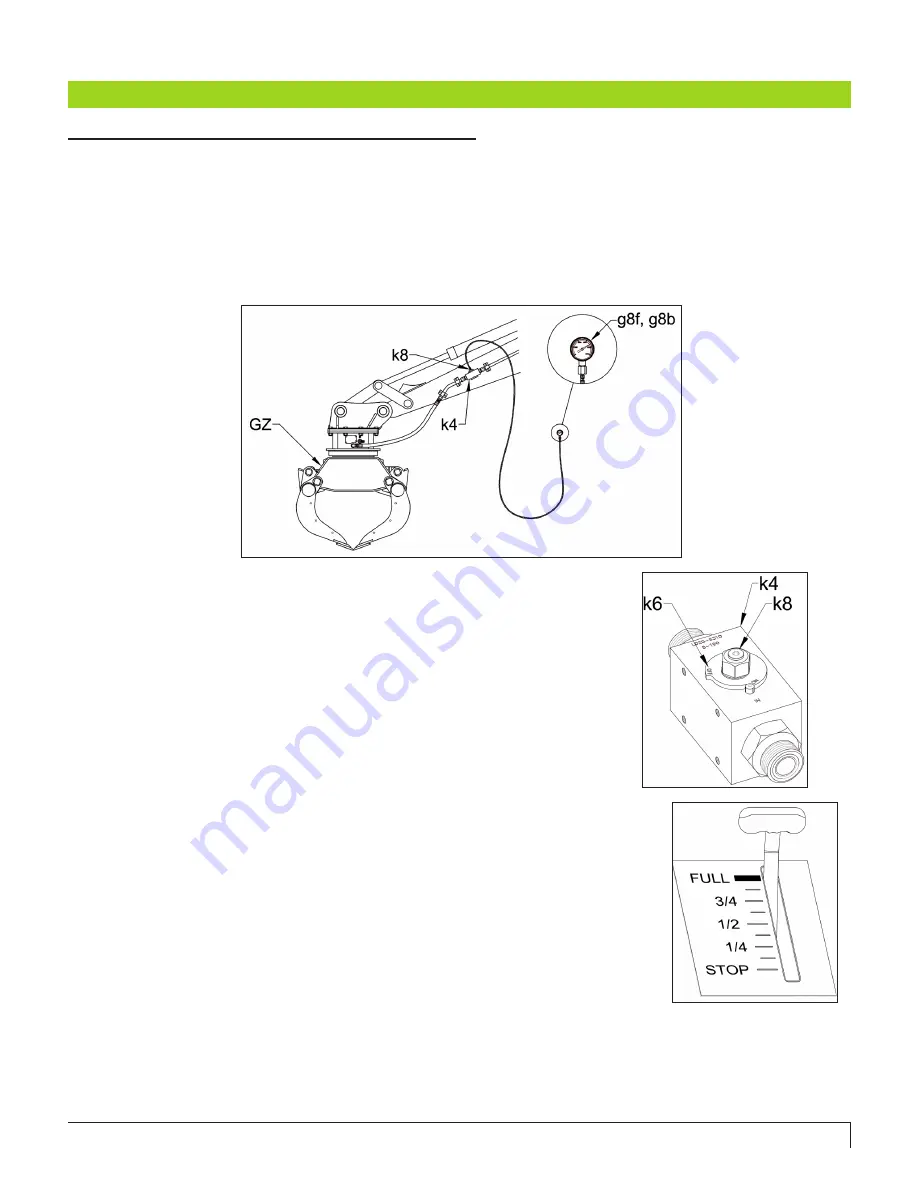
© 2022 Genesis Attachments, LLC
Genesis GHG 16 - GHG 50 Handling Grapple 37
Relief Valve Checking and Setting
(cont'd)
The Carrier's Hydraulic Circuit Relief Valve
Verify the hydraulic circuit meets the GHG's (GZ) requirements; see Hydraulic Flow and Pressure
page 28.
Install a 0 – 5,000 psi (0 – 350 bar) pressure gauge (g8f) in the #4 SAE test port (k8) on the arm
close side and a 0 – 5,000 psi (0 – 350 bar) pressure gauge (g8b) in the #4 SAE test port on the
arm open side located in both shut off valves (k4) at the end of the stick.
Turn the shut-off valves (k4) to the off position.
Start the carrier and set the throttle to the full position. Actuate the
hydraulic circuit to close the GHG arms.
The pressure reading on the gauge should be a minimum of 500 psi
(34 bar) above the GHG's relief valve setting, see Hydraulic Flow and
Pressure page 28.
If the carrier’s relief is not set at a minimum of 500 psi (34 bar) above the
GHG's relief, reset or replace at this time.
TROUBLE-SHOOTING GUIDE