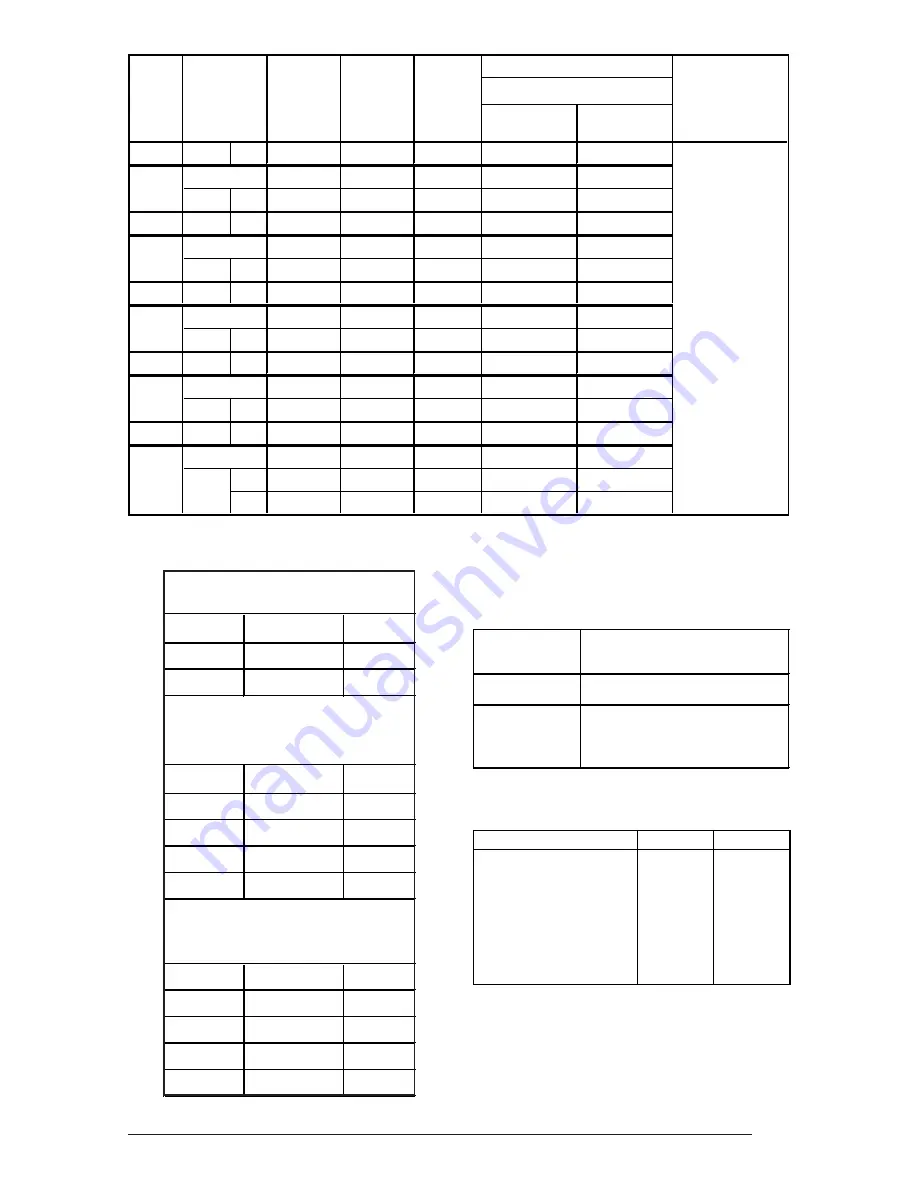
19
Standard 2-Speed Blower,
with filter, @ 0.3" ESP
Pin No.
Speed
CFM
#1
Low
840
#2
High
1160
4-Ton Blower with Coil and
Coil Filters, @ 0.3" ESP
Pin No.
Speed
CFM
#1
Low
880
#2
Med.-Low
1170
#3
Med.-High
1310
#4
High
1460
5-Ton Blower, with Coil and
Coil Filters, @ 0.3" ESP
Pin No.
Speed
CFM
#1
Low
990
#2
Med.-Low
1320
#3
Med.-High
1620
#4
High
1790
Sizes*
Model
Max Over-
Min.
75°C Copper
Low-Voltage
E2EH/
E2EB-
Supply
Circuit
Total
Amperes
Current
Rating
Circuit
Ampacity
Wire Size
Ground Size
Thermostat Wire
Size
010
Single
45.5
60
57
6
10
012
Single
52.1
70
65
6
8
Dual
"A"
28.0
40
35
8
10
"B"
24.2
30
30
10
10
015
Single
66.3
90
83
4
8
Dual
"A"
45.5
60
57
6
10
"B"
20.8
30
26
10
10
017
Single
71.3
90
89
3
8
Dual
"A"
48.8
60
61
6
10
"B"
22.5
30
28
10
10
020
Single
87.1
125
109
2
6
Dual
"A"
45.5
60
57
6
10
"B"
41.7
60
52
6
10
023
Single
93.8
125
117
1
6
Dual
"A"
45.5
60
57
6
10
"B"
48.3
60
60
6
10
2-Wire
system max
wire lengths :
24 Ga. = 55’
22 Ga. = 90’
20 Ga. = 140’
18 Ga. = 225’
4 or more-Wire
system max
wire lengths :
24 Ga. = 25’
22 Ga. = 45’
20 Ga. = 70’
18 Ga. = 110’
Table 6. Electrical Specifications
Table 7. Blower Performance
Table 8. Anticipator Settings
* All wire sizes for copper conductors only, based on NEC Table 310-16. Equivalent wiring may be used per NEC.
Furnace
Thermostat
Model
Anticipator Setting
010, 012
0.20
015, 017,
020, 023
0.40
ALL MODELS
CLOSET
ALCOVE
Front ‡
6"
18"
Back
0"
0"
Sides
0"†
0"†
Top
0"
0"
Top and Sides of Duct
0"
0"
Bottom of Duct
0"
0"
‡ Service Clearance
† For upflow application using upflow stand,
1" minimum per side.
Table 9. Clearances