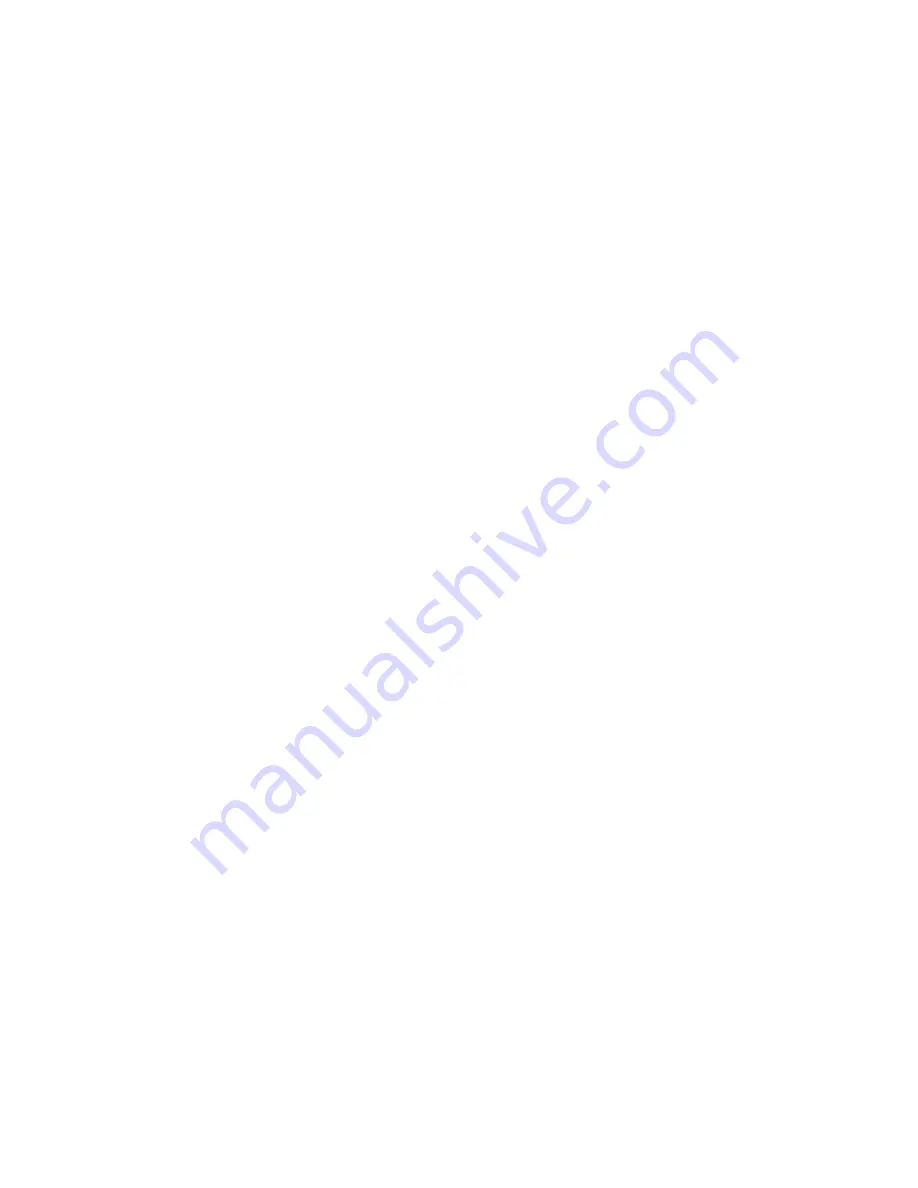
NO-STRIKE FAULT
PAGE
|
78
No-Strike fault
A No-Strike fault occurs when the laser discharge does not strike (gas does not breakdown). During No-
Strike faults lasing is limited to a maximum 6.25% duty cycle (at a PWM Command frequency of 5 kHz),
or 5% at the user’s specified frequency during PWM signal application.
Blinking Shutter LED fault
Possible Causes:
•
A No-Strike fault has occurred, possibly due to cold environmental conditions (common when
overnight temperatures are low) that may prevent the gas from breaking down into a plasma
state.
