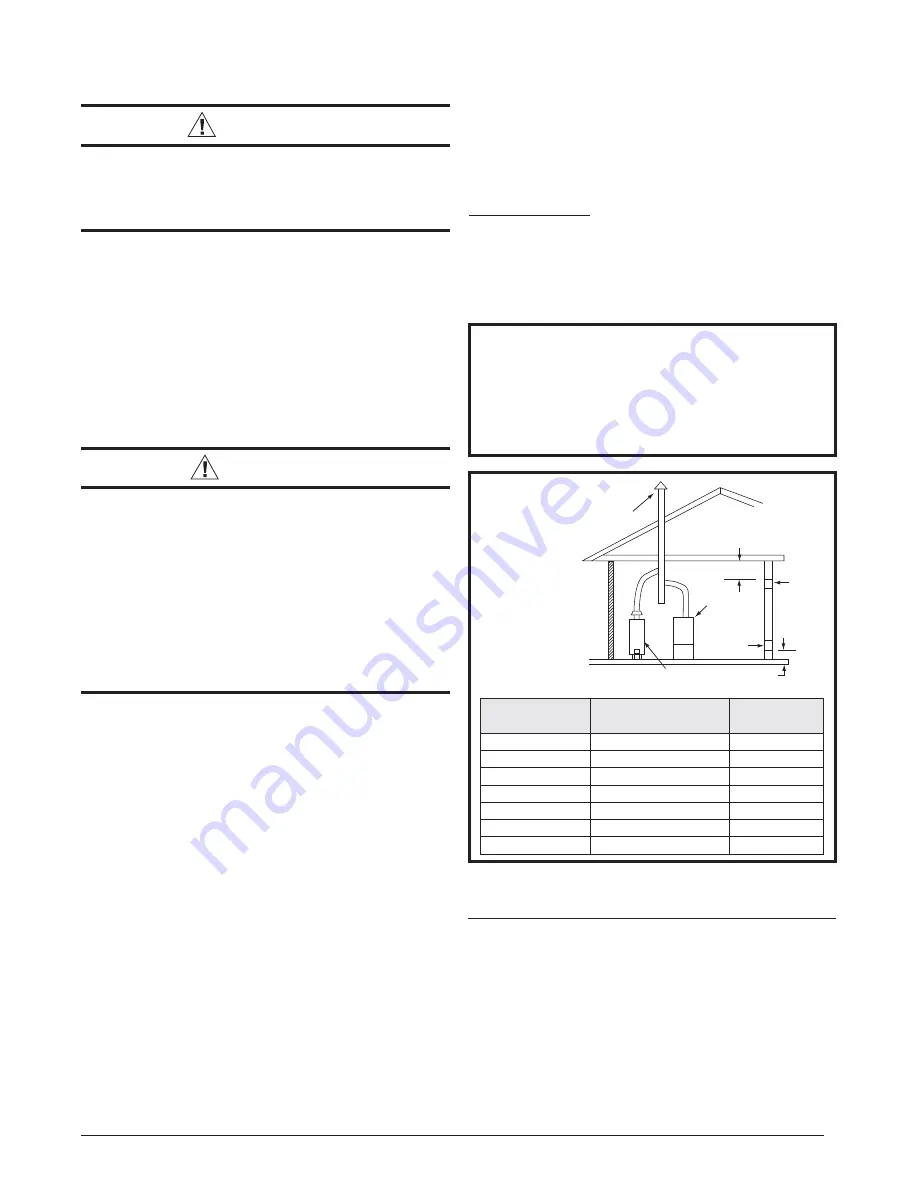
7
General Information
WARNING:
Furnace installation using methods other than
those described in the following sections must
comply with the National Fuel Gas Code (NFGC)
and all applicable local codes.
• Instructions for determining the adequacy of combustion
air for an installation can be found in the current revision
of the NFGC (ANSI Z223.1 / NFPA54). Consult local
codes for special requirements. These requirements
are for US installations as found in the NFGC.
• The requirements in Canada (B149.1) are structured
differently. Consult with B149.1 and local code offi cials
for Canadian installations.
Provisions must be made during the installation of
this furnace that provide an adequate supply of air for
combustion.
CAUTION:
Exhaust fans, clothes dryers, fi replaces and
other appliances that force air from the house
to the outdoors can create a negative pressure
inside the house, resulting in improper furnace
operation or unsafe conditions such as fl ame roll
out. It is imperative that suffi cient air exchange
with the outdoors is provided to prevent
depressurization. Additional information about
how to test for negative pressure problems can
be found in the NFGC.
Air openings on top of the furnace and openings in closet
doors or walls must never be restricted. If the furnace is
operated without adequate air for combustion, the fl ame
roll-out switch will open, turning off the gas supply to the
burners.
NOTE: This safety device is a manually reset
switch. DO NOT install jumper wires across these
switches to defeat their function or reset a switch
without identifying and correcting the fault condition.
If a switch must be replaced, use only the correct sized part
specifi ed in the Replacement Parts List provided online.
Installation In A Confi ned Space
A confi ned space is an area with volume less than 50
cubic feet per 1,000 Btuh of the combined input rates of
all appliances drawing combustion air from that space.
Furnace closets, small equipment rooms and garages are
confi ned spaces. Furnaces installed in a confi ned space
which supply heated air to areas outside the space must
draw return air from outside the space and must have the
return air ducts tightly sealed to the furnace.
The required sizing of these openings is determined by
whether inside or outside air is used to support combustion,
the method by which the air is brought to the space, and
by the total input rate of all appliances in the space. In
all cases, the minimum dimension of any combustion air
opening is 3 inches.
Air From Inside
If combustion air is taken from the heated space, the two
openings must each have a free area of at least one square
inch per 1,000 Btuh of total input of all appliances in the
confi ned space, but
not less than
100 square inches of
free area
(Figure 1). See example.
Example
:
If the combined input rate of all appliances is less
than or equal to 100,000 Btuh, each opening must
have a free area of at least 100 square inches. If the
combined input rate of all appliances is 120,000 Btuh,
each opening must have a free area of at least 120
square inches.
Furnace
12" Max.
Water
Heater
Vent or
Chimney
NOTES:
Each opening must
be at least 100 sq. in.
or 1 sq. in. per 1,000
Btuh of total input rating,
whichever is greater.
Openings must start at
no more than 12 inches
from the top and bottom
of the enclosure.
12” Max.
See
Notes
See Notes
Figure 1. Combustion Air Drawn from Inside
Total Input Rating
(Btuh)
Minimum Free Area
(Each Opening)
Round Duct
Diameter
40,000
100 sq. In
12 inches
60,000
100 sq. In
12 inches
80,000
100 sq. In
12 inches
100,000
100 sq. In
12 inches
120,000
120 sq. In
13 inches
140,000
140 sq. In
14 inches
160,000
160 sq. In
15 inches
Outdoor Air from a Crawl Space or Vented Attic
When the openings can freely exchange air with the
outdoors, each opening shall have a minimum free area
of 1 square inch per 4,000 Btuh of total appliance input.
The openings shall exchange directly, or by ducts, with
the outdoor spaces (crawl or attic) that freely exchange
with the outdoors (Figure 2, page 8).
Summary of Contents for *SA Upfl ow / Horizontal
Page 35: ...35...