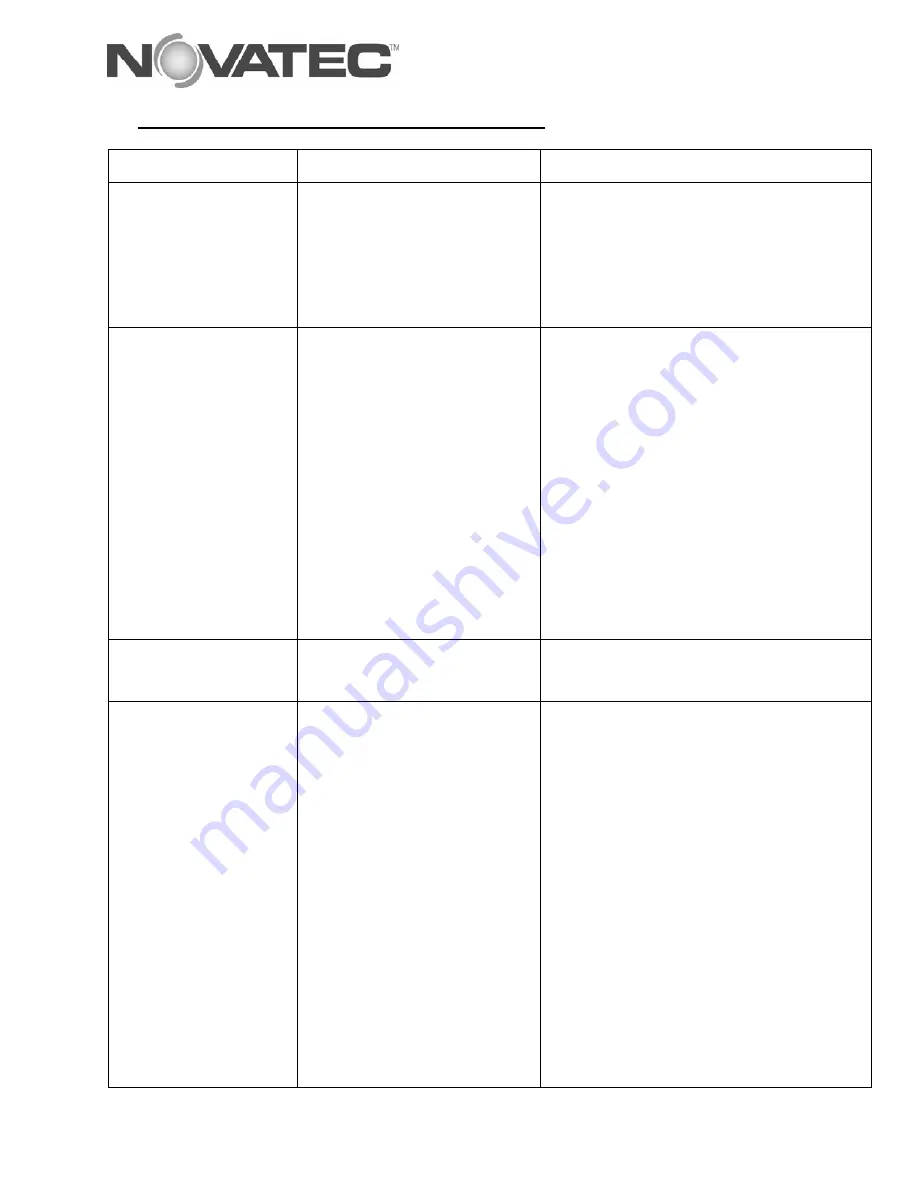
NovaWheel Instruction Manual
29
Document#: IM NW400-2000_10-07-08
NW Series NovaWheel Dryer
INSTRUCTION MANUAL
14 TROUBLE SHOOTING and ERROR MESSAGES
TROUBLE PROBABLE
REASON CORRECTIVE
ACTION
1. Unit not running
Control main circuit breaker
tripped.
Main power off.
Control power interrupted.
Reset the breaker.
Check line and main.
Check per item as per electrical wiring
diagram.
2. Material in hopper
melts.
Process temperature
controller set too high for
material being
dried.
Temperature probe not
installed in process air
stream.
Process blower rotating in
wrong direction.
Temperature sensor
connection loose or
reversed.
Check set temperature for proper
drying process temperature.
Ensure temperature probe is installed
in the dryer outlet, or in the hopper
inlet.
Change blower rotation.
Correct the connection.
3. Reactivation
(regeneration)
temperature too high.
React temperature set too
High.
Check set temperature on NovaWheel
controller. it should be 400°F (205°C)
4. React
(regeneration) heat
too low (Rotor not
fully reactivating.)
React thermostat setting too
low
React temperature
controller set too Low
React heaters faulty.
Adjust thermostat for proper
reactivation heat at around 400° F
(205°C)
Check set temperature on NovaWheel
microprocessor controller. it should be
400° F. (205°C)
Replace heaters.