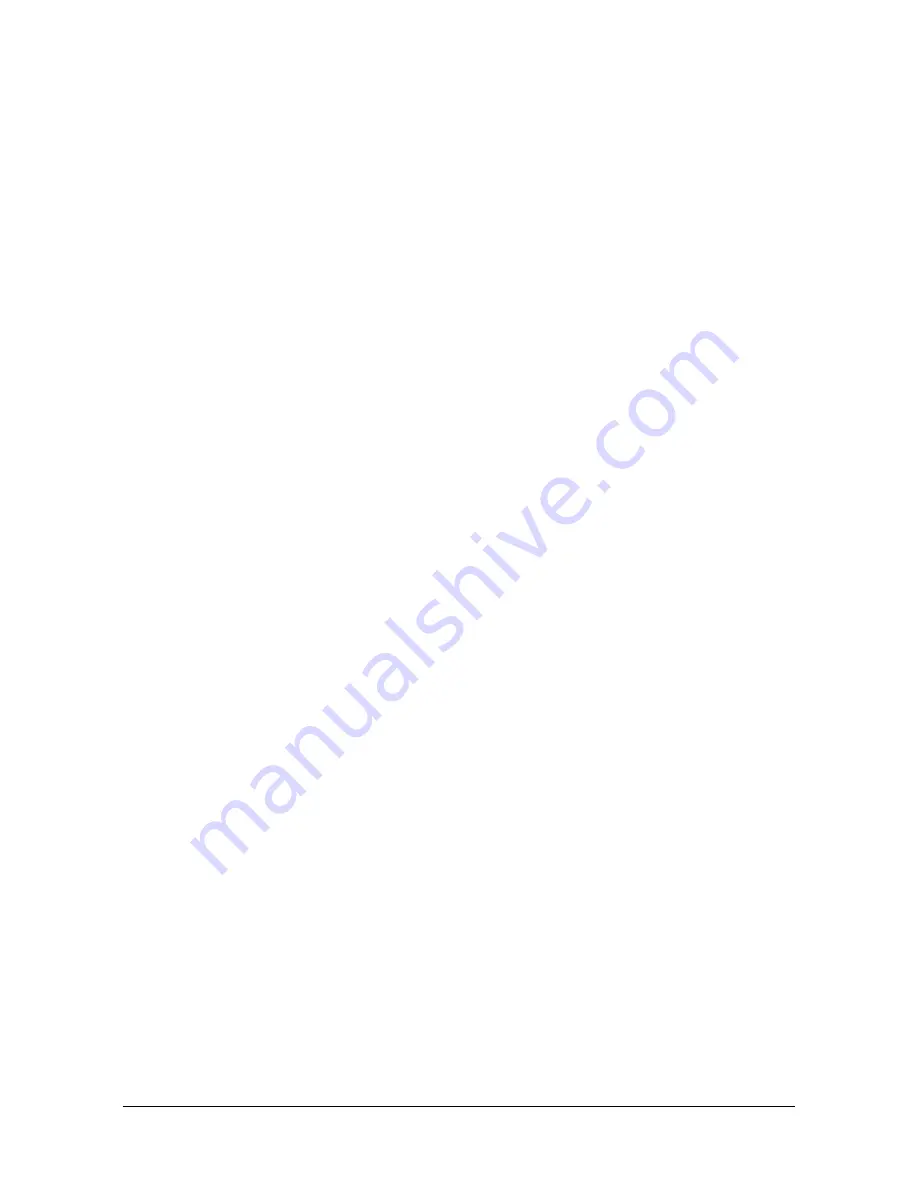
Manual, F/T Sensor, Axia90
Document #9620-05-B-Axia90-03
Pinnacle Park • 1031 Goodworth Drive • Apex, NC 27539 • Tel:+1 919.772.0115 • Fax:+1 919.772.8259 •
B-20
6. The calculated tooling masses for all (6) points should deviate from each other by less than twice the
worst accuracy rating of the sensor.
•
For example: the Axia90-M50 sensor’s rated accuracy is 2% the range on all axes. For a 1000 N F
xy
range and a 2000 N F
z
range, the allowable errors of any single data point would be
±
20 N F
xy
and
±
40 N F
z
respectively. Since F
z
has the larger tolerance, then one data point could be + 40 N and another
data point could be - 40 N, for a total range (max-min) of 80 N error.
•
In addition, the tooling mass should be within 80 N
of the results of this test when it was performed
with a new sensor.
7. If this test fails, then the sensor should be returned to ATI for diagnosis or recalibration.
3.7 Detecting Sensitivity Changes
Sensitivity checking of the sensor can also be used to measure the Axia sensor’s health. Apply known loads
to the sensor and verifying the system output matches the known loads. For example, a sensor mounted to a
robot arm may have an end-effector attached to it. Use the following process to set a sensitivity value:
1.
If the end-effector has moving parts, they must be moved in a known position.
a.
Place the robot arm in an orientation that allows the gravity load from the end-effector to exert load
on many sensor output axes.
2. Record the output readings.
3.
Position the robot arm to apply another load, this time causing the outputs to move far from the
earlier readings.
4.
Record the second set of output readings.
5. Find the differences from the first and second set of readings.
6.
Use the differences as a sensitivity value.
Even if the sensitivity values vary from sample set to sample set, these values can be used to detect gross
errors. Either the resolved outputs or the raw sensor voltages may be used (the same must be used for all
steps of this process).