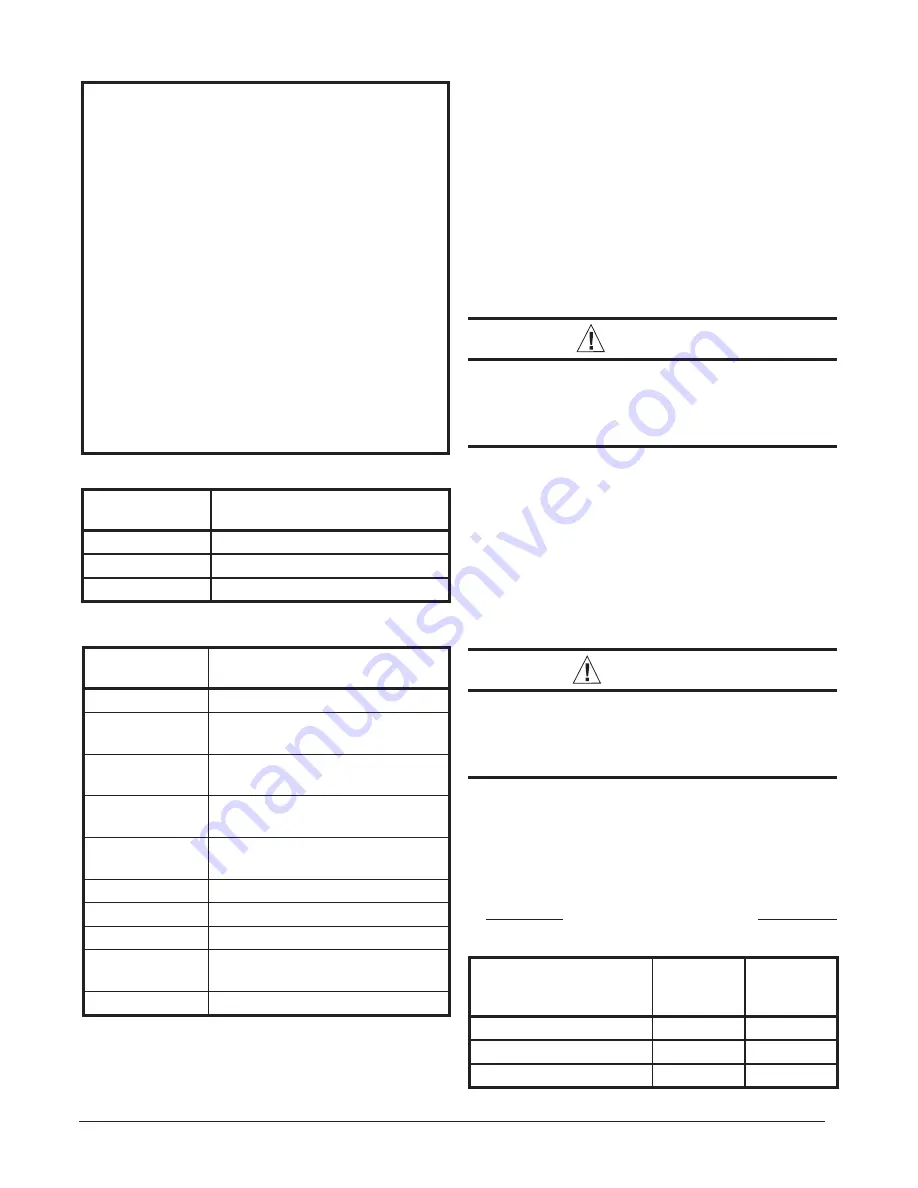
17
TROUBLESHOOTING
If the unit does not operate properly in the cooling
mode, check the following:
• The thermostat is operating properly.
• Electrical power to the unit is turned on.
• All safety switches are closed.
• The service doors are in place.
• Transformer circuit breaker is reset.
If the unit does not operate properly in the heating
mode, check the following:
• The thermostat is operating properly.
• Electrical power to the unit is turned on.
• All safety switches are closed.
• The gas is on and shut-off valve is open.
• The service doors are in place.
• The fl ame roll-out control is closed.
• Refer to the diagnostic codes in Tables 1 or 2, or the
wiring diagrams (Figures 15 - 19, pages 37 - 41).
• Transformer circuit breaker is reset.
Table 1. Diagnostic Codes For 7 1/2 & 10 Ton Units
STATUS LIGHT
(RED)
FAULT
CONDITION
Continuous ON
Internal Control Failure
2 Flashes
Flame Sense Problem
3 Flashes
Ignition Lockout
STATUS LIGHT
(Red LED)
FAULT
CONDITION
Continuous ON
Operation Normal
2 Flashes
Pressure/centrifugal switch open
with inducer on
3 Flashes
Pressure/centrifugal switch closed
with inducer off
4 Flashes
Lockout from too many
failed ignition tries
5 Flashes
Lockout from too many
fl ame losses
6 Flashes
High temperature switch open
7 Flashes
Rollout switch open
8 Flashes
Flame present with gas off
9 Flashes
Exceeded max limit trips (5)
in one call for heat
10 Flashes
Gas valve fault
Table 2. Diagnostic Codes For 6 Ton Units
UNIT MAINTENANCE
NOTE:
These maintenance instructions are primarily
intended to assist qualifi ed technicians experienced in the
proper maintenance and operation of this appliance
.
To achieve optimum performance from the air conditioner
and minimize equipment failure, it is recommended
that periodic maintenance be performed on this unit.
The ability to properly perform maintenance on this
equipment requires certain mechanical skills and tools.
Please consult your dealer for maintenance information
and availability of maintenance contracts.
CAUTION:
Use care when removing parts from this unit.
Personal injury can result from sharp metal
edges present in all equipment of sheet metal
construction.
At a minimum, routine maintenance should include the
following items:
Condensate Drain and Outdoor Coil
Inspect the condensate drain and outdoor coil at the
beginning of each cooling season. Remove any debris.
Clean the outdoor coil and hail guard louvers (optional)
as necessary using a mild detergent and water. Rinse
thoroughly with water.
Air Filters
WARNING:
Never operate the unit without fi lters in place. Dust
and lint in the return air can build up on internal
components, resulting in loss of effi ciency,
equipment damage, and possible fi re.
It is recommended that the air fi lters be inspected and
cleaned or replaced every three to four weeks using fi lters
of like size and kind. Table 3 lists the correct fi lter sizes
and quantities for each unit.
IMPORTANT NOTE: R6GP units are equipped with 2”
pleated disposable fi lters. Filter rack is adjustable for
1” permanent type fi lters. DO NOT use 1” disposable
fi lters.
UNIT
FACTORY
FILTER
SIZE
QTY
R6GP-072*-(100/166)C
16x20x2
4
R6GP-090*-200C
16x20x2
4
R6GP-120*-235C
16x25x2
4
Table 3. Filter Sizes and Quantities