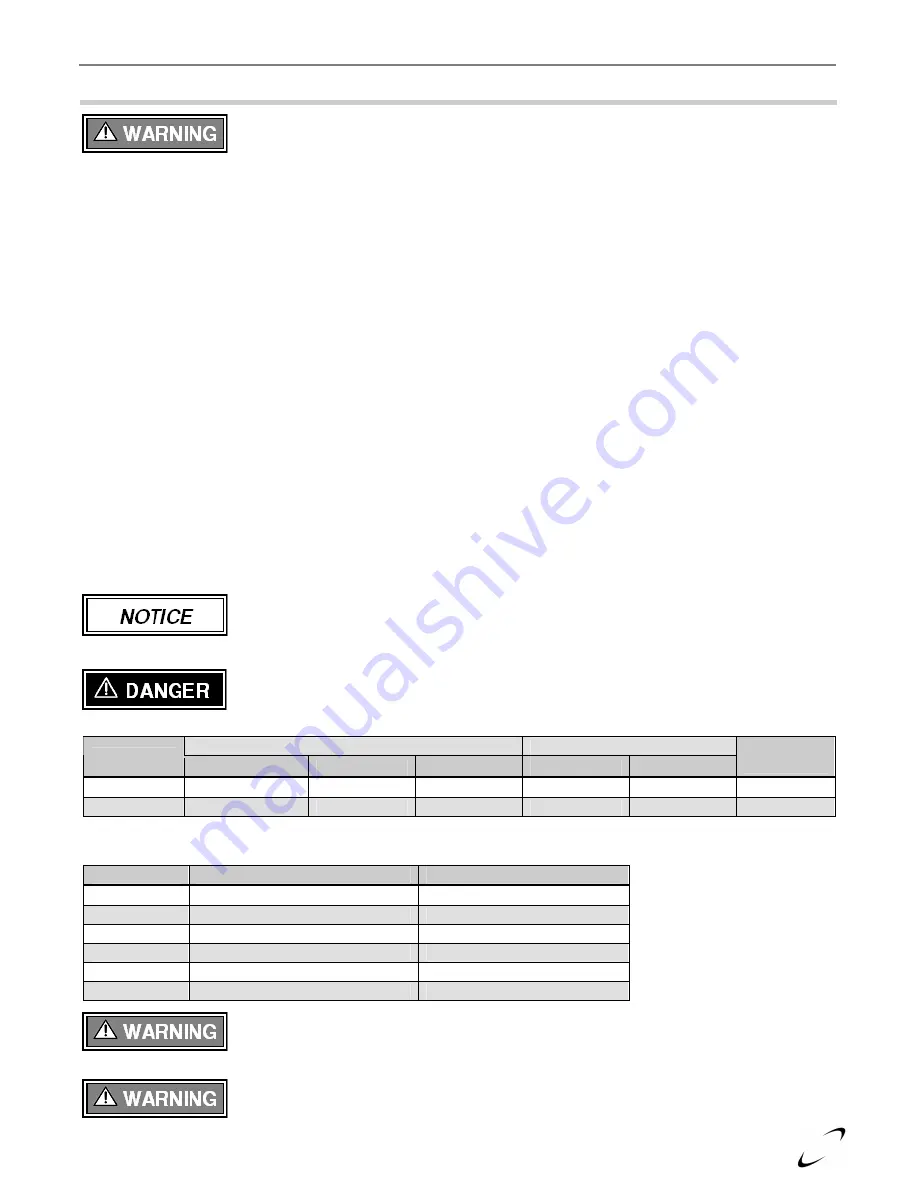
Lx Series Installation and Operation Instructions
│
Trinity Lx
33
9.0
GAS VALVE AND BURNER SET-UP
The Trinity Lx gas valve must be set-up by a licensed Gas Technician. Improper set-up
may result in incorrect operation, damage to components or property, injury or death.
Gas Line Pressure
The appliance gas valve is equipped with a line pressure test port; see Figures 9-1 through 9-4. Use the following
procedure to measure the gas line pressure to the appliance to ensure if falls within the range given in Table 9-1:
1.
Turn the supply of gas to the appliance off.
2.
Open the bleed screw of the line pressure test port approximately 1-1/2 turns (Lx150-400 models). This
port is directly connected to the gas line feeding the appliance. For Lx800 models, replace 1/8” NPT plug in
the inlet flange of the gas valve with a hose barb fitting suitable for manometer tubing used. See Figure 9-4.
3.
Force 1/4
"
ID tubing over the housing of the line pressure test port; install the other end of the tubing to an
appropriate line pressure test gauge or manometer. Ensure both ends of the tubing make a tight connection.
4.
Open the supply of gas to the appliance and check for gas leaks.
5.
Observe the line pressure under static conditions and compare it to Table 9-1. The pressure will be greatest
under static conditions.
6.
With all other gas appliances in the applications running, operate the burner to the maximum firing rate
(See Table 9-2) and compare the observed line pressure with Table 9-1. The pressure will be lowest during
the maximum flow of gas.
7.
Adjust the gas line pressure to ensure the parameters in Table 9-1 are attained under all conditions. If
possible adjust the line pressure to the "Nominal/Desired" value listed in Table 9-1, while the unit is
operating at the maximum modulation rate, see Table 9-2.
8.
Continue observing the gas line pressure until the completion of the combustion analyses, incase
adjustments need to be made.
9.
Upon completion of the line pressure testing, return the bleed screw of the Line Pressure Test Port to the
closed position. For the Lx800, replace the installed hose barb fitting with the factory 1/8” NPT plug; use
NG/LP approved thread sealant.
The line pressure is a function of the gas supply and is affected solely by field provided
parameters such as line size and regulator settings. Under no circumstances can the
appliance gas valve influence or be used to adjust the gas line pressure.
Failure to close the bleed screw of the Line Pressure Test Port will cause a severe leakage
of gas, resulting in a fire or explosion causing property damage, serious injury or death.
Table 9-1 Line Pressure and Combustion Parameters
Line Pressure (inches wc)
CO
2
(%)*
Gas
Nominal/Desired
Min.
Max.
Min.
Max.
CO (ppm)
Max.
Natural
7
4
10.5
8.5
9.5
175
Propane
11
8
13
9.5
10.5
175
*Note: it is permissible to have higher CO
2
values with the burner operating at the minimum modulation rate.
Table 9-2 Minimum and Maximum Modulation Rates
Model
Min. Modulation Rate (RPM)
Max. Modulation Rate (RPM)
Lx150
1150
5850
Lx150E
925
4450
Lx200
925
5950
Lx300
1250
5850
Lx400
1550
7250
Lx800
1250
5300
Carbon Monoxide - Never leave the unit operating while producing Carbon Monoxide
(CO) concentrations in excess of 175ppm. Failure to follow this warning may result in
serious injury or death.
Manifold Pressure - DO NOT adjust or measure the Manifold Pressure of the appliance.
Correct manifold pressure is factory set. Field adjustment could result in improper burner
operation resulting in fire, explosion, property damage or death.