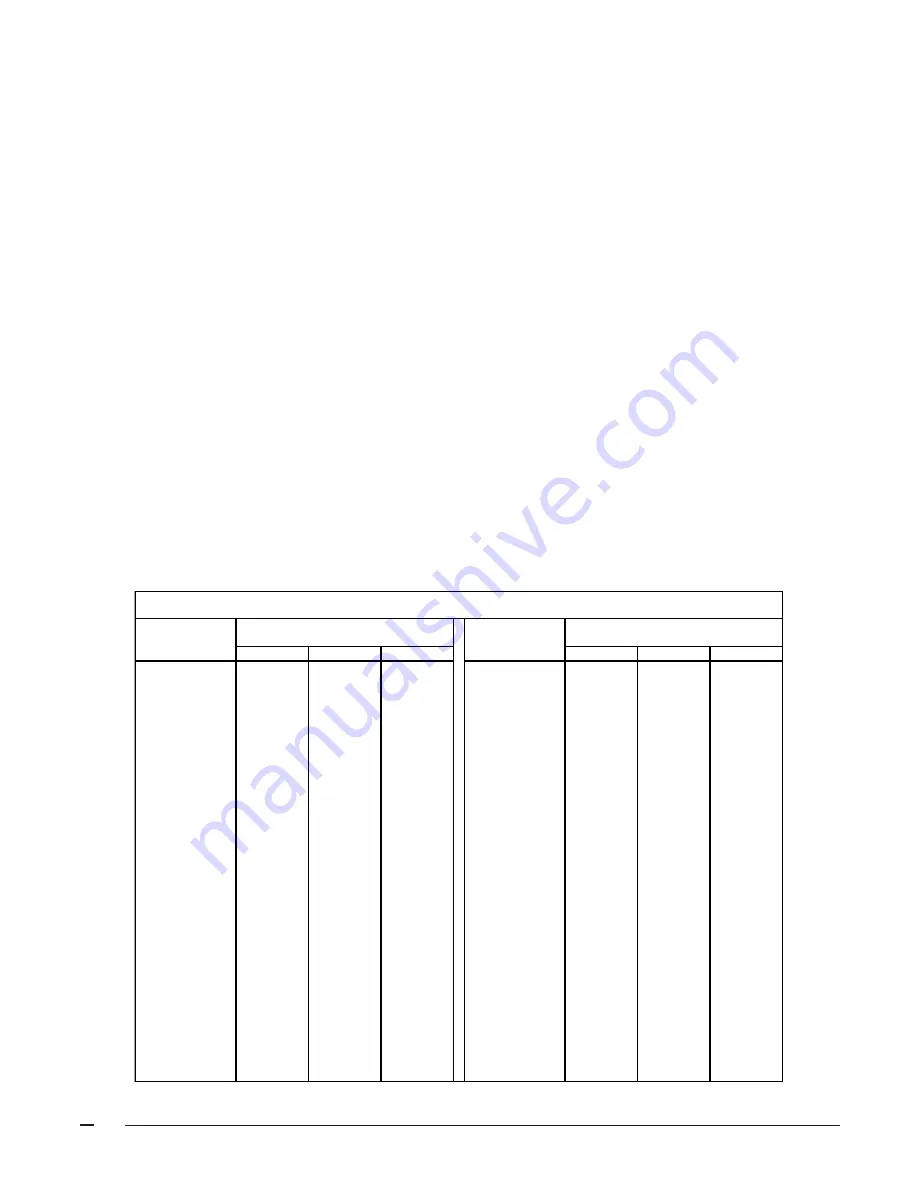
26
Table 11. Gas Flow Rate
TIME FOR
TIME FOR
ONE REVOLUTION
ONE REVOLUTION
(SECONDS)
1
5
10
(SECONDS)
1
5
10
10
360
1800
3600
66
55
273
545
12
300
1500
3000
68
53
265
529
14
257
1286
2571
70
51
257
514
16
225
1125
2250
72
50
250
500
18
200
1000
2000
74
49
243
486
20
180
900
1800
76
47
237
474
22
164
818
1636
78
46
231
462
24
150
750
1500
80
45
225
450
26
138
692
1385
82
44
220
439
28
129
643
1286
84
43
214
429
30
120
600
1200
86
42
209
419
32
113
563
1125
88
41
205
409
34
106
529
1059
90
40
200
400
36
100
500
1000
92
39
196
391
38
95
474
947
94
38
191
383
40
90
450
900
96
38
188
375
42
86
429
857
98
37
184
367
44
82
409
818
100
36
180
360
46
78
391
783
102
35
176
353
48
75
375
750
104
35
173
346
50
72
360
720
106
34
170
340
52
69
346
692
108
33
167
333
54
67
333
667
110
33
164
327
56
64
321
643
112
32
161
321
58
62
310
621
114
32
158
316
60
60
300
600
116
31
155
310
62
58
290
581
118
31
153
305
64
56
281
563
120
30
150
300
GAS FLOW RATE (CUBIC FEET PER HOUR)
CUBIC FEET PER REVOLUTION OF
METER
CUBIC FEET PER REVOLUTION OF
METER
Selecting The Cooling/Heat Pump Airflow
In order to select the appropriate airflow for AC and HP
operation the nominal system capacity must be known.
The nominal system capacity is ALWAYS the nominal
capacity of the outdoor unit. In some cases the nominal
system capacity is not the same as the nominal capacity
of the indoor coil.
The cooling/heat pump airflow is selected by setting
switches 1 through 4 on the motor control board located in
the blower control panel. All airflows for other modes of
operation (except gas heat) are determined by this setting.
Table 1 shows the airflow values versus the airflow selector
switch settings, and the range of airflow settings recom-
mended for each nominal system capacity.
NOTE: The CFM values listed on Table 2 are not
dependent on duct static pressure. The motor auto-
matically compensates for changes in duct static pres-
sure (within the limits of the motor).
For Two Stage Cooling:
The furnace is supplied with the yellow "Y1" and blue "Y2"
connections attached to the control board. When installing
this furnace with a two stage condensing unit, remove the
blue "Y2" wire from the control board and connect to the
thermostat. Connect a field supplied wire from the yellow
"Y1" to the thermostat and the condensing unit, and
another wire from "Y2" on the thermostat to "Y2" on the
condenser. (See Figure 23).
For maximum capacity and energy efficiency, generally, a
selection at or near the top of the CFM range for that
nominal capacity is best. For maximum dehumidification,
select an airflow near the middle or bottom of the CFM
range for that nominal capacity.
IMPORTANT NOTE: When installing a 2-stage heat
pump with a fossil fuel kit, the transformer in the
furnace MUST be upgraded to one with a 60VA rating
(Part No. 904077)
.
NOTE: If coil icing is observed, the cooling/heat pump
airflow selected may be too low. Double-check to be
sure the setting selected is within the range shown in
Table 1. Also check to be sure the system is properly
charged (see outdoor unit installation instructions). If
icing continues to occur, raise the selected airflow one
or two steps.
Verifying and Adjusting Temperature Rise
Verify the temperature rise through the furnace is within the
range specified on the furnace rating plate. Temperature
Summary of Contents for 060C-12
Page 2: ......