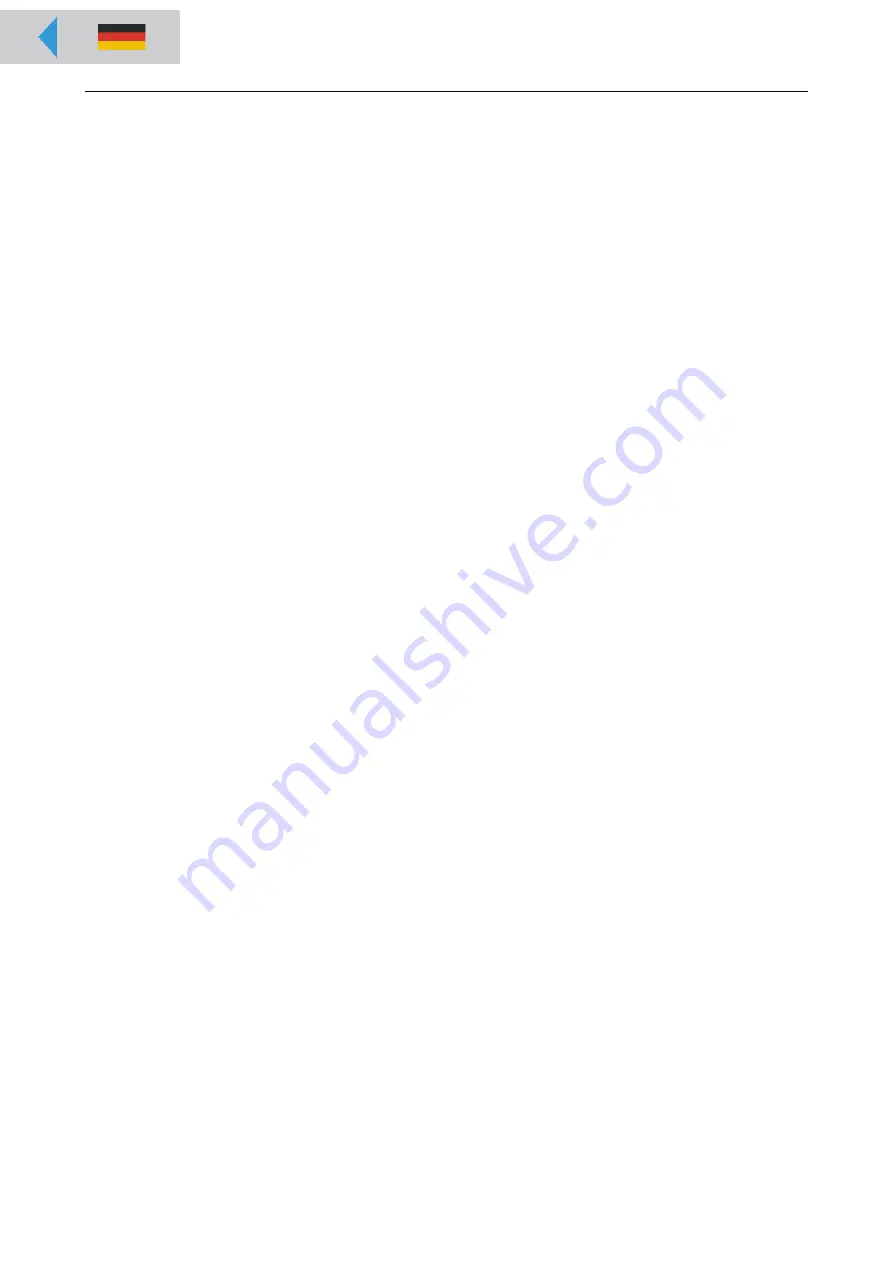
04/11 Rev. 5.07-00
OPERATING MANUAL
ALX 73x
Cleaning
Cleaning instructions ..................................... 2
Safety ........................................................ 2
Cleaning agents ........................................ 2
Cleaning interval ....................................... 2
General cleaning ........................................... 3
Printhead ....................................................... 4
General notes ............................................ 4
Cleaning the printhead .............................. 5
Replacing printheads ................................ 7
Testing the printhead ................................ 8
Rubber rollers ................................................ 9
Feed rollers/print roller .............................. 9
Pressure roller ......................................... 10
Deviator rollers ............................................ 11
Sensors ....................................................... 12
Cleaning the punch sensor ...................... 12
Cleaning the material end sensor ............ 13
Cleaning the ribbon path ............................. 14
Replacing the filter liner ............................... 15