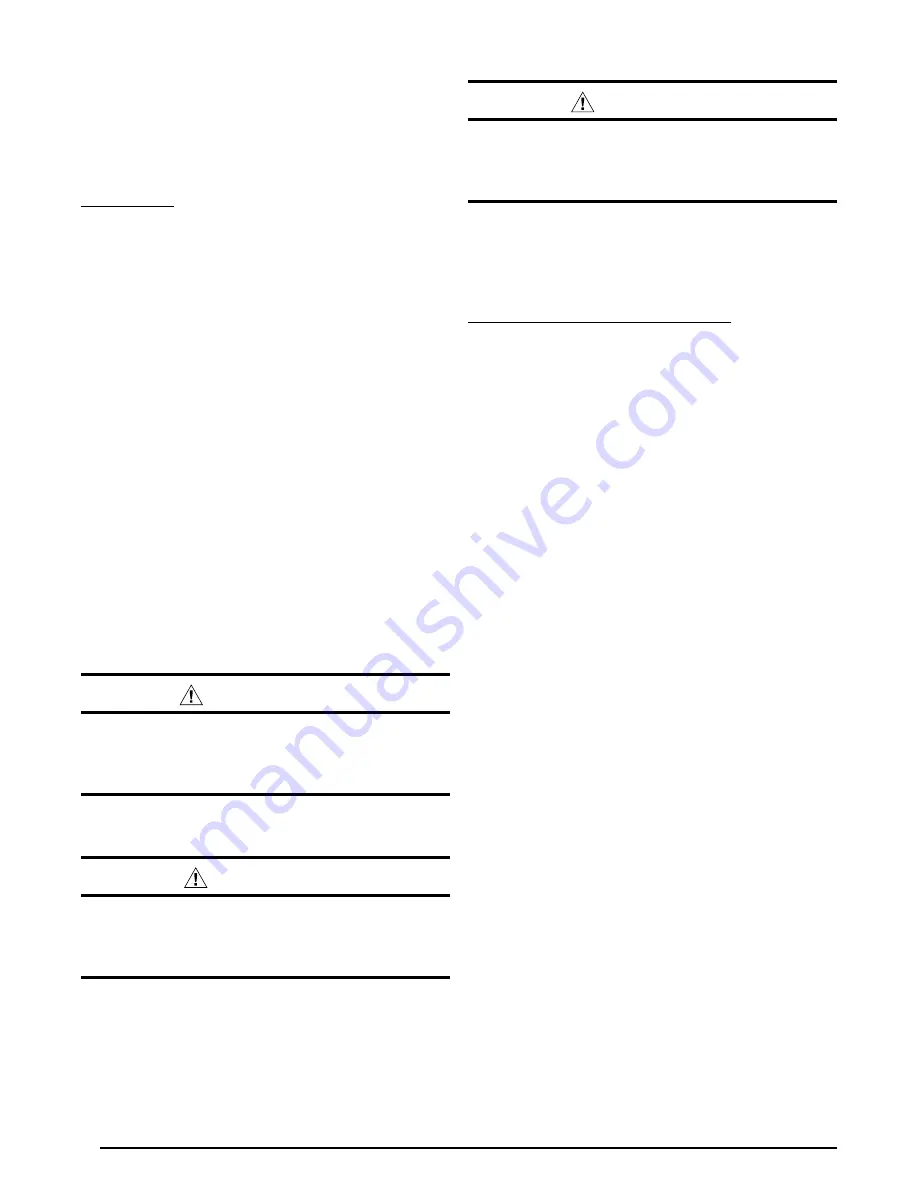
8
2 Stage Heat with Single Stage Heating Thermostat -
If a single
stage heat thermostat is used and 2 stage heat is desired,
an optional outdoor thermostat may be installed. Connect
the optional outdoor thermostat between the
W1
(
BROWN
)
connection and
ORANGE
wire in the outdoor unit. See
. Refer to the installation Instructions supplied with the outdoor
thermostat for setup details.
Cooling Mode
1. On a call for cooling, the thermostat closes, and applies
24VAC to the
G
&
Y1
terminals of the control. The compressor
contactor closes and operates the compressor in 1st stage.
