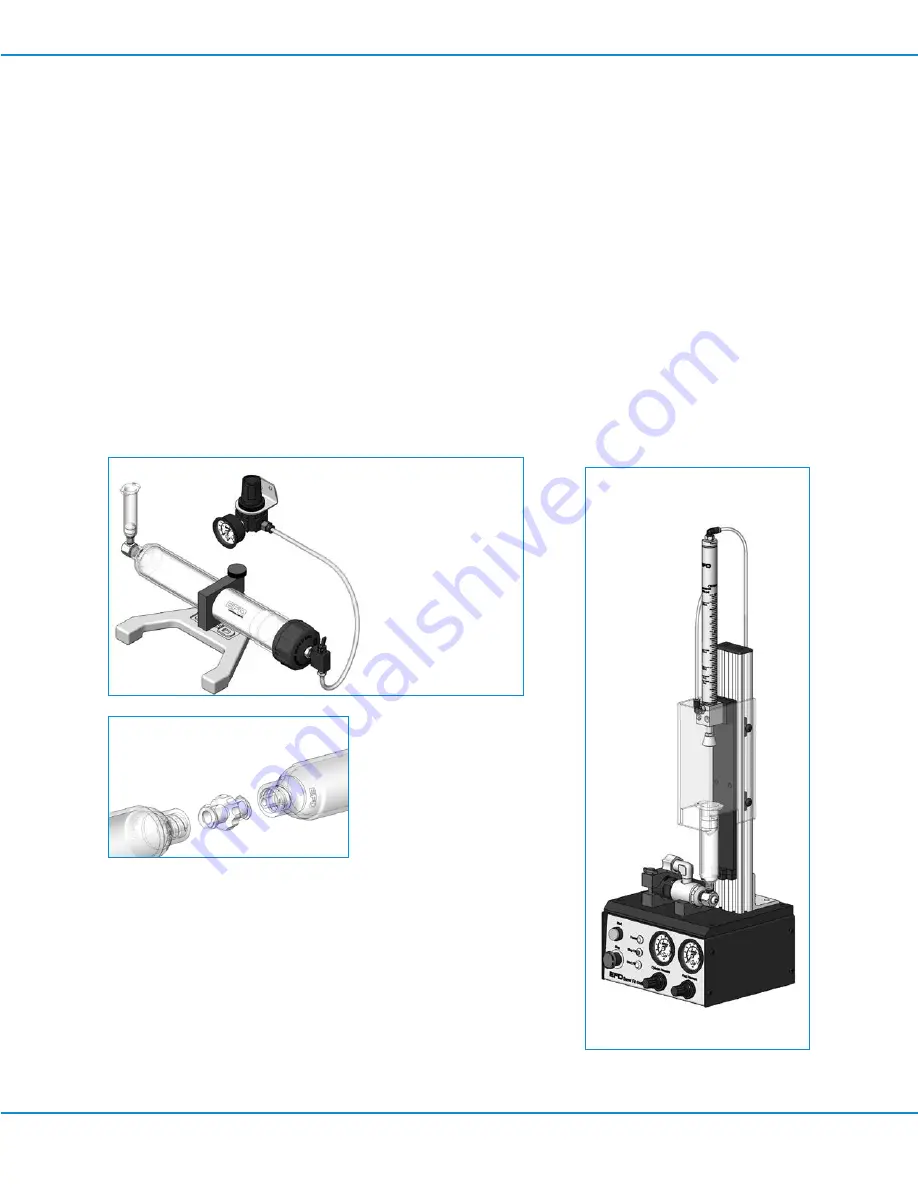
System Setup and Operation (continued)
Luer-to-luer fitting
P/N 7012606 100 pack
P/N 7014838 1 piece
P/N 7022068 Atlas Filling System
Syringe Barrel Filling Alternatives
Nordson EFD offers productive alternatives to traditional syringe barrel filling methods. Here are a few suggestions
that can help keep your work area clean, save time, and reduce the chance of entrapped air in the fluid.
• Use the Atlas
™
Filling System, P/N 7022445 (12 fl oz). Pack the fluid into a 2.5 fl oz, 6 fl oz, 12 fl oz, 20 fl oz, or
32 fl oz cartridge as shown. Then place the pre-filled cartridge into the barrel loader. Using air pressure, the barrel
loader fills the syringe barrel (with a piston installed) from the bottom up.
If the fluid comes packed in a 300 mL (1/10 gallon) caulking type cartridge, use the EFD P/N 7022452 filling
system.
For fast, volumetric filling, the P/N 7022068 Atlas Filling System is an accurate, easy, and fast system for filling
syringe barrels.
• If you receive frozen epoxies or other fluids in medical type syringes with a manual plunger, request the EFD luer-
to-luer fitting to transfer the material.
Contact an EFD fluid application specialist for additional assistance.
P/N 7022445 (12 fl oz) Atlas Filling
System. Also available in 2.5, 6, 20,
and 32 fl oz.
P/N 7022452 for pre-filled 300mL
(1/10 gal) caulking tubes.
Performus I Dispensing System
18
www.nordsonefd.com [email protected]
+1-401-431-7000 Sales and service of Nordson EFD dispensing systems are available worldwide.