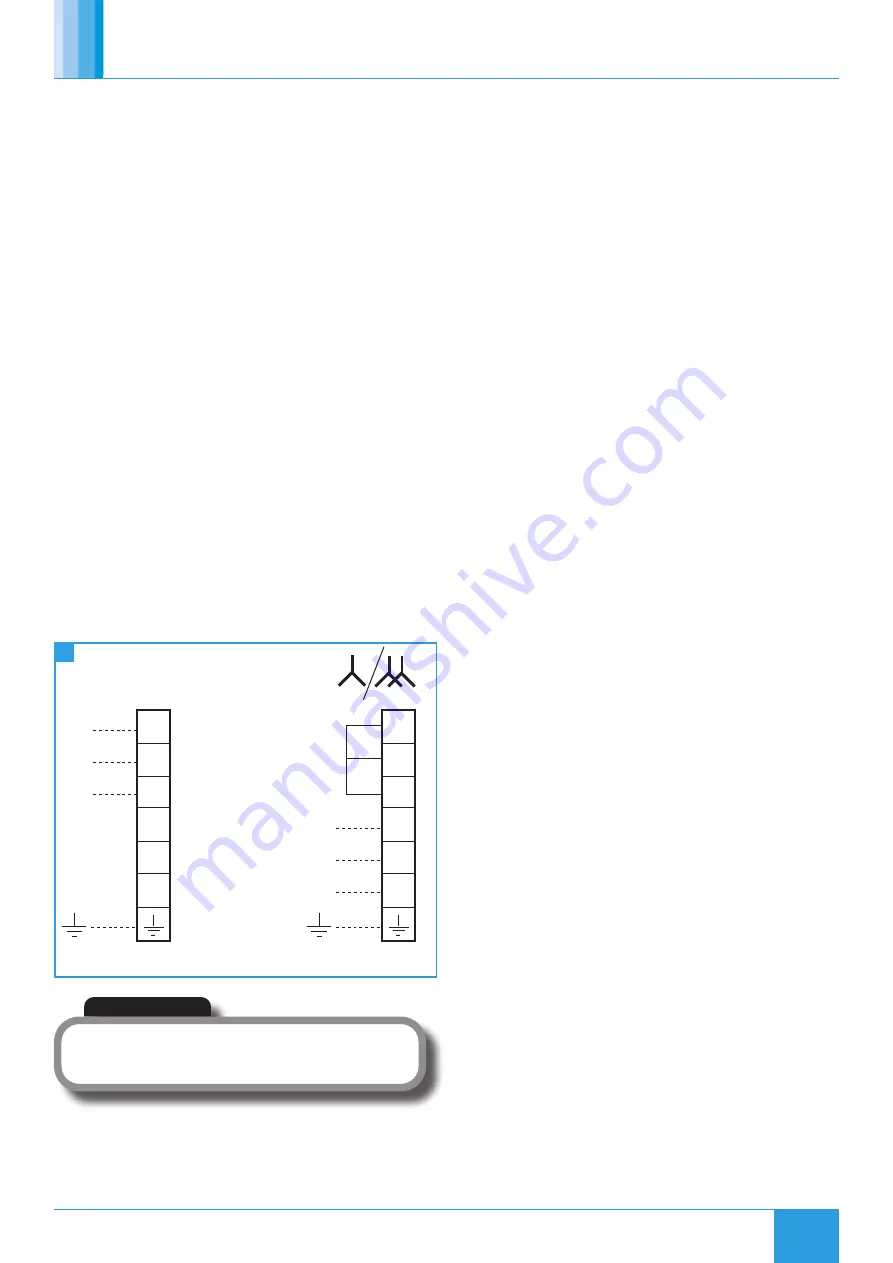
04. 02. 20. Document Number 671712
4
Nuaire |
Western Industrial Estate
|
Caerphilly
|
CF83 1NA
|
nuaire.co.uk
SVT28
Installation Manual
6.0 ELECTRICAL INSTALLATION
Motors are totally enclosed and protected to IP55 (Dust and low
pressure water jets). Motors comply with BS5000, EN600034 and
IEC34-1. Enclosures are to IP55 with class H insulation. Motors are
tested in accordance with EN12101-3 2015.
