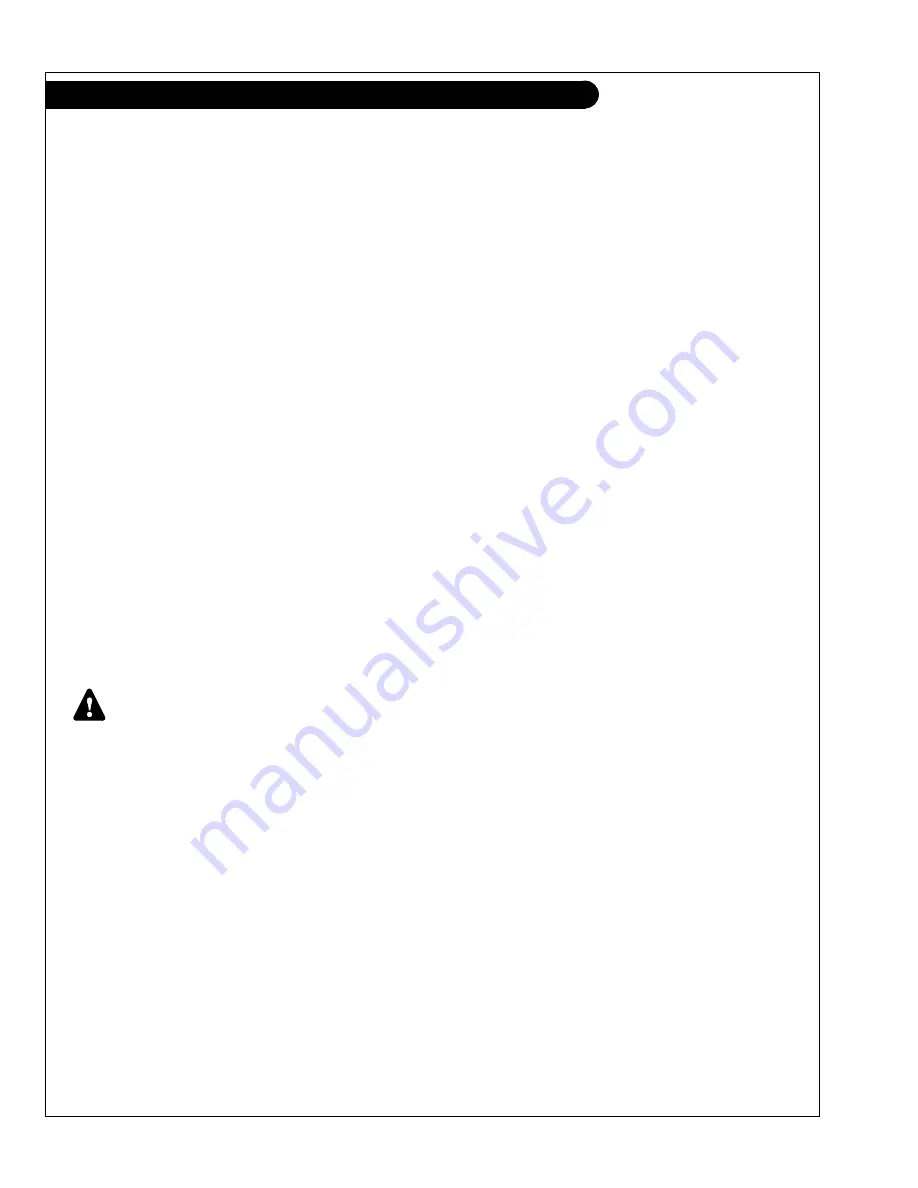
O844K 10/09
8
bREAK-IN PERIOd
1. The first 100 hours on a new or reconditioned
engine are critical to its life and performance.
2. Frequently check the engine temperature and oil
pressure gauges (sets with Series 3 or 4 panels).
3. Oil consumption is greater during break-in as
piston rings take time to seat.
4. Break-In Oil Changes: Change engine oil and
filter at 50 hours. Change oil and filter again at
100 hours (consult Lubricants section for oil recom-
mendation).
Operating Instructions:
Maintain at least a 75% load on your generator
set for the first 100 hours. If this is not possible,
maintain no less than a 50% load to ensure proper
seating of the piston rings. Vary the load to help
seat the rings.
bEfORE STARTINg
1. Check the water level by removing the pressure
cap from the expansion tank or radiator. In order to
give the cooling water an opportunity to expand, the
level should be about 1 in. (2.5 cm) below the filler
cap sealing surface when the engine is cold.
CAUTIoN: Use protective clothing and open the
filler cap carefully when the engine is warm to
prevent burns.
2. Check the oil level in the crankcase with the dip-
stick. The oil level must be in the waffled area on the
stick. Never allow the level to go below this area.
Always add the same viscosity of oil as is already in
the crankcase.
3. Check the fuel tank level and open any fuel valves.
4. Marine Sets: close the sea-cock; check, clean, and
reassemble the sea strainer and re-open the sea-cock.
5. Marine Sets: place the battery switch in the ON posi-
tion.
6.
NoTe: The battery switch must always be kept
oN while the engine is running. If the switch is
turned oFF while the engine is running, the bat-
tery charging regulator could be ruined.
STARTINg
1. Hold the Shutdown Bypass-Preheat switch in the ON
position for 10 to 20 seconds before starting a cold
engine. Holding the switch too long can burn out the
glow plugs. This step is not necessary if the engine is
already warm.
2. While holding the Shutdown Bypass-Preheat switch
in the ON position, push the Engine Control switch
to the START position.
3. As soon as the engine starts, release both switches. Do
not crank the starter for more than 20 seconds consecu-
tively. If the engine fails to start with the first attempt,
be sure that it has stopped completely before re-engag-
ing.
6.
NoTe: excessive cranking of the starter on Marine
sets equipped with a water lift muffler can cause
engine damage. If the engine does not start after three
20-second cranks, remove the impeller from the raw
water pump. This will prevent the muffler from filling
with water and backfilling the exhaust line and engine.
once the engine starts, shut it off immediately and
re-install the impeller. Re-start the engine and check
the exhaust overboard outlet for gushes of water.
OPERATINg
1. Units with Series 3 and Series 4 Control Panels:
check gauges often. Oil pressure must be above 15
PSI. The D.C. voltmeter should read between 11
and 15 volts at 80°F (25°C) ambient temperature.
The water temperature gauge on Marine sets must
be below 200°F (94°C). Check the A.C. voltage
and frequency meters (Series 4 panel). If the gauges
deviate from normal levels, shut down the generator
set and investigate.
2. Let the unit run unloaded for a three to five minute
warm-up period.
3. Apply electrical load.
STOPPINg
1. Remove electrical load from the generator set.
2. Run the engine for a 3 to 5 minute cool down period.
3. Hold the Engine Control switch to the STOP posi-
tion until the engine comes to a complete stop.
4. Marine Sets: shut off the seacock, fuel valve, and
battery switch.
Operating Procedures