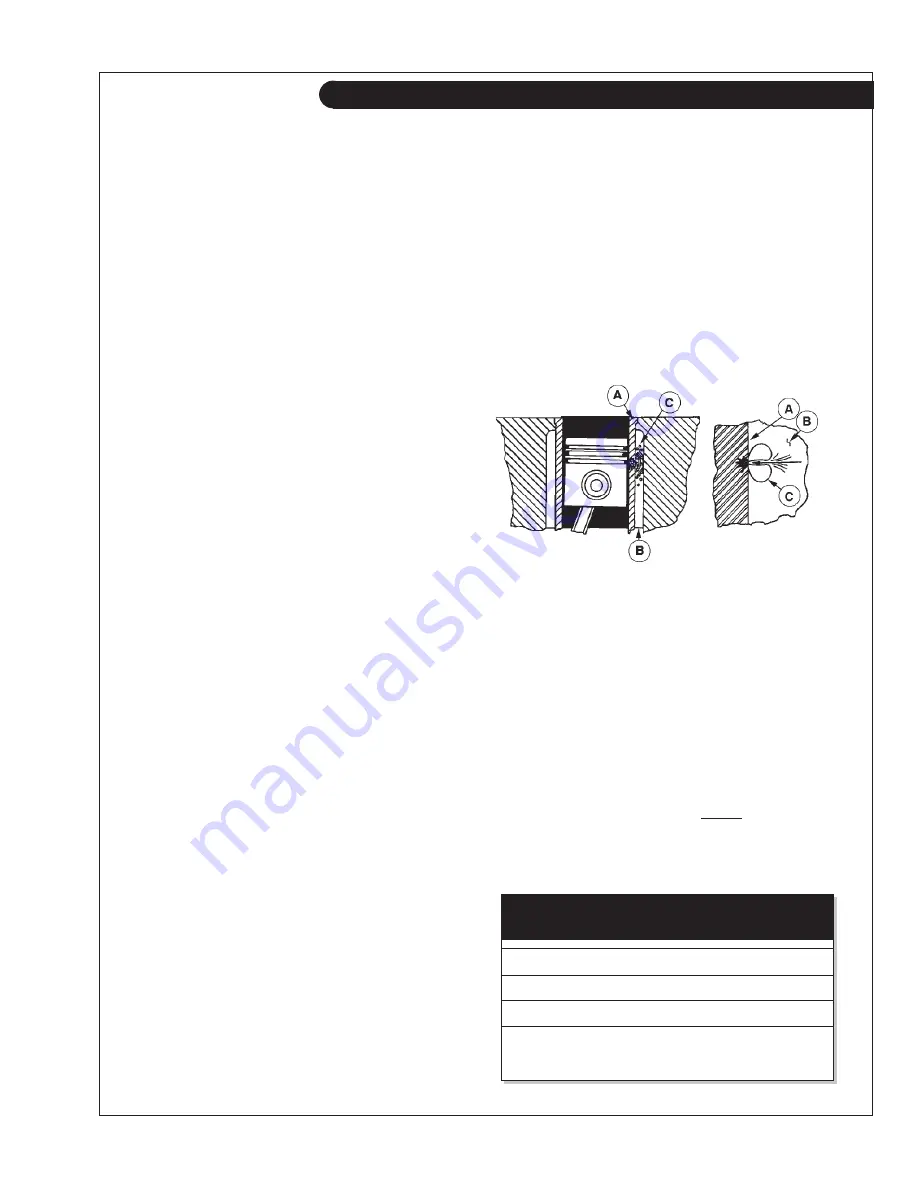
OLP 05/00
SP12. TURBOCHARGER
1. Check for air leaks every 200 hours. Air leakage
will lower engine output and may cause black
exhaust smoke and soot.
2. Listen along air line while engine is running.
A whistling or hissing sound indicates leakage.
3. Leakage on the pressure side, between turbo and
engine, can be found by applying soapy water to the
air line.
4. Tighten the hose clamps, replace hose or gaskets as
required.
5. Check to see that the lubrication and cooling lines
are tight and without leaks.
SP13. TURBO BOOST
1. This check measures the amount of air the turbo
is pushing into the engine. It should be done by an
authorized dealer every 600 hours.
2. On the inlet manifold there is a 1/8" NPT threaded
port. Remove the plug and install the boost gauge
hose. Refer to your engine specifications for correct
pressure.
COOLING REQUIREMENTS
1. To meet cooling system protection requirements, the
coolant solution must consist of:
a. Quality water
b. Ethylene glycol concentrate (EGC ) commonly
known as antifreeze.
c. Supplemental coolant additives (SCA's).
2. A coolant solution of ethylene glycol concentrate
(EGC-antifreeze), quality water and supplemental
coolant additives (SCA's)
MUST
be used
YEAR
ROUND
to protect against freezing, boil-over, liner
erosion or pitting and to provide a stable, noncorro-
sive environment for cooling system components.
3. Ethylene glycol coolant concentrate (antifreeze)
normally DOES NOT contain the SCA chemical
inhibitors needed to control liner pitting or
erosion, rust, scale, and acidity.
LINER EROSION (PITTING)
1. Cylinder liner walls
(Figure 22-A)
which are in contact
with engine coolant
(Figure 22-B)
can be eroded or
pitted unless the proper concentration and type of
SCA's are present in the coolant. Water pump
impellers are also susceptible to pitting.
2. Vapor bubbles
(Figure 22-C)
are formed when the
piston's impact causes the liner walls to vibrate,
sending pressure waves into the coolant.
3. These tiny vapor bubbles collect on the surface
of metal parts. As the bubbles collapse (pop) a
microscopic piece of metal is eroded from the
metal part. Over a period of time, this pitting may
progress completely through the cylinder liner of a
wet-sleeve, heavy-duty diesel engine. This allows
coolant to enter the combustion chamber. Engine
failure or other serious damage will result.
A
- Cylinder Liner Walls
B
- Engine Coolant
C
- Vapor Bubbles
Figure 22.
4. Unprotected engines with low quality water as cool-
ant can have liner failure in as few as 500 hours.
WATER QUALITY
1. Distilled, deionized, soft water is preferred for use in
cooling systems. Bottled distilled water from a food
store or water supplier is recommended. Tap water
often has a high mineral content. Tap water should
NEVER
be put in a cooling system unless first tested
by a water quality laboratory. Do not use water
made by the reverse osmosis method unless it has
been PH neutralized.
2. Here are acceptable water quality specifications:
Parts Grains
Contaminates
per Million per Gallon
Maximum Chlorides
40
2.5
Maximum Sulfates
100
5.9
Maximum Dissolved Solids
340
20.0
Maximum Total Hardness
170
10.0
PH Level 5.5 to 9.0
17
Servicing
Summary of Contents for OLP LP445
Page 29: ...OLP 05 00 27 Wiring Diagrams DC Engine Wiring Diagram 12 Volt Lugger LP668 Drawing C 4363B...
Page 30: ...OLP 05 00 28 DC Engine Wiring Diagram 12 Volt Lugger LP445 Drawing C 4364A Wiring Diagrams...
Page 31: ...OLP 05 00 Wiring Diagrams 29 DC Engine Wiring Diagram 24 Volt Lugger LP668 Drawing C 4370A...
Page 32: ...OLP 05 00 Wiring Diagrams 30 DC Engine Wiring Diagram 24 Volt Lugger LP445 Drawing C 4371...
Page 34: ...OLP 05 00 32 Notes...
Page 35: ......