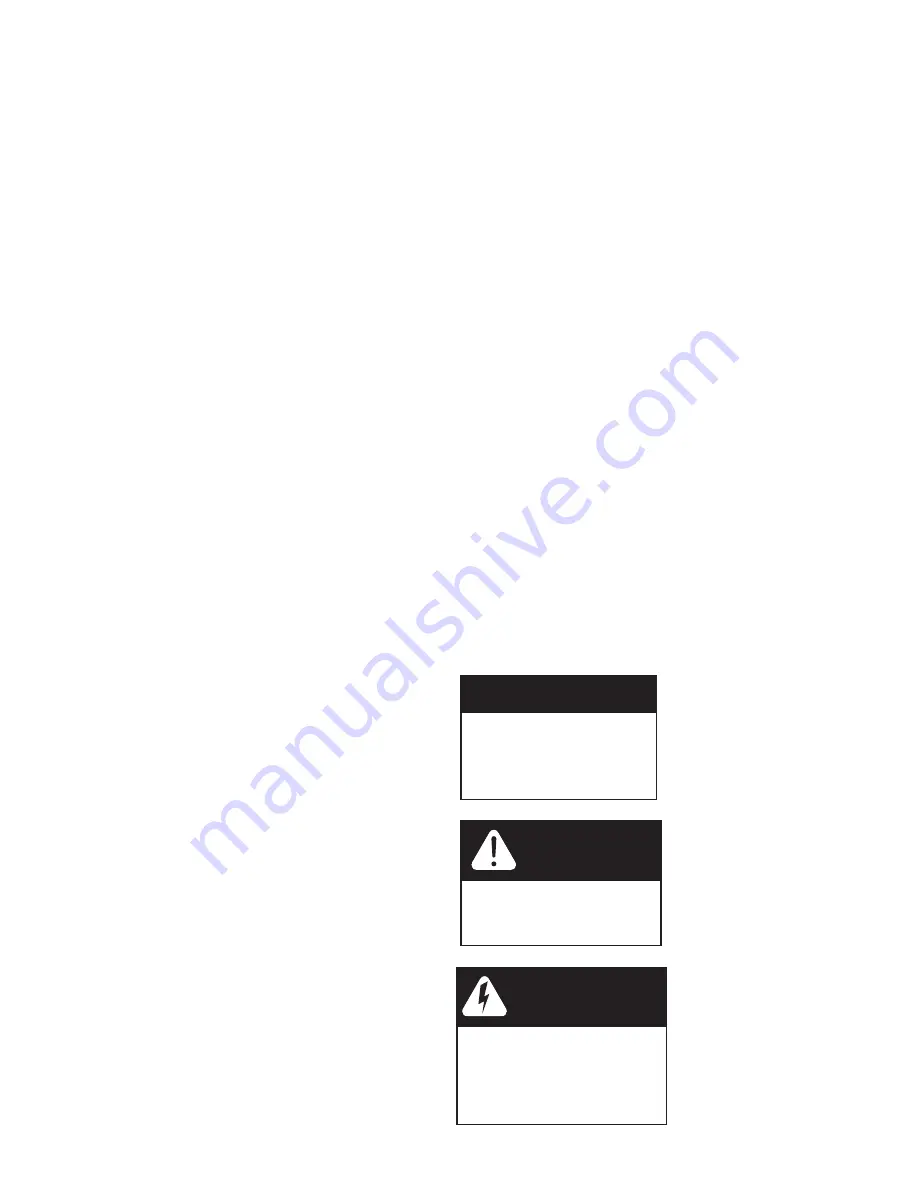
3
READ THIS PAGE FIRST
BEFORE STARTING INSTALLATION
INSTALL NOTES &
SAFETY MESSAGES
Watch for the following
messages in this manual:
NOTE
Do not remove or destroy
the serial number. It must be
referenced on request
for warranty repair or
replacement
CAUTION!
Disassembly while
under pressure can
result in flooding.
WARNING!
ELECTRICAL SHOCK
HAZARD!
UNPLUG THE UNIT
BEFORE REMOVING THE
COVER OR ACCESSING ANY
INTERNAL CONTROL PARTS
NOTE:
used to emphasize
installation, operation or
maintenance information
which is important but does
not present a hazard.
CAUTION:
used when
failure to follow directions
could result in damage to
equipment or property.
WARNING:
used to
indicate a hazard which
could cause injury or death if
ignored.
Read this manual thoroughly to become familiar with the
appliance and its capabilities before installing or operating
the new appliance. Failure to follow instructions in this
manual could result in personal injury or property damage.
This manual will also help you to get the most out of
your new appliance.
Installation must comply with all State, provincial or local
regulations. Check with your local public works department
for plumbing and sanitation codes. In the event the codes
conflict with any content in this manual the local codes
should be followed. Consult your licensed plumber for
installation of this system.
WARNING!:
Do not use water that is microbiologically unsafe
without adequate disinfection before or after this system.
Do not install this appliance where it may be exposed to wet
weather, direct sunlight, or temperatures outside of the
range specified above.
This appliance is designed to operate on pressures of 30
psi to 125 psi. If the water pressure is higher than the
maximum use a pressure reducing valve in the water supply
line to the device.
This appliance is capable of operating at temperatures
between 40°F and 110°F (4°C - 43°C). Do not use this
appliance on hot water supplies.
Avoid pinched o-rings during installation by applying
(provided with install kit) NSF certified lubricant to all seals.
It is not uncommon for sediment, precipitated iron or
hardness to be present in water supplies. Precipitated
minerals or sediments can cause damage to the seals and
piston. This is considered a harsh environment and the seals
and piston would not be covered by warranty stated or
otherwise.
It is recommended to regularly inspect and service the
control valve on an annual basis. Cleaning and or replacement
of piston, seals, and or spacers may be necessary depending
on how harsh the conditions are. An Annual Maintenance kit
is available for this purpose
This publication is based on information available when
approved for printing. Continuing design refinement could
cause changes that may not be included in this publication.
The manufacturer reserves the right to change the
specifications referred to in this literature at any time,
without prior notice.