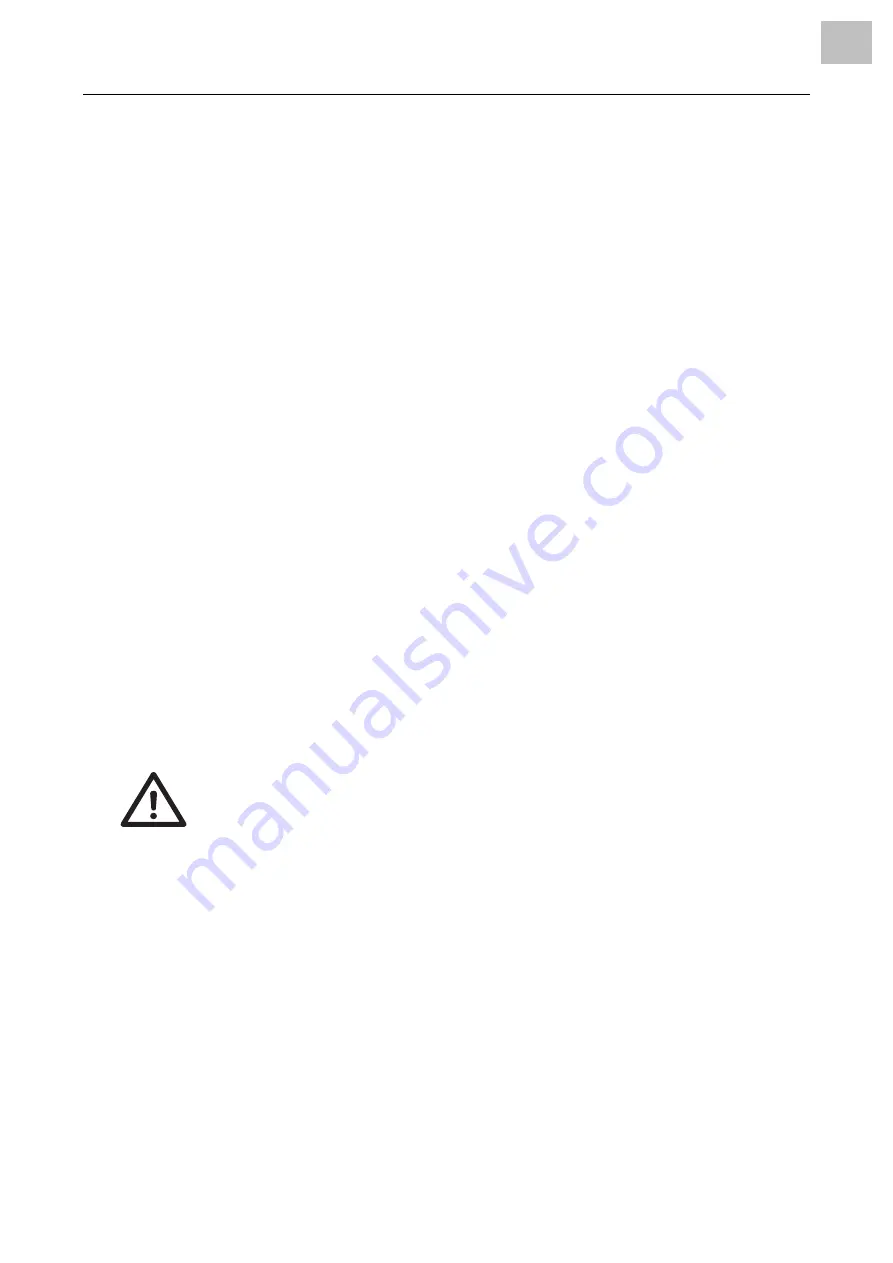
06/08 Rev. 4.05-01
USER MANUAL
Setting up
TTX
x50/67x
–
Wildcats/Wildcats plus
–
S 45/65/95/105
–
TDI/STDI/XXTREME
4
Materials
Document
material
When selecting the material, attention should be paid to 3 factors:
– The abrasive behavior of the surface structure of the material.
– The properties relating to the chemical reaction when the printing ink is
applied.
– The temperature required for ink transfer.
Abrasive behavior
If the material is very abrasive, the print head becomes "worn" sooner than
would normally be the case. This criterion is particularly critical in
thermoprinting. It is not so crucial in heat transfer printing, because in this
case the ribbon can be chosen a little wider than the material and thus the
print head is protected across the whole width of the material (see printer
layout).
Head temperature
More or less the same applies in the case of a high print head temperature.
The material and ribbon need more time to cool down, the print quality is
more critical and the print head wears down more quickly.
For papers weighing more than 240 g, adjustments may need to be made
to the contact pressure and the position of the print head.
Thermoprinting
ribbon
For ribbon, we recommend the following:
– The rear of the ribbon must be given an antistatic and friction-reducing
coating (back-coating).
– Foils must be specified for "near edge type print heads".
– Foils should be suitable for print speeds of up to 12 inch/sec.
Foils without these properties could reduce the performance of the print
and the print quality and also damage the print head!
Note
The print head zero line can be adjusted from 2 to 13 mm away from the
left edge of the label. The setting also affects the horizontal position of the
print image.
The ribbon zero line can also be adjusted towards the label zero line.