When this occurs, it may take 30 to 60 seconds for gas breakdown so the laser can begin normal daily
operation. There are three methods to force breakdown and clear the no-strike fault: (1) Apply tickle
pulses or a PWM Command signal (< 6.25% duty cycle) for 30 to 60 seconds. When the gas breaks
down into a plasma state, the laser will recover and begin lasing at the commanded power level without
cycling DC power. (2) Apply a single 20
μ
s PWM pulse (at 5 kHz) while monitoring the Fault Detected
output. If the output closes, wait a minimum of 52 ms for the output to open and then apply another 20
μ
s PWM pulse. Repeat this sequence until no fault is detected—which typically occurs in less than one
second. Be aware that applying 20
μ
s breakdown pulses in rapid succession may cause laser output. (3)
Apply a PWM Command signal (at < 5% duty cycle) until the fault clears—typically less than 30 seconds.
With either method, when breakdown does occur, lasing will begin immediately at the commanded PWM
parameters without cycling DC power. If the No-Strike condition persists, contact NOVANTA® or a
NOVANTA Authorized Distributor.
Frequency Limit Fault
Possible Causes:
•
The 100 kHz PWM frequency limit has been exceeded.
Lasing is disabled when the input frequency limit is exceeded. When the input drops below 100 kHz, the
laser will begin lasing immediately at the commanded PWM parameters without cycling DC Power.
Duty Cycle/Pulse Width Limit Fault
Possible Causes:
•
The applied PWM Command signal is outside the laser’s operating parameters.
Lasing is disabled when a constant 5V signal (100% duty cycle) is applied. When the PWM duty cycle
drops below 100%, the laser will begin lasing immediately at its 37.5% PWM duty cycle limit. If the
commanded duty cycle is above 37.5% or the PWM pulse length exceeds 600
μ
s, adjust the pulse length
until the PWM input is brought within limits. The laser will then lase at the commanded PWM parameters.
When a duty cycle or pulse width limit fault is detected, the SHT LED flashes 3 blinks and the Fault
Detected output Closes to indicate (1) a constant 5V PWM signal is applied, forcing the PWM duty cycle
to 100%—full continuous wave operation; (2) the applied duty cycle is above the 37.5% limitation; or (3)
the applied pulse length exceeds 600
μ
s in duration. When condition 1 occurs, the laser begins lasing
immediately at 37.5% once the PWM duty cycle drops below 100%. For condition 2, the laser begins
lasing immediately at the commanded PWM parameters, the duty cycle is automatically limited to 37.5%.
For condition 3, the laser begins lasing immediately at the commanded PWM parameters, the pulse
duration is automatically limited to 600
μ
s.
Summary of Contents for SYNRAD Pulstar p100
Page 1: ...ENGINEERED BY SYNRAD p100 150 Lasers User Manual...
Page 17: ...NOMENCLATURE CONTINUED PAGE 12 Nomenclature Continued Figure 1 2 Anatomy of a model number...
Page 23: ...ADDITIONAL LASER SAFETY INFORMATION PAGE 18 p100 label locations...
Page 24: ...ADDITIONAL LASER SAFETY INFORMATION PAGE 19 p150 label locations...
Page 30: ...ELECTROMAGNETIC INTERFERENCE STANDARDS PAGE 25 Figure 2 1 p100 Declaration Document...
Page 31: ...ELECTROMAGNETIC INTERFERENCE STANDARDS PAGE 26 Figure 2 2 p150 Declaration Document...
Page 39: ...FOCUSING OPTICS PAGE 34 Table 3 1a Dew point temperatures in Fahrenheit Dew Point Table F...
Page 46: ...OPERATION MODES PAGE 41 Figure 3 6 p150 pulse profile 37 5 duty cycle at 10 kHz...
Page 49: ...USER I O CONNECTION SUMMARY PAGE 44 Figure 3 9 User I O connector pinouts...
Page 68: ...REMOTE INTERLOCK FUNCTIONS PAGE 63 Figure 3 21 p100 150 outline mounting drawings pg 1 of 2...
Page 70: ...REMOTE INTERLOCK FUNCTIONS PAGE 65 Figure 3 23 p100 150 packaging instructions...
Page 71: ...REMOTE INTERLOCK FUNCTIONS PAGE 66 Figure 3 24 p150 outline and mounting...
Page 79: ...STATUS LEDS PAGE 74 Status LEDs Table 4 2 p100 p150 Input output LED Status Signals...