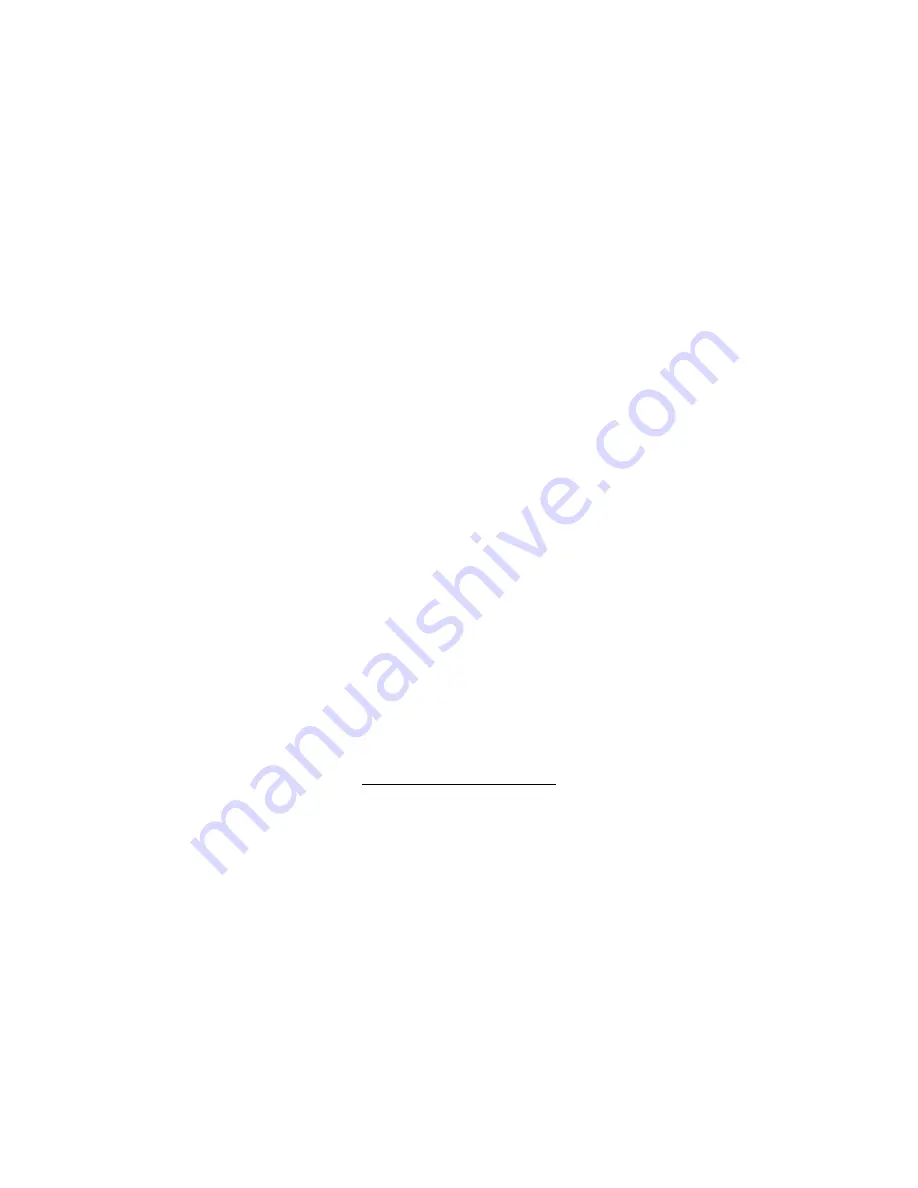
OM0291
Page 27 of 56
Rev 3 November2020
6.3 Operating Sequence
6.3.1 Start Up
Turn on cabinet blower and lights and check air intake and exhaust portals of the cabinet to make sure they are
unobstructed. The electronic airflow control system will automatically control airflows to specified setpoints.
However, upon filter loading, the cabinet may be required to be re-balanced or filters replaced. Only a qualified
maintenance technician should perform cabinet balancing and filter replacement.
Allow blowers to operate for a minimum of 15 minutes before aseptic manipulations are begun in the cabinet. If
the filtered air exhausted from the cabinet is discharged into the room, as in some installations, an additional
advantage is obtained from purification (filtration) of the room air circulated through the equipment. Because of
this characteristic contributing to the quality of the laboratory environment, some owners of AHBSC’s leave them
in operation beyond the time of actual use.
6.3.2 Wipe Down
The interior surfaces of the workspace should next be disinfected (see Cleaning Procedures) by wiping them
thoroughly with 70% alcohol or similar non-corrosive anti-microbial agents. USE OF CHLORINATED OR HALOGEN
MATERIALS IN THE CABINET MAY DAMAGE STAINLESS STEEL.
6.3.3 Materials and Equipment
The apparatus and materials should next be placed into the cabinet. Care must be exercised that no items be
placed over the front intake grills. Materials should be arranged so that clean, dirty (used), and virus materials are
well separated. Passage of contaminated materials over uninoculated cultures or clean glassware should be
avoided and transfer of viable materials should be performed as deeply into the cabinet (away from open face) as
possible.
6.3.4 Air Purge
Additional purging of the workspace without user activity should be allowed for 2-3 minutes after materials and
apparatus have been placed in it. This will rid the area of all "loose" contamination that may have been introduced
with the items.
6.3.5 Perform Work
The work can now be performed. The technician performing the work is encouraged to wear a long-sleeved gown
with knit cuffs and rubber gloves. This will minimize the shedding of skin flora into the work area and concurrently
protect the hands and arms from viable agent contamination. At a minimum, the hands and arms should be
washed well with germicidal soap before and after work in the cabinet. For the preparation of antineoplastic
drugs, the following procedures summarize those contained in OSHA Technical Manual TED 1-0.15A, Section VI,
Chapter 2 “Controlling Occupational Exposure to Hazardous Drugs”. The above document should be thoroughly
studied and reviewed prior to drug preparation in the cabinet.
It may be found at this website. http://www.osha.gov/dts/osta/.
a. A sterile plastic-backed absorbent drape should be placed on the work surface during mixing procedures.
The drape should be exchanged whenever significant spillage occurs, or at the end of each production
sequence.
b. Vials should be vented with a filter needle to eliminate internal pressure or vacuum.
c. Before opening ampoules, care should be taken to insure that no liquid remains in the tip of the ampoule.
A sterile gauze sponge should be wrapped around the neck of the ampoule while opening.
d. Final drug measurement should be performed prior to removing the needle from the stopper of the vial.
e. A non-splash collection vessel should be available in the AHBSC to discard excess drug solutions.
Summary of Contents for LabGard NU-640-400
Page 7: ...OM0291 Page 7 of 56 Rev 3 November2020...
Page 9: ...OM0291 Page 9 of 56 Rev 3 November2020...
Page 10: ...OM0291 Page 10 of 56 Rev 3 November2020...
Page 11: ...OM0291 Page 11 of 56 Rev 3 November2020...
Page 15: ...OM0291 Page 15 of 56 Rev 3 November2020...
Page 20: ...OM0291 Page 20 of 56 Rev 3 November2020...