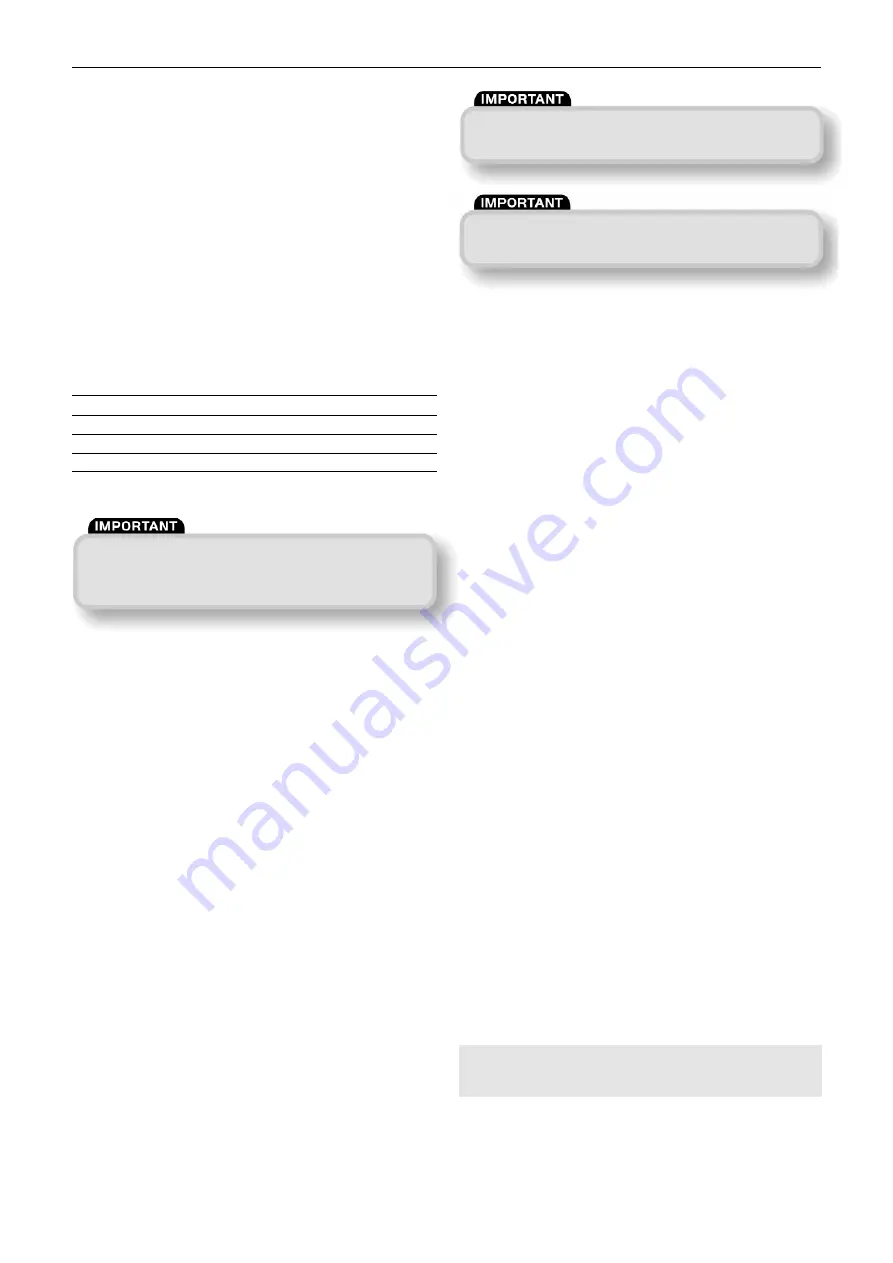
Unit must not be switched off, product is
designed to run continuously.
4
For good EMC engineering practice, any sensor cables
or switched live cables should not be
placed within 50mm of other cables or on the same
metal cable tray as other cables.
Leaflet Number 671390 July 2011
Installation and Maintenance
LPXBOXDC-2 Mechanical Ventilation with Heat Recovery
WARNING - Before commencing work, electrically
isolate the fan unit from the mains supply.
6.0 Maintenance
It is inevitable that even with filtered extract grilles as
recommended in BRE digest 398 some dust, fluff etc. will
pass through the filter, and which, if allowed, will build up
internally on motors and impellers, shortening the life of
the unit and, in severe cases, leading to overheating of the
motors. Consequently, it is strongly recommended that all
units are inspected and cleaned every six months.
7.0 Cleaning
Remove covers and carefully clean out interiors as
necessary. To clean the filter, remove from the unit and
wash in tepid water to which a little mild detergent has
been added. Shake out excess water and allow to dry
naturally. Replace when dry. Check for damage and
security of components. Refit covers.
8.0 Replacement of Parts
Should any component need replacing Nuaire keep extensive
stocks for quick delivery. Ensure that the unit is electrically
isolated, before carrying out any work.
When ordering spare parts, please quote the serial number
of the unit and the ARC number of the purchase if possible.
(This information will be available on the fan label).
9.0 Warranty
The 5 year warranty starts from the day of delivery and
includes parts and labour for the first year and parts only
for the remaing four years. This warranty is conditional on
planned maintenance being undertaken.
10.0 Service Enquiries
Nuaire can assist you in all aspects of service. Our service
department will be happy to provide any assistance required,
initially by telephone and If necessary arrange for an
engineer to call.
Customer Services Department
on 08705 002 555
4.0 Setting to Work
Each fan is factory set to operate at trickle airflow when
power is applied and switch over to the boost flow rate
when a switched live signal is present. The pot marked ‘MIN
Airflow’ adjusts the trickle flow rate and the boost flow rate
by the pot marked ‘MAX Airflow’. These flow rates for the
supply and extract fan are adjusted separately. When the
switched live signal is removed, the fan will continue to run
at boost flow rate for a preset period as dictated by the pot
marked ‘RUN-on’.
Work out the required flow rate for the supply and extract
fans (these are usually supplied by the design consultant)
and adjust the approprate pots. If these figures are not
available, please refer to the typical settings below.
No. of
Typical volume of
Trickle/normal
Boost
Bedrooms
ventilated space
flow rate l/s*
flow rate l/s*
1
140m
3
19
24
2
200m
3
28
35
3
260m
3
36
45
4
320m
3
44
56
*These figures are given as a general guide. They should only be
used if actual design figures are not available.
5.0 Run-on Timer
The Run-on timer adjustment is from 0 - 60 mins.
Run-on is
only available from the switched live (SL) signal.
5.1 Start-up Routine
On power up or and after power failure the unit goes
through a 2 minute set-up period.
During this period the unit:
1. Starts at full speed
2. Ramps down to off
3. Restarts at 25% speed
4. Resumes normal operation
5.2 Status Light
Green light - Fan running
Red light - Fan failure
Flashing green light - Set-up period
Flashing red light - Electronics failure or insufficient
pressure reading, check ducting/installation
e.g. please remove inlet/outlet ducting and test
5.3 Calibration
By pressing the calibration button the unit re-sets itself by
switching off for 30 seconds then re-starts at full speed
before ramping down to the desired duty. Whilst running at
full speed the status light flashes to indicate if the duty set
on the adjustment dials can be achieved (green for yes,
amber for no). Checks can be carried out in both the trickle
and boost modes. If the light flashes amber check the
resistance of the ducting, grilles etc. or turn down the
adjustment dial.