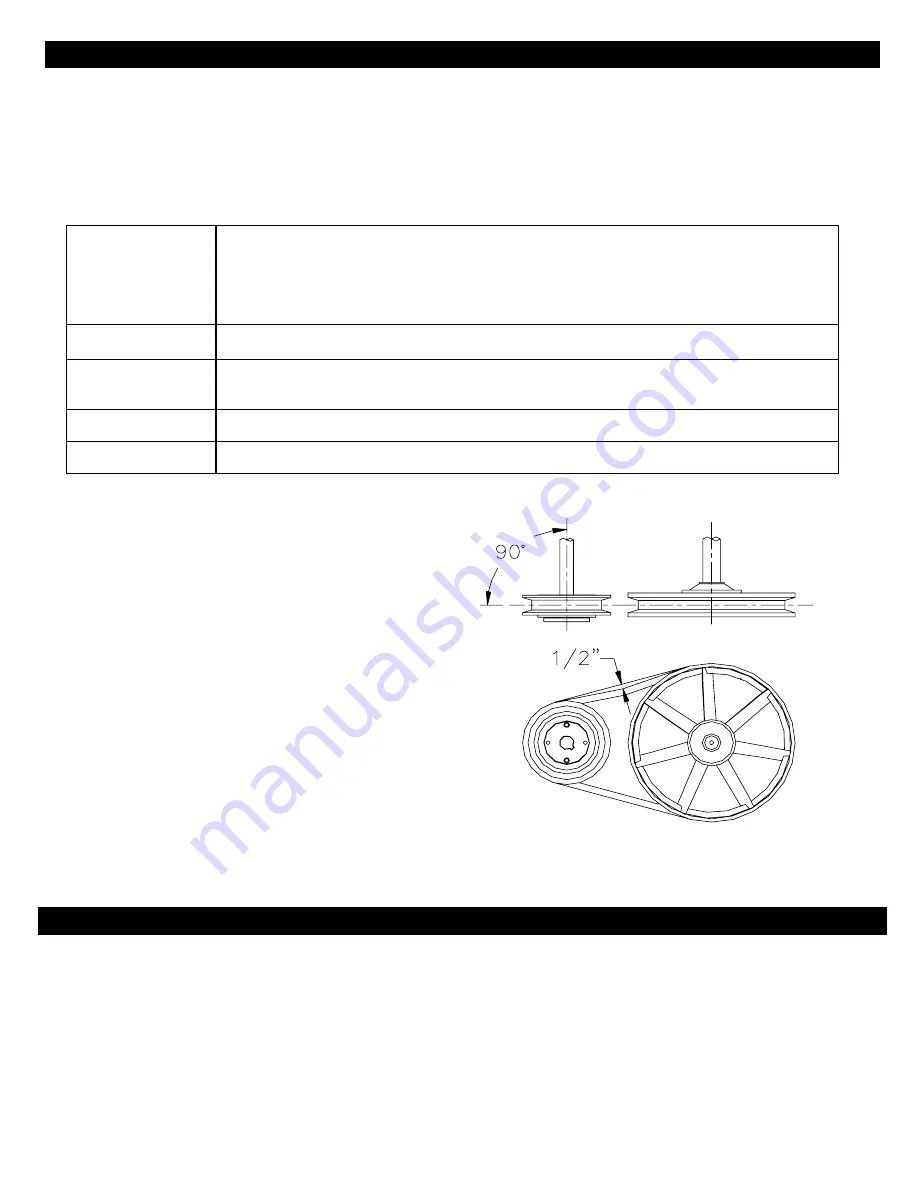
6
Maintenance
WARNING!
Disconnect spark plug wire from spark plug and release air pressure from system before performing
maintenance.
NOTE:
All compressed air systems contain maintenance parts (e.g. lubricating oil, filters, separators), which are
periodically replaced. These used parts may be, or contain, substances that are regulated and must be disposed
of in accordance with local, state, and federal laws and regulations.
NOTE:
Take note of the position and locations of parts during disassembly to make reassembly easier. The
assembly sequences and parts illustrated may differ for your particular unit.
Daily or before each
operation
•
Check lubrication levels. Fill as needed.
•
Drain receiver tank condensate.
•
Check for unusual noise or vibration.
•
Ensure belt guards and covers are securely in place.
•
Ensure area around compressor is free from rags, tools, debris, and flammable or explosive
materials.
Weekly
•
Check safety/relief valves by pulling rings. Replace safety/relief valves that do not operate freely.
•
Inspect air filter element. Clean if necessary.
Monthly
•
Inspect for air leaks. Squirt soapy water around joints during compressor operation and watch for
bubbles. Tighten fittings if necessary.
•
Clean exterior.
3 months or 500
hours
•
Change petroleum lubricant in pump while crankcase is warm.
12 months or 1000
hours
•
Replace air filter element.
DRIVE BELT
Belts will stretch in normal use. Properly adjusted, a
5 pound force applied to the belt between the motor
pulley and the pump will deflect the belt about 1/2”.
TO ADJUST DRIVE BELT:
1. Remove the belt guard cover.
2. Loosen the four fasteners holding the
engine/motor to the compressor.
3. Shift the engine/motor in the proper direction.
The belt must be properly aligned when
adjustment is made.
4. To align belt, lay a straight edge against the face
of the flywheel touching the rim at two places.
5. Adjust flywheel or motor pulley so that the belt
runs parallel to the straight edge.
6. If necessary, use a gear puller to move the pulley
on the motor shaft.
7. Check for proper belt tension (see diagram).
8. Tighten the four fasteners holding the
engine/motor to the compressor.
9. Attach belt guard cover.
Service Parts
Air filter (Item #459211): Part #AB2281000
Air filter (Item #459221): Part #35409
Non-detergent Oil: Part #4043
00882