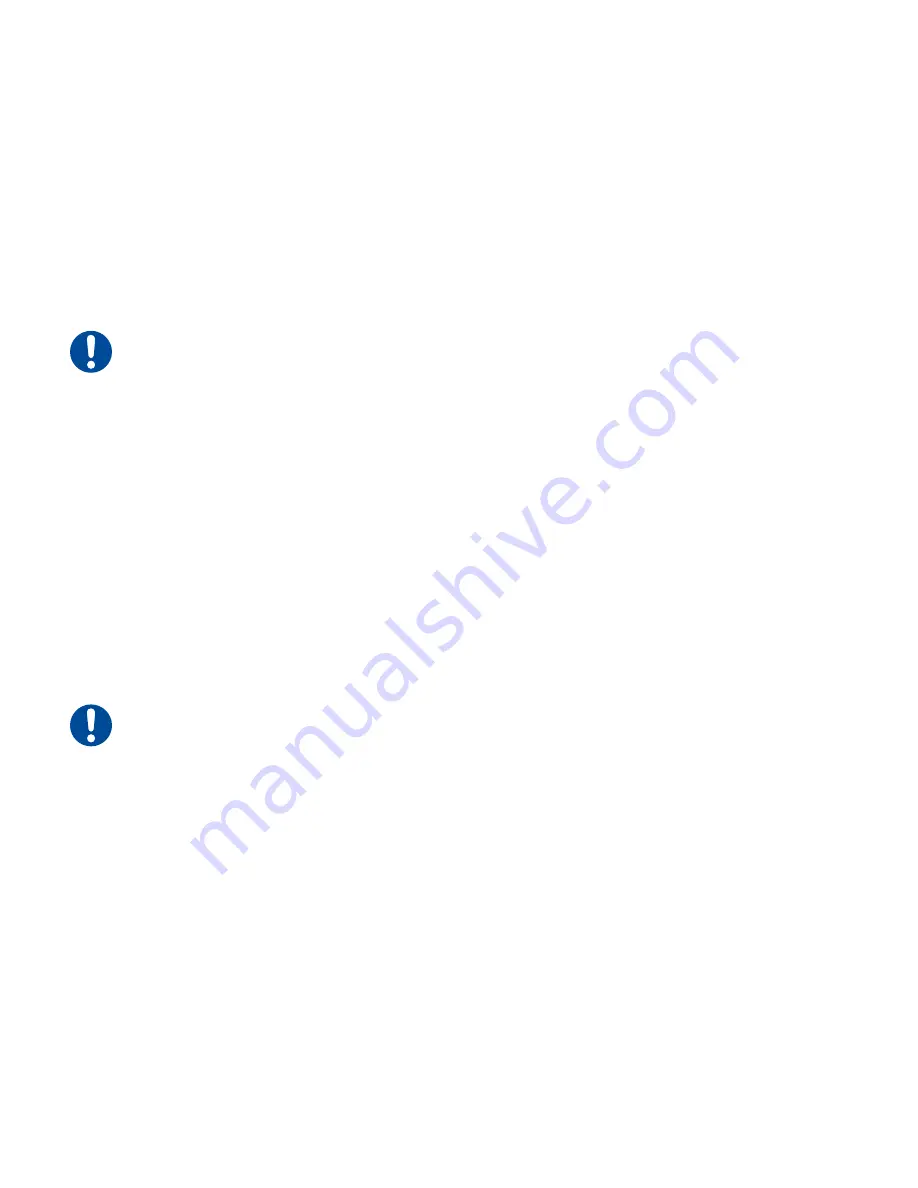
INTEGRATING F201 SAFETY FEATURES
PAGE
|
75
Integrating f201 safety features
The Integrating f201 safety features section includes subsections:
Remote Keyswitch functions
The f201 DB-9 Connector allows system integrators or end-users to integrate f201 laser safety features
into their control system. In particular, the f201 Remote Keyswitch function serves to disable DC power to
the laser’s RF driver. Without power, the RF driver cannot supply PWM or tickle signals to the resonator,
causing the CO2 gas to remain in a zero-energy state.
Important Note:
You can use these same circuits to monitor the laser’s Remote Lase LED Output
(DB-9, Pin 8); however, the Remote Lase LED Output is not a steady state (on/off) output. It is a
Pulse Width Modulated (PWM) signal based on the PWM input signal to the laser.
OEM lasers
On OEM lasers, 5-seconds after power-up DC power is applied to the RF driver. To reset a fault condition,
remove DC power for 30 seconds and then reapply power to the laser or toggle (open, then close) the
Remote Keyswitch signal via pins 6 and 7 on the DB-9 Connector. To use this “remote reset” functionality,
open and then close a “dry-circuit” (zero voltage) switch or relay contact between Pin 6, Remote
Keyswitch Input, and Pin 7, Remote Keyswitch Output. Reconnecting Pin 6 to Pin 7 applies power to the
RF driver and begins a five-second delay after which lasing is enabled.
Your control system can monitor the laser’s power-on status through the DB-9 Connector by connecting
your system’s input between Pin 9, Remote Ready LED Output, and Pin 2, Signal Ground. The Remote
Ready LED Output goes active when the laser is enabled, indicating that lasing is possible after the five-
second delay. The output is inactive when lasing is disabled. Refer to the DB-9 pin assignment tables for
specific details.
Important Note: f201 lasers may be hard mounted to equipment by removing several of the bot-
tom panel screws and replacing these with longer screws to secure the laser to optical
assemblies. This mounting method is only recommended if the screws do not support the weight of the
laser. For a sturdier attachment, the laser may be clamped to optical assemblies by applying clamping
forces between top and bottom cover screws. Do not apply clamping forces on the longitudinal cen-
terline.
Summary of Contents for f201
Page 1: ...ENGINEERED BY SYNRAD f201 Laser User Manual...
Page 15: ...INVENTORY PAGE 15 Inventory F201 Lasers Figure 2 3 f201 shipping box contents...
Page 36: ...F201 LABEL LOCATIONS PAGE 36 f201 label locations Figure 3 1 100 hazard label locations...
Page 44: ...COMPLIANCE PAGE 44 Figure 3 4 f201 Declaration Document...
Page 45: ...COMPLIANCE PAGE 45 Figure 3 5 continued F201 Declaration Document...
Page 76: ...INTEGRATING F201 SAFETY FEATURES PAGE 76 Figure 4 15 F201 packaging diagram...
Page 78: ...F201 GENERAL SPECIFICATIONS PAGE 78 Table 4 9 f201 general specifications continued...
Page 104: ...INDEX PAGE 1 This page is intentionally left blank...