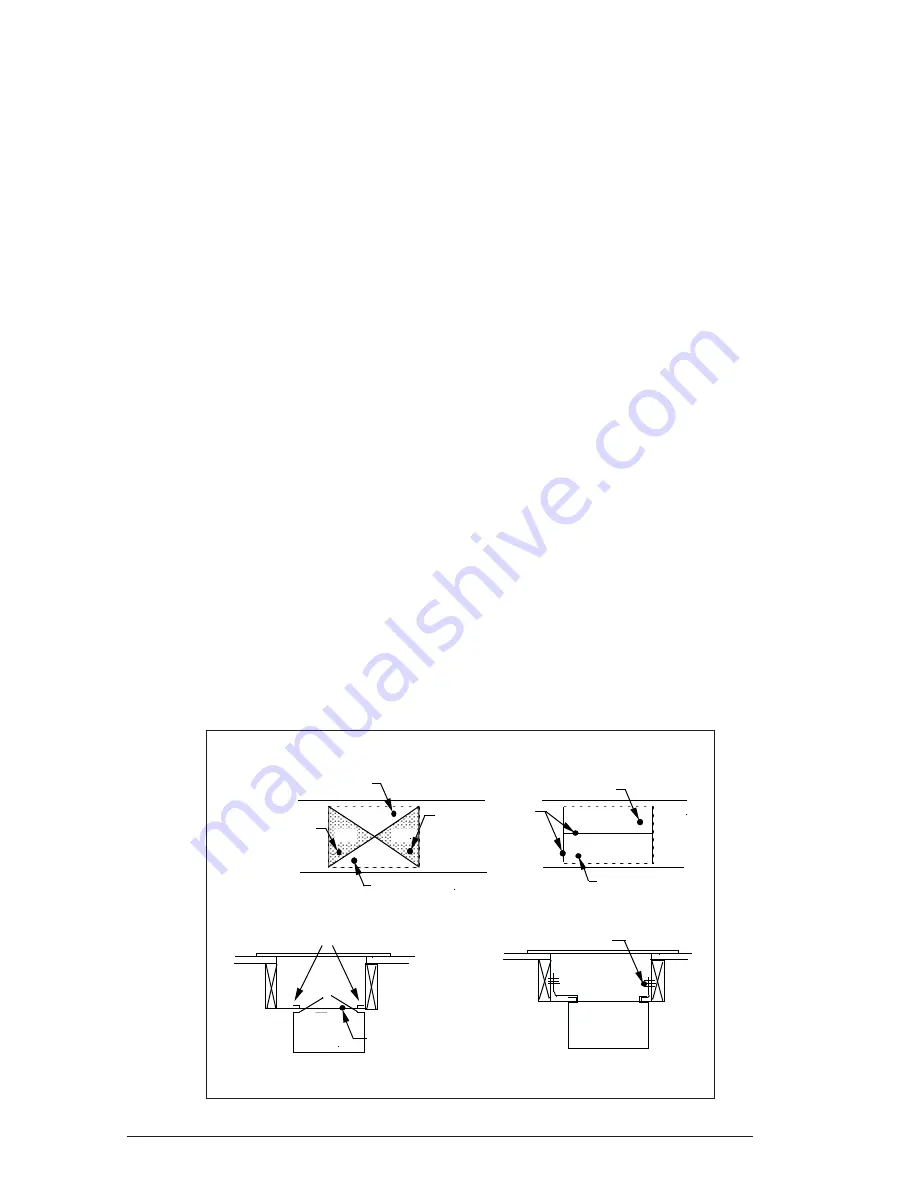
13
Staple Folded Duct
Flap (typ) to side of Duct
Connector
Duct
STEP 4.
STEP 1.
"A"
"A"
"B"
"B"
Cut- Out
Area"A"
Cut- Out
Area "A"
Fold Back Flap "B"
Fold Back Flap "B"
Top of Duct
"A"
"A"
STEP 2.
"B"
"B"
Fold Back Flap"B"
Cut
Lines
Duct
Fold Back Flap"B"
STEP 3.
Bend Duct Connector Tabs Up
and Over- (along length of duct)
Duct
Flap "B"
Duct
Figure 18.
INSTALL FURNACE
a. Remove furnace outer door(s) and bottom
fuel line knockout.
b. Place furnace onto duct connector and center
with fl oor opening.
c. Slide onto mounting plate. (Bottom rear slots
on furnace should engage with mounting plate
tabs.)
d. Secure front with one (1) fastener at each
corner (See Figure 19 or 20).
NOTE:
Additional fasteners may be used at rear,
sides or through door frame, as desired, to secure
furnace to closet or alcove framing.
INSTALL ROOF JACK
Apply caulking compound on underside of roof
fl ashing to form a continuous strip at least 3/8”
wide (see Figure 21) around the underside of
the perimeter of the fl ashing. Connect Roof Jack
Assembly to the furnace. Insert telescoping
Roof Jack Assembly through the opening cut
on the roof. Connect fl ue pipe to fl ue collar of
furnace. Connect combustion air pipe to furnace
collar with sheet metal screw (See Figure 22).
It is recommended that the connection of the
combustion air pipe to the furnace be made
before the fl ashing is secured to the roof to
maintain alignment of roof jack and furnace
connections.
NOTE:
For replacement furnaces, be sure the
inner fl ue pipe connects over the furnace vent
collar.
DO NOT use a smaller diameter inner
fl ue pipe which could slide inside the furnace
vent collar and restrict the fl ow of furnace
fl ue products.
Attach Roof Flashing: If necessary, shift roof
fl ashing slightly in the roof opening so that as-
sembly is in good alignment with furnace. Press
down fi rmly over caulking on roof fl ashing to make
the seal with roof water tight. Secure fl ashing with
appropriate fasteners. As an added protection
against leaks, coat the fl ashing plate and fasten-
ers with approved roofi ng compound.
If fl ashing mounted on 12 degree angle is used
it may be necessary to adjust the angle to match
the roof pitch; (1/12 - 4/12 maximum).
12. INSTALLATION OF TRANSIT-
MODE VENTING SYSTEM
MANUFACTURED HOME FACTORY
a. Furnace to be installed per furnace installation
manual.
b. Roof Jack to be selected from Table 5 of these
instructions.
c. Roof Jack (less upper Roof Jack crown), with
weather cap to be installed as described under
Install Roof Jack.
d. Upper Roof Jack crown to be stored in a
prominent location inside manufactured home
until on-site installation.
e.
The four warning tags supplied must be
installed as follows:
• To weather cap
• To fuel line connection point (Gas) or
furnace burner (Oil)