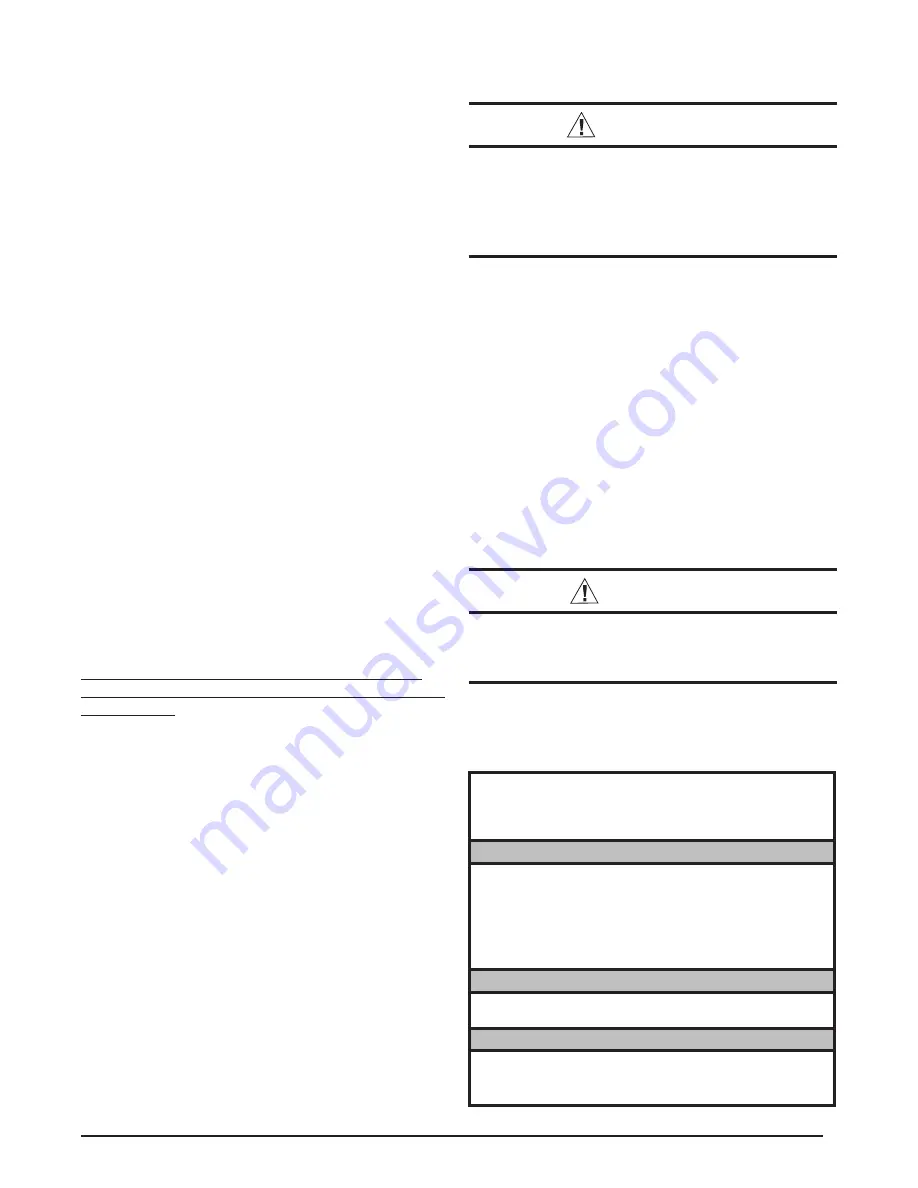
13
After refrigerant line connections are completed, it is
required that you leak check and evacuate the indoor
section and all line connections (using proper methods)
before fi nalizing the full system refrigerant charge. For
fi nal charges based on matched systems and specifi ed
line lengths, see physical and electrical specifi cations
(Table 4, page 15).
• To achieve rated capacity and effi ciency, the compressor
must be exposed to refrigerant for at least 24 hours
prior to running and then the compressor must be run
for a minimum of 12 hours.
• Cooling mode charging charts are applicable only to
matched assemblies of NORDYNE equipment and
listed airfl ows for the indoor coil. T5BP outdoor units
with indoor coils not listed are not recommended
and deviations from rated airfl ows or non-listed
combinations may require modifi cation to the expansion
device and refrigerant charging procedures for proper
and effi cient system operation. Refer to Figure 8 for
7.5 ton units or Figure 9 for 10 ton units (page 19).
• The refrigerant charge can be checked and adjusted
through the service ports provided external to the
outdoor unit. Use only gage line sets which have
a “Schrader” depression device present to actuate
the valve. A common suction port for heating mode
charging is included and located on the compressor
access panel above the outdoor unit service valves.
• Heat mode verifi cation charts are provided for quick
reference when the unit is in heating mode and for the
inspection of the liquid line pressures and temperatures.
Refer to Figure 10 for 7.5 ton units or Figure 11 for 10
ton units (page 21).
Charging an R410A system in AC mode at outdoor
temperatures above 55° F for optimized sub-cooling of
10° F to 12° F.
1. With the system operating at steady-state, measure
the liquid refrigerant pressure (in PSIG) at the outdoor
unit service valve.
2. Measure the liquid refrigerant temperature (in
Fahrenheit) at the service valve.
3. Determine the required liquid refrigerant pressure
from the appropriate charging chart (Figures 8 or 9).
• If the pressure measured in Step 1 is greater than
the required liquid refrigerant pressure determined in
Step 3, then there is too much charge in the system.
Remove refrigerant and repeat Steps 1 through 3
until the system is correctly charged.
• If the pressure measured in Step 1 is less than the
required liquid refrigerant pressure determined in
Step 3, there is too little charge in the system. Add
refrigerant and repeat Steps 1 through 3 until the
system is correctly charged.
HEAT PUMP MAINTENANCE
WARNING:
To prevent electrical shock, personal injury, or
death, disconnect all electrical power to the unit
before performing any maintenance or service.
The unit may have more than one electrical
supply.
Proper maintenance is important to achieve optimum
performance from the heat pump. The ability to properly
perform maintenance on this equipment requires certain
mechanical skills and tools. If you do not possess these
skills, contact your dealer for maintenance. Consult your
local dealer about the availability of maintenance contracts.
Routine maintenance should include the following:
• Inspect and clean or replace air fi lters at the beginning
of each heating and cooling season, or more frequently
if required.
• Inspect the condensate drain and outdoor coil at the
beginning of each cooling season. Remove any debris.
Clean the outdoor coil and louvers as necessary using
a mild detergent and water. Rinse thoroughly with water.
• Inspect the electrical connections for tightness at the
beginning of each heating and cooling season. Service
as necessary.
CAUTION:
The unit should never be operated without a
fi lter in the return air system. Replace disposable
fi lters with the same type and size.
• Do not attempt to add additional oil to motors
unequipped with oil tubes. The compressor is
hermetically sealed at the factory and does not require
lubrication.
REPLACEMENT PARTS
Replacement parts are available through all Nordyne distributors.
Please have the complete model and serial number of the unit
when ordering replacement parts.
ELECTRICAL:
Capacitors
Temperature Limit Switches
Compressors
Thermostats
Contactors
Time Delay Relays
Pressure Switches
Transformers
Relays
MOTORS:
Blower Motor
Fan Motor
COMPONENTS:
Blower Assembly
Fan Grille
Cabinet Panels
Filter/Driers
Expansion Valves