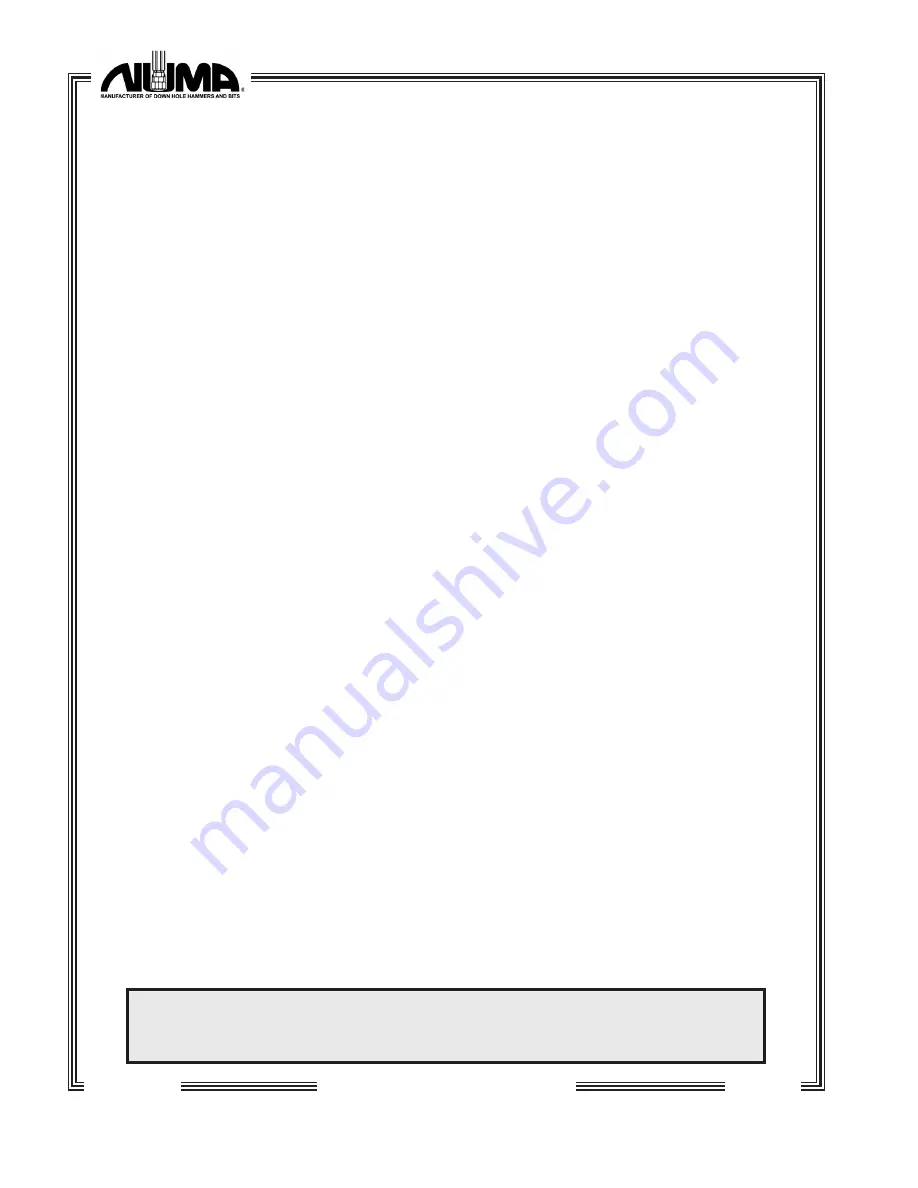
Page 12
04/21/20
Champion
®
RC300
HAMMER ASSEMBLY
•
Using the overhead crane, turn the hammer case upside down in a vertical position
so that the bit bearing bore is facing up.
•
Insert the bit bearing into the chuck end of the case. This should be a close slip fit.
Making sure the bearing makes contact with the shoulder provided for it in the case,
insert the snap ring into the groove at the chuck end of the bit bearing diameter.
•
Using the overhead crane, turn the hammer case so that the backhead end is facing
up. The hammer case should still be in a vertical position.
•
Lower the piston into the backhead end of the case using the 8" (203 mm) long steel
rods, 1.625" (41 mm) diameter steel rods and the nylon straps.
•
Install the feed tube assembly into the backhead end of the case, making sure it is
firmly against the shoulder in the case. Due to close tolerances, caution is advised
when inserting the feed tube assembly. It should not be forced into the case.
•
Install the belleville wahsers in the counter bore of the feed tube assembly. See the
stacking diagram on page 14 for proper installation.
•
Install the collection tube housing o-ring and the collection tube o-ring in the I.D. of
the collection tube housing.
•
Install the collection tube housing. The collection tube housing will rest on the belleville
washers.
•
Place the check valve spring and check valve on the collection tube housing.
•
Install the check valve seat o-ring into the groove on the outside diameter of the check
valve seat.
•
Lower the check valve seat through the check valve and check valve spring. Make
sure the check valve seat is seated into the collection tube housing.
•
Assemble the backhead o-ring into the groove in the backhead. Install the collection
tube o-ring in the groove in the backhead on the drill rod mating end. With the thrust
washer installed on the case shoulder, thread the backhead into the case and tighten
until the shoulder is tight against the case.
•
Install the connector pin o-rings on the connector pins. Using a soft blow hammer, seat
the (2) connector pins into the flange openings on the top of the backhead.
NOTE
DUE TO THE INTERNAL COMPRESSION SPRINGS, THE CHAMPION RC300 BACKHEAD
CAN ONLY BE FULLY TIGHTENED WITH A POWER WRENCH ON THE RIG.
Summary of Contents for Champion RC300
Page 2: ......