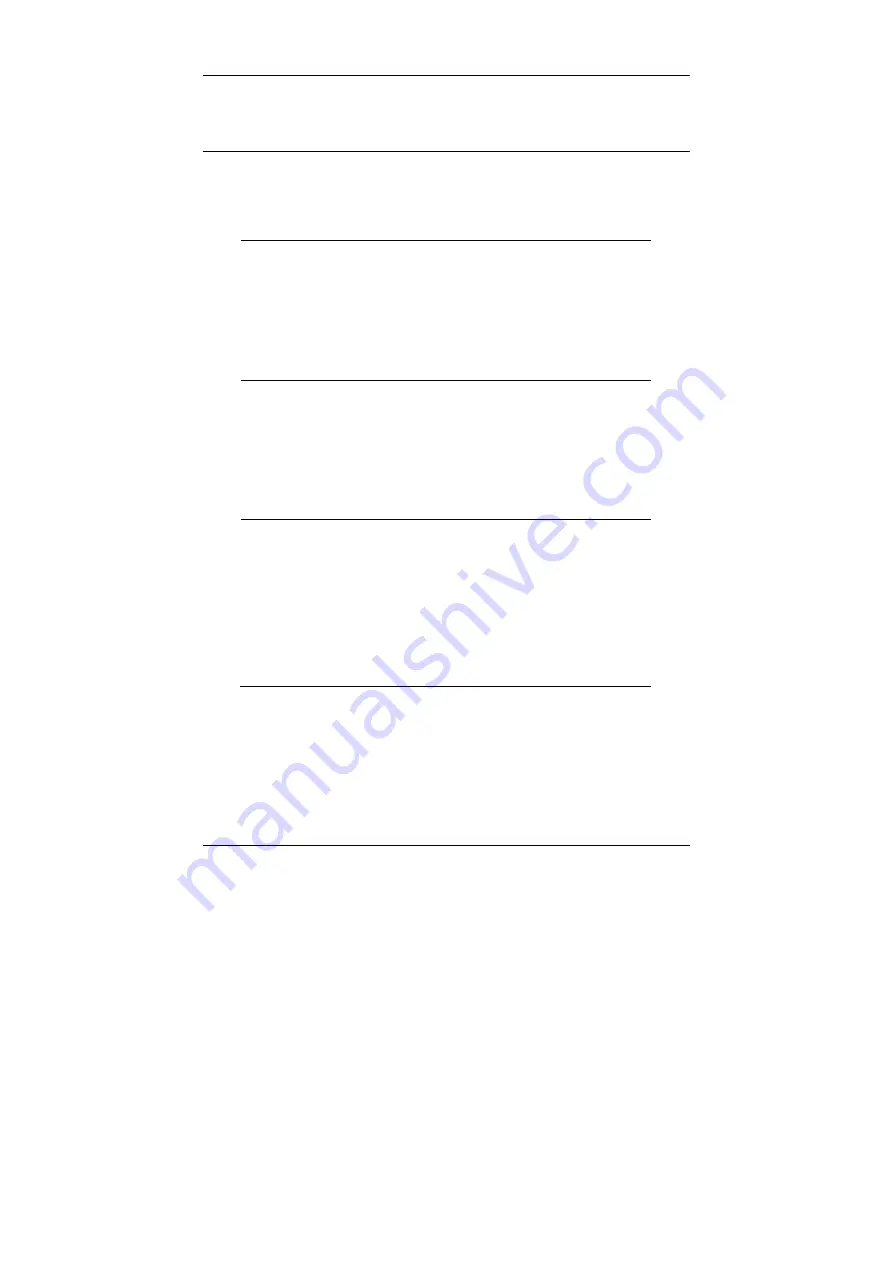
Operating Instructions and Parts Manual
Northern Industrial Welding
14
Amp Arc 7000
Amp Arc 7000
23
Muffler front housing plate
2.16.03.687
1
24
L type supporter
2.16.03.683
2
25 Handle
1.2.01.01.3243
2
26
Muffler right housing plate
2.16.03.686
1
27
Hexagon flange screw
2.06.01.056
8
28 Rack
form
1.1.01.04.0354
1
29 Wheel
2.05.07.2116 2
30 Pin
2.06.17.008 2
31 Hexagon
screw
2.06.01.064 4
32 Flap
washer
2.06.17.010 4
33 Axle
1.2.02.04.0118
1
34 Flap
washer
2.06.17.005 4
35 Spring
washer
2.06.18.005 4
36 Hexagon
nut
2.06.14.005 4
37 Damping
feet
2.05.05.126 4
38 Dynamo
2.07.40.617 1
39 Cross-flow
pipe
2.05.05.907 1
40
Electric cabinet component
1.2.01.01.3241
1
41 Pallet
component
1.1.01.04.0353
1