2. If the thermostat is not satisfied in the required time (based
on the operation of the 2-stage cooling thermostat),
Y2
will
energize and the compressor will run at 2nd stage. Refer to
the thermostat’s Installation Instructions for the cooling profile.
3. When the thermostat is satisfied, the
G
&
Y
terminals on
the control board de-energized and open the compressor
contactor.
Electric Heat Package (optional)
This air conditioner is shipped without an auxiliary electric heat
kit installed. If electric heat is desired, an accessory heater kit
must be field installed.
• Select the correct size heat package for the installation. See
specifications sheet for available kits and application. Install
the heater kit according to the to the installation instructions
provided with the kit.
• Installation is most easily accomplished before making duct
or electrical connections.
• The blower must be set at the correct speed for the installed
electric heat kit. For airflow data, refer to
and the
installation instructions provided with the kit.
Blower Speed
For optimum system performance and comfort, it may be
necessary to change the factory speed setting. See
factory settings.
NOTE:
This model has a high efficiency ECM
motor with 5 speed taps.
WARNING:
To avoid electric shock, personal injury, or death,
turn off the electric power at the disconnect or the
main service panel before making any electrical
connections.
To Change the blower speed of the high efficiency motor:
1. Disconnect all electrical power to the unit and remove the
service panel.
CAUTION:
Label all wires prior to disconnection when
servicing controls. Wiring errors can cause
improper and dangerous operation. Verify proper
operation after servicing.
2. Locate the
RED
,
BLUE
and
ORANGE
wires terminated to the
blower motor. The
RED
wire controls the low speed cooling
and heating operations, the
BLUE
wire controls high speed
cooling and heating operations, and the
ORANGE
wire controls
the electric heating operation.
CAUTION:
To avoid personal injury or property damage,
make certain that the motor leads cannot come
into contact with any metal components of the
unit.
3. Verify the required speed from the airflow data found in
. Place appropriate wire on the appropriate
motor speed tap for the required airflow.
4. Check all factory wiring per the unit wiring diagram and inspect
the factory wiring connections to be sure none loosened during
shipping or installation.
Outdoor Motor - 4 & 5 Ton Models Only
The outdoor motor has variable speeds which adjust in
conjunction with the compressor and indoor blower motor. The
outdoor motor is preset at the factory and wired as shown:
• 4 Ton Model:
YELLOW
wire is connected to
Y1
and the
WHITE
wire is connected to
Y2
.
NOTE:
For 2nd stage, both
Y1
&
Y2
(
YELLOW
&
WHITE
) should be energized.
• 5 Ton Model:
WHITE
is connected to
NC
on blower relay.
YELLOW
is connected to
Y2
. For 1st stage only
WHITE
should be energized.
NOTE:
For 2nd stage, only
YELLOW
should be energized.
NOTE:
The
BLUE
wire from the outdoor ECM motor is always
common for either speed setting.
START UP & ADJUSTMENTS
Pre-Start Checklist
The following check list should be observed prior to starting
the unit.
√
Verify the unit is level and allows proper condensate drainage.
√
Verify the outdoor coil and top of the unit are free from
obstructions and debris, and all equipment access/control
panels are in place. Unit must be installed with the proper
√
Verify that the duct work is sealed to prevent air leakage.
√
Verify that the line voltage power leads are securely connected
and the unit is properly grounded. Check the condenser fan
to make sure it turns freely.
√
Verify the thermostat is wired correctly and installed in a
proper location. Make sure the low voltage wires are securely
connected to the correct leads on the low voltage terminal
strip.
√
Verify that the power supply branch circuit overcurrent
protection is sized properly.
Start-Up Procedure
NOTE:
The control circuit thermostat may consist of an anti-
short cycle timer that will not let the compressor re-start before
3 - 5 minutes have elapsed.
1. Set the system mode to OFF and the temperature mode to
its highest setting.
2. Turn power on at the disconnect switch.
3. Set the system mode to ON or COOL.
4. Set the temperature mode below room temperature. Verify
that the indoor blower, outdoor fan, and compressor energize
and the cooling function starts.
5. Verify the discharge air grilles are adjusted and the system
air is balanced.
6. Verify the duct work has no air leaks.
7. Verify the condensate drain is installed correctly and functions
properly.
8. Set the temperature mode above room temperature. The unit
should stop.