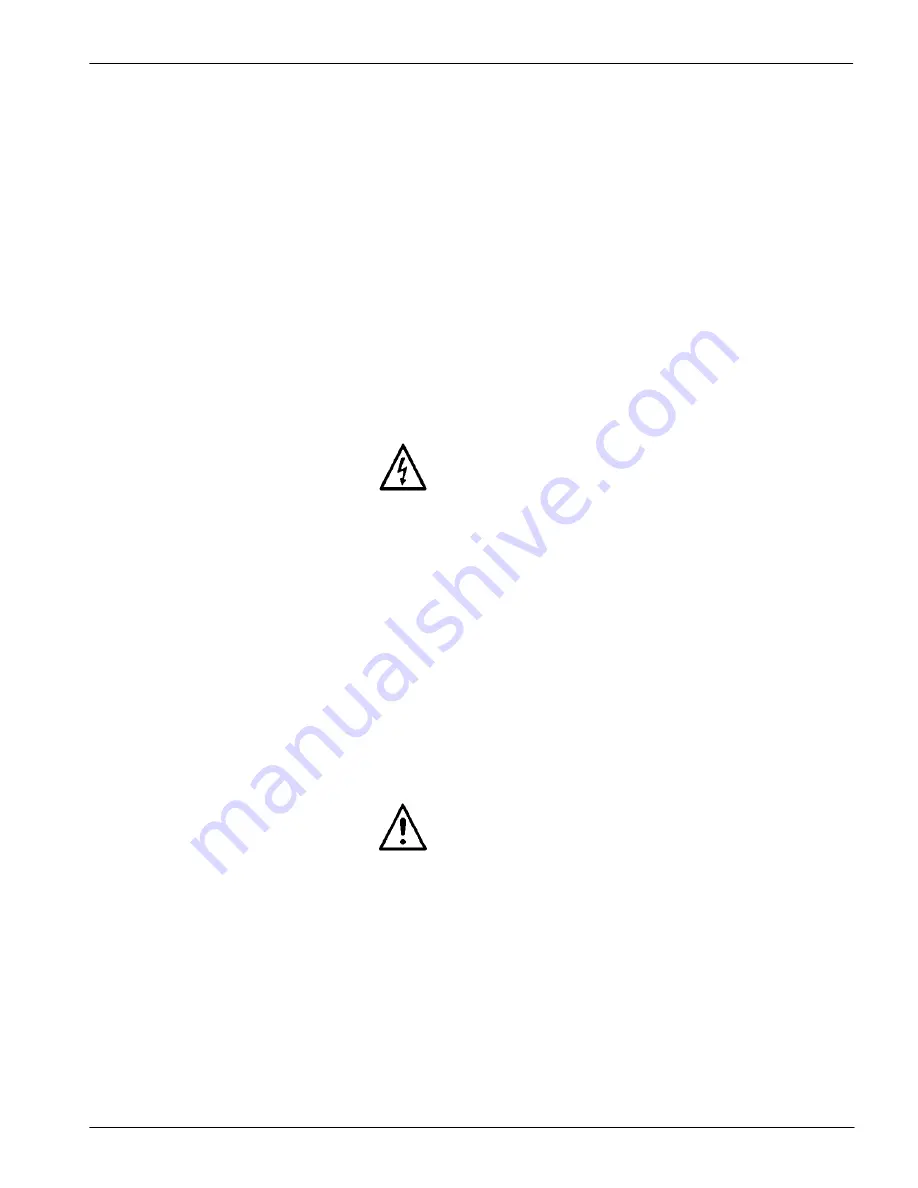
Installation
3
Nordson Corporation 1994
All Rights Reserved
108 129
Issued 3/94
Manual No. 31
−
13
The electrostatic cable should not be bent in a radius of less than 6
inches (152 mm), nor subjected to any strain. Use elastic bands or
cable ties to secure the cable and tubing to the mounting bar and
reciprocator arm, if used, so that any strain is taken up by the
tubing, not the cable.
3.
Connect powder feed tubing to the powder pump. Wrap spiral-cut
tubing around the feed tubing wherever necessary to prevent it
from kinking.
NOTE:
To increase powder flow and keep distribution as even as
possible, the powder feed tubing should be kept short. Ideally, the
tubing should not be longer than 26 ft (8 meters).
4.
Connect the high voltage cable to the electrostatic power supply,
as described in your power supply manual. Make sure the cable
end is clean and dry before connecting.
WARNING
: The electrostatic equipment in itself is safe.
However, metal objects in the spray area that are isolated
from ground accept and store an electrical charge and can
become unsafe. Ungrounded workpieces present a fire
hazard and also lose transfer efficiency. For these reasons,
all objects and the work in the spray area MUST BE
PROPERLY GROUNDED.
1.
Remove the flat spray nozzle and the flat spray wear sleeve from
the gun.
2.
Install the conical wear sleeve over the electrode and resistor
assembly. Be careful not to bend the electrode. DO NOT use the
conical nozzle without the wear sleeve.
3.
Ensure that the O-rings are in place on the nozzle. Press the
nozzle into the end of the gun with a slight twisting motion until the
nozzle bottoms out.
CAUTION
: The electrode has a very sharp tip. Install the
deflector by its edges only. DO NOT push the deflector onto
the resistor with your palm. Personal injury may result.
4.
Install the conical deflector over the resistor. The deflector should
bottom out on the wear sleeve.
5.
Slide the pattern adjuster sleeve onto the nozzle, with the hole in
the sleeve towards the mounting block end of the gun.
6.
Slip the end of the adjuster rod under the pattern adjuster sleeve,
so that the rounded pin on the end of the adjuster rod goes into the
hole in the sleeve.
Installation
(contd.)
Installing Optional 32 mm
Conical Nozzle