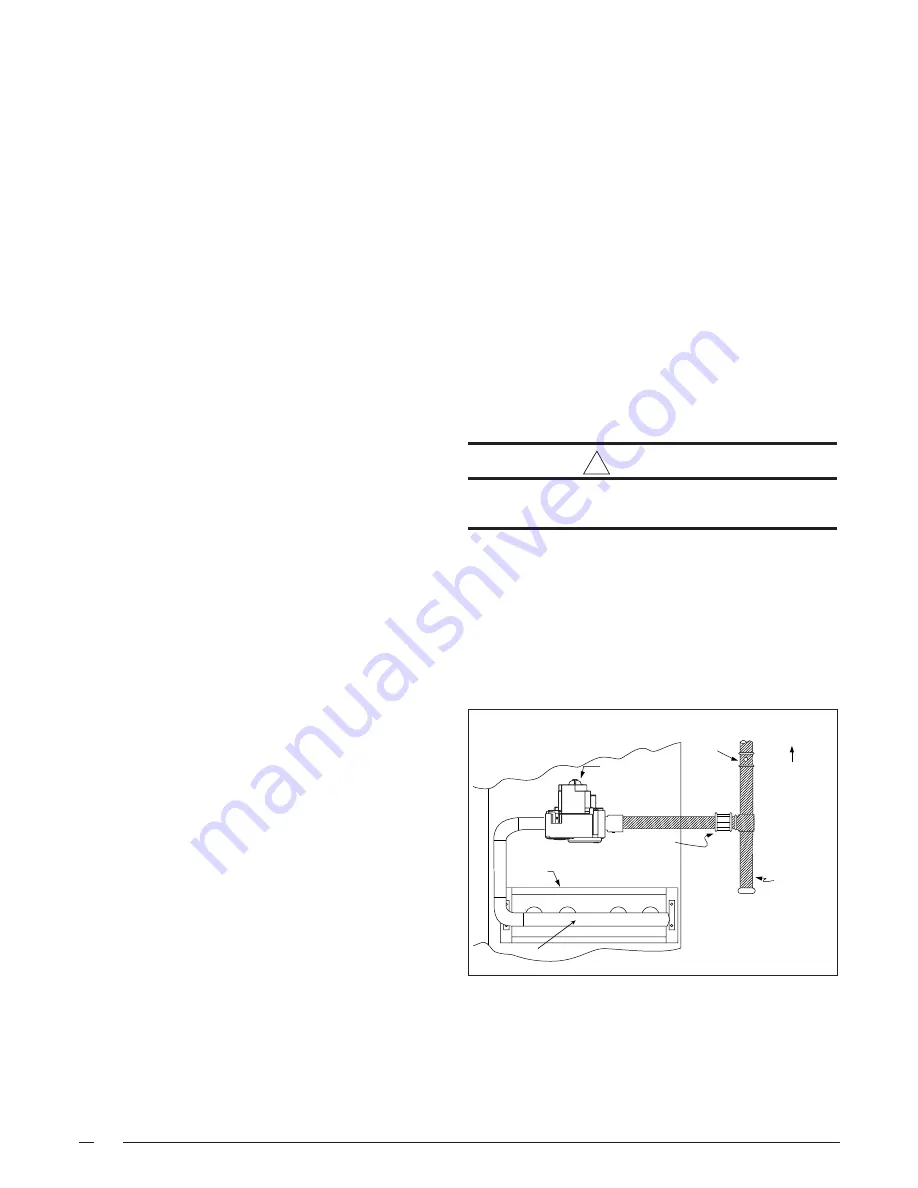
12
Figure 7. Typical Right Side Entry
Gas Service Connection.
Ground Joint
Union
Dripleg
Shut-Off Valve
with 1/8 NPT
plugged tap
Burner
Assembly
Manifold
Some utilities
require Shut-Off
Valve to be
4 to 5 feet
above floor
Automatic Gas
Valve (with manual
shut-off)
It is recommended that the outlet duct be provided with a
removable access panel. This opening should be accessible
when the unit is installed in service and shall be of a size
such that the smoke or reflected light may be observed
inside the casing to indicate the presence of leaks in the
heat exchanger. The cover for the opening shall be
attached in such a manner as to prevent leaks.
If outside air is utilized as return air to the unit for ventilation
or to improve indoor air quality, the system must be
designed so that the return air to the unit is not less than
50°F (10°C) during heating operation. If a combination of
indoor and outdoor air is used, the ducts and damper
system must be designed so that the return air supply to
the furnace is equal to the return air supply under normal,
indoor return air applications.
Unconditioned Spaces — All ductwork passing through
unconditioned space must be properly insulated to minimize
duct losses and prevent condensation. Use insulation
with an outer vapor barrier. Refer to local codes for
insulation material requirements.
Acoustical Ductwork — Certain installations may require
the use of acoustical lining inside the supply ductwork.
Acoustical insulation must be in accordance with the
current revision of the Sheet Metal and Air Conditioning
Contractors National Association (SMACNA) application
standard for duct liners. Duct lining must be UL classified
batts or blankets with a fire hazard classification of FHC-
25/50 or less. Fiber ductwork may be used in place of
internal duct liners if the fiber ductwork is in accordance
with the current revision of the SMACNA construction
standard on fibrous glass ducts. Fibrous ductwork and
internal acoustical lining must be NFPA Class 1 air ducts
when tested per UL Standard 181 for Class 1 ducts.
Horizontal to Down flow Conversion — The unit is
shipped ready for horizontal duct connections. If down
flow ducts are required, the unit must be converted following
the steps below for both the supply and return ducts.
1. Locate the duct cap inside the duct openings and
remove the screw holding it in place.
2. Lift the cap out of the unit. The cap can be pushed
up from the bottom by reaching through the fork slot.
3. Cover the horizontal duct opening with the cap. The
insulation will be on the indoor side.
4. Fasten the cover with screws and seal to prevent air
leakage.
GAS SUPPLY AND PIPING
This unit has right side gas entry. A typical gas service
hookup is shown in Figure 7. When making the gas
connection, provide clearance between the gas supply
line and the entry hole in the unit’s casing to avoid
unwanted noise and/or damage to the unit.
All gas piping must be installed in compliance with local
codes and utility regulations. Some local regulations require
the installation of a manual main shut-off valve and ground
joint union external to the unit. The shut-off valve should
be readily accessible for service and/or emergency use.
Consult the local utility or gas supplier for additional
requirements regarding placement of the manual main gas
shut-off. In the absence of local codes the gas line
installation must comply with the latest edition of the
National Fuel Gas Code ANSI Z223.1 or CAN/CGA B149
Installation Codes.
!
CAUTION:
Do not use matches, lighters, candles or other
sources of open flame to check for gas leaks.
A 1/8 inch NPT plugged tap must be installed in the gas line
immediately upstream of the gas supply connection to the
furnace for use when measuring the gas supply pressure.
The plug should be readily accessible for service use. A
drip leg should be installed in the pipe run to the unit. Table
4 lists gas flow capacities for standard pipe sizes as a
function of length in typical applications based on nominal
pressure drop in the line.