Note the requirements for maintenance of the motor. Failure to
comply with the recommendations will invalidate any warranty
claim.
6.1 Wiring
Electrical supply wiring connection is to an externally mounted
terminal box on the case exterior. The box is pre-wired to the motor
with heat resisting cable. If a two speed starter is used it must have 3
contactors. Individual wiring diagrams are included with each unit.
A matched Nuaire Inverter Speed Control is available. Please contact
Nuaire.
6.2 Two Speed Motors
Two speed motors are supplied TAP or PAM single winding. All two
speed types are designed for Direct-On-Line (D.O.L) starting on both
speeds only unless otherwise specified
N.B. TAP wound motors require a three contactor control. Individual
wiring instructions are included with each unit.
6.3 Connection Details
Check that the voltage full load and starting current on the fan rating
label is suitable for your supply.
6.3.1 Two Speed - TAP/PAM WOUND MOTOR D.O.L Starting
(Both Speeds), 3 phase
1U
1V
1W
2U
2V
2W
400V 3 phase
50Hz supply
Link
(if no control
is used)
High speed
Low speed
L1
L2
L3
1U
1V
1W
2U
2V
2W
L1
L2
L3
6
Wiring - Three Phase - Two Speed TAP/PAM
Wound Motor D.O.L Starting (Both Speeds)
IMPORTANT
For good EMC engineering practice, any sensor cables or
switched live cables should not be placed within 50mm of
other cables or on the same metal cable tray as other cables.
6.4 Start Up Procedure
Ensure that the impeller rotation follows the label arrow indicator
on the casing. Should the direction be incorrect on three phase units,
reverse any two of the supply leads. Care should be taken to set correct
rotation as incorrect rotation may result in damage to the motor.
Equipment should be run for approx. 30 minutes to ensure correct
operation. If any fault occurs, the equipment should be switched off. Do
not re-start until the fault has been rectified.
7.0 SPECIFIC COMMISSIONING AND SERVICING
REQUIREMENTS
Motors for Smoke Extract Fans
Exposure temperature/time: 300°C for 2 hours / 400°C for 2 hours
These motors are used to provide a SAFETY FUNCTION for people
in the event of fire in public premises or in the home: they are
therefore subject to strict constraints concerning their operating and
maintenance.
Operating Constraints
i. Check on the nameplate that the selected motor corresponds to
the maximum exposure temperature and duration.
ii. Non ventilated motors MUST be placed in the airflow from the
driven fan. Ventilated motors can be placed outside the flow.
iii. AFTER THE MOTOR HAS BEEN SUBJECTED TO ONE EMERGENCY
DUTY OPERATION, IT MUST BE REPLACED.
iv. With variable speed control. Ensure that the maximum speed never
exceeds the speed of the motor supplied by the mains and that the
delivered power corresponds to the previous definitions.
These qualifications ensure the qualification of the driven fan by
the manufacturer.
Maintenance Constraints
Regular service visits must be performed on the installation AT
LEAST EVERY 6 MONTHS, incorporating the following checks:
i. Checking insulation resistance (R>100 MOhms, 500V DC)
•
If the drain holes are blocked, open them to eliminate any
accumulated condensation.
•
If R<100 MOhms, dry the stator in an oven and check the
insulation resistance. If the fault persists, replace the stator.
•
The stator must be replaced 5 years after installation or after
20,000 hours of operation.
ii. Cooling check
•
Ensure there is no dust or grease in the entire ventilation circuit
(housing fins, motor cover/fan if fitted driven fan).
•
Ensure the motor runs normally when switched on for a few
minutes.
iii. Bearing check (C3 or C4 play)
Run the motor during each maintenance visit. When the motor is cold,
a high level of noise is caused by the texture of the grease. This does
not indicate a bearing fault.
iv. S2 duty only:
The bearings must be replaced by an identical type every 5 years.
Ensure the motor runs normally when switched on for a few
minutes.
v. Fixing Check
During regular maintenance, check all fixtures and fittings to ensure
they have remained secure and in good working order.