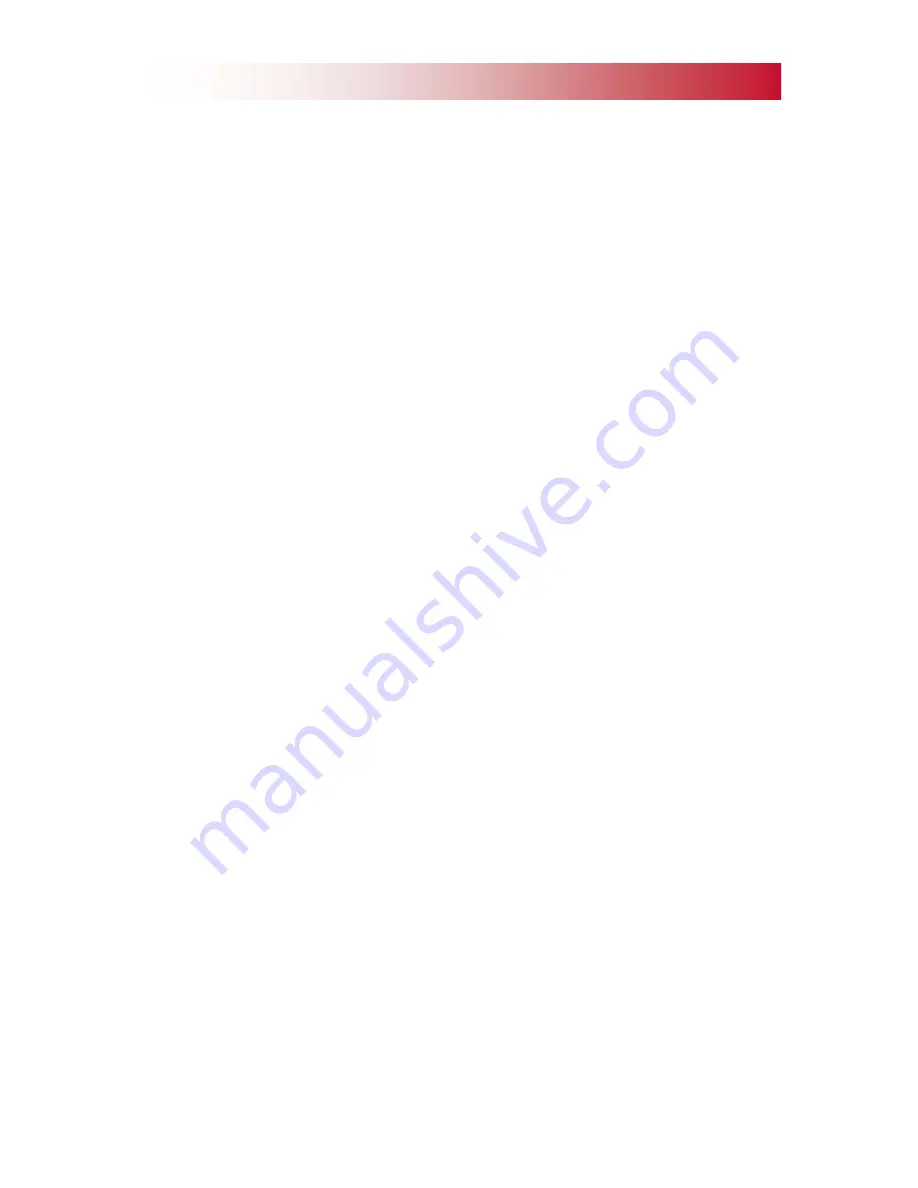
34
Minimum heating set point (supply air) to be
maintained above room set point.
Maximum heating set point (supply air) 26
o
C.
Consecutive heating stages activated by Trend
to provide overlap to encourage multiple stages
at part load in preference to single stage at or
near full load. This is to derive maximum benefit
from increased COP at part condenser load.
S1 Heating Control Heatpump & Gas
Heatpump
Heatpump heating used above 5
o
C ambient
temperature.
Stages (condensers) 1 and 2 (and 3 where
applicable) activated by Trend from T1 sensor.
Trend dictates required supply air temperature
via 0 -10v output simultaneously to each
Mitsubishi FTC controller.
Each Mitsubishi FTC controller controls relevant
condenser output to achieve supply air set point
as dictated by Trend 0-10v output.
Minimum heating set point (supply air) to be
maintained above room set point.
Maximum heating set point (supply air) 26
o
C.
Consecutive heating stages activated by Trend
to provide overlap to encourage multiple stages
at part load in preference to single stage at or
near full load. This is to derive maximum benefit
from increased COP at part condenser load.
Gas Heater (Benson Heater)
Gas heater used below 5
o
C
ambient
temperature.
0-10v Trend control output via AHU terminal rail
to heater 3RM board for two stage heater
control.
(Nordair/Benson to develop modulating burner
control in future).
Trend control direct from T1 kitchen sensor and
not via supply duct temperature.
Burner fault indication to Trend via AHU terminal
rail.
S1 Heating Control Heatpump & Electric
heater
Mitsubishi controls if required by plugging into
AHU mounted socket provided in S1 and S2 air
handling units (Note: Keypad controller should
not normally be required for commissioning).
Condenser power supplies from factory fitted
mcb’s in AHU via terminal rail with external
wiring by electrical contractor with local isolator
at each condensing unit.
Hardwired control cabling from factory fitted
FTC’s in AHU via terminal rail with external
wiring by electrical contractor.
Modbus ‘daisy chain’ network cabling to be
connected to condensers when Mitsubishi
confirm availability – initially for monitoring
purposes only.
Condenser operation interlocked with supply fan
run control, fire alarm activation and no flow/fault
alarm from supply fan inverter.
S1 Cooling
Stages (condensers) 1 and 2 (and 3 where
applicable) activated by Trend from T1 room
sensor.
Trend dictates required supply air temperature
via 0-10v output simultaneously to each
Mitsubishi FTC controller.
Each Mitsubishi FTC controller controls relevant
condenser output to achieve supply air set point
as dictated by Trend 0-10v output.
Minimum cooling set point (supply air) 12
o
C.
Consecutive cooling stages activated by Trend
to provide overlap to encourage multiple stages
at part load in preference to single stage at or
near full load. This is to derive maximum benefit
from increased COP at part condenser load.
All stages cooling held off below 12
o
C ambient.
S1 Heating Control Heatpump Only (where
no gas or electric heating installed)
Stages (condensers) 1 and 2 (and 3 where
applicable) activated by Trend from T1 sensor.
Trend dictates required supply air temperature
via 0-10v output simultaneously to each
Mitsubishi FTC controller.
Each Mitsubishi FTC controller controls relevant
condenser output to achieve supply air set point
as dictated by Trend 0-10v output.
7. Controls cont.