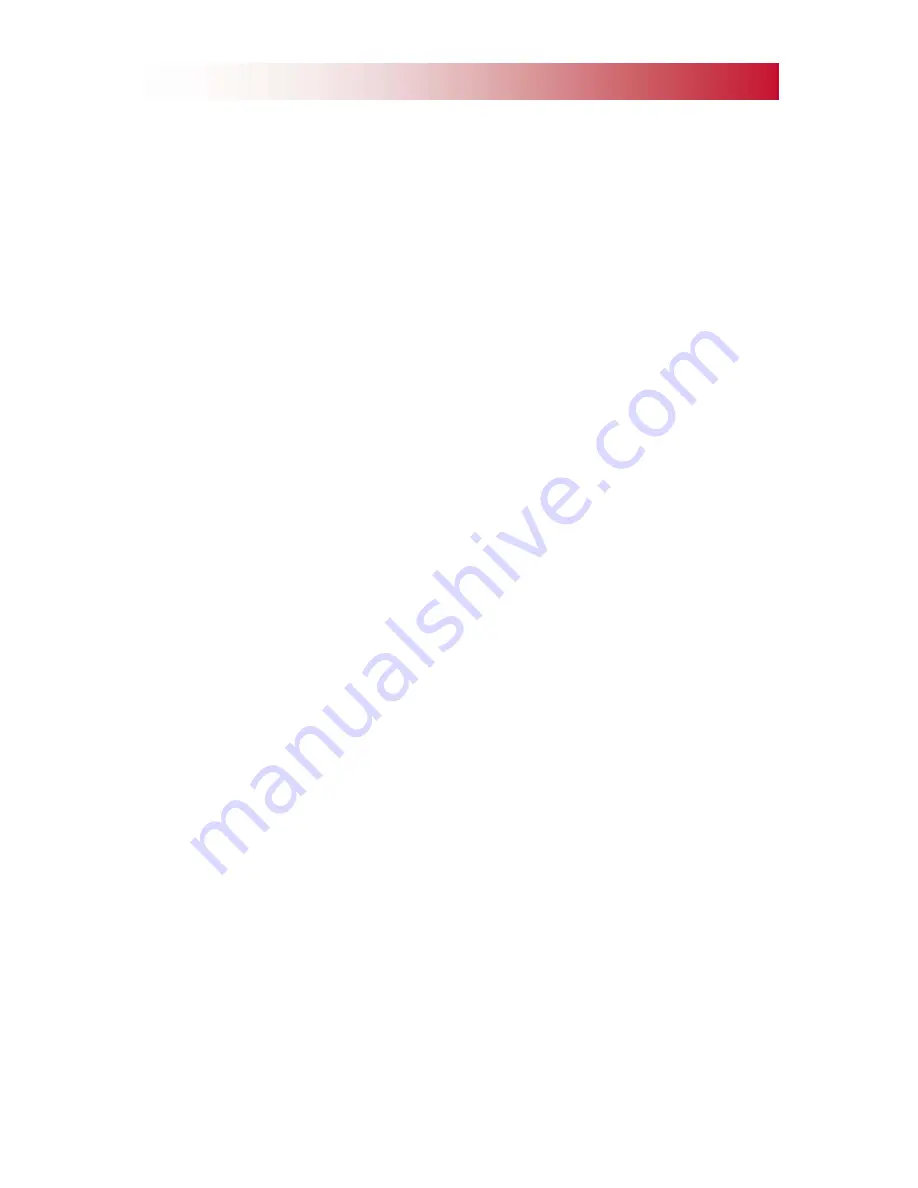
23
manufactured and pre set for use with Natural/
lpg Gas, and all feature 1/2” or 3/4” BSP
connections. Prior to installation the supply
characteristics (gas type and pressure) must be
checked to ensure that they are in accordance
with the data plate on the heater.
The gas supplier should check that the meter
and service connection to the heater are capable
of delivering the required volume of gas, thereby
ensuring that the minimum burner pressure can
be achieved.
Consideration should be given to the pressure
drop on single and multi heater installations and
the effect they may have on other plant sharing
the supply.
If it is necessary to fit a gas pressure booster, the
controls must include a low pressure cut off
switch which must be fitted on the supply / inlet
side of the booster. It is also a requirement that
the gas supplier is advised prior to the
installation or fitting of the booster.
Each heater supply must be fitted with a
separate isolating cock positioned adjacent to
and upstream of the union which must be sited
outside the heater.
The isolating cock should be of the 90° turn type
and should be clearly marked
OPEN / CLOSED
it should also be installed so as to fall to the
closed position.
An approved gas jointing compound must be
used on all joints and unions and the system
purged and tested for soundness prior to final
connection.
The connection to the heater can be made by
way of either an approved flexible coupling or
rigid connection. Threaded connections must
comply to ISO 288/1 or ISO 7/1 further
information concerning accepted European
practice is detailed in BS EN1020.
The diameter of the pipework from the isolating
cock to the burner must not be less than the
diameter of the connection into the gas multi-
block.
Note
Reference to The Institute of Gas Engineers
publications Utilisation Procedures IGE/UP1 and
IGE/UP2 together with reference to BS6891 is
strongly advised.
6.3.0 Commissioning
Note:
It is a requirement that only suitably qualified
and competent personnel are allowed to
undertake the commissioning of the heater.
It is also strongly recommended that prior to
commissioning the engineer familiarises
himself
with
the
heater,
the
specific
requirements of the installation / application,
and the information contained within the
manual.
Warning
All heaters are subject to a rigorous test
programme prior to despatch, whilst such a
programme does involve pre-commissioning and
the setting of the heater to operate efficiently and
within its designed operational limits, this does
not mean that the function of thorough on site
commissioning is less important.
It is strongly recommended that the equipment
used for the sampling and analysis of the flue
gases is accurate to /- 0.1% and
maintained so that it is regularly calibrated.
The following pre-commissioning checks should
be undertaken, having first ensured that the gas
and electrical supplies are turned off.
(a) Check that all panels and fasteners are
secure and in place.
(b) Check that the heater is mounted safely.
(c) Check that the flue is sealed, secured, and
adequately supported.
(d) Check that the fan is free to rotate, that the
fan is secured to its shaft, and that the guards
and fan assembly are all in place and properly
secured.
(e) Check that the heater is installed so that it is
not tilted and remains square.
(f) Check that the outlet louvres (Axial heaters)
are set to offer minimum resistance to air flow.
6.3.1 Electrical pre-tests
The electrical safety checks must include the
following:
a) Test for earth continuity.
b) Test for resistance to earth.
c) Check live and neutral connections are
correct.
d) Check to ensure that when the external
controls operate to switch the heater off, power
remains to the fan.
6.3.2 Gas supply pre-test
Ensure that the service pipework has been
installed, purged and tested in accordance with
the relevant regulations, and that the installation
is served by an adjacent isolating cock.
6. Commissioning & Testing cont.