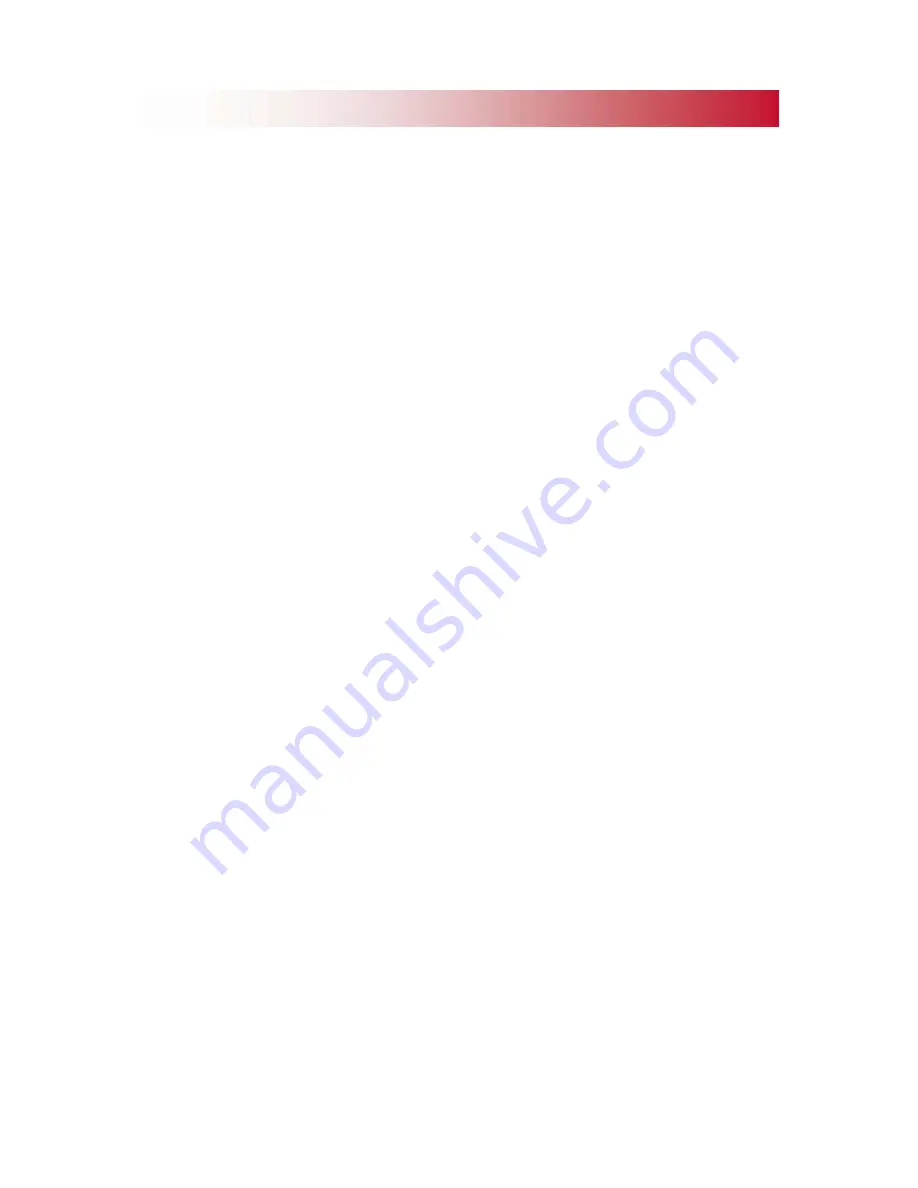
14
4. DX Coil Information
DX COILS
General description
DX coils comprise a matrix of copper tubes
supported in tube end plates and associated
casing work. The tube matrix carries thin
continuous fins, regularly spaced, at right
angles to the tube matrix.
The tubes are fed via headers which
distribute the fluid between a number of
parallel circuits to give the optimum tube
velocity. The flow from the parallel circuits
rejoins in the return header. The flow to DX
evaporator coils is via distributor and
capillary tubes to ensure even distribution.
The fin array is designed to provide an
enlarged air side surface and to optimise
heat transfer for the design air conditions,
whilst minimising the resultant air side
pressure drop.
All coil blocks are tested to 22-bar air under
water, dried, vacuum tested and charged
with dry nitrogen.
F Gas certificate of engineers must only be
used
for
the
installation,
service,
maintenance
or
commissioning
of
refrigeration air conditioning and heat pump
systems containing or designed to contain
HFC refrigerant.
Refrigerant coils
Evaporator coils are supplied with one or
more liquid refrigerant distributors connected
via capillary tubes to the coil circuitry. These
are of equal length for correct refrigerant
distribution. Care should be taken to avoid
kinking the tubes.
Refrigerant coils are generally supplied with
sealed caps, and the coil positively charged
with dry Nitrogen. The connections should be
cut or sweated off when ready for installation.
Capillary or compression fittings should be
fitted
according
to
manufacturer’s
instructions.
Care should be taken to avoid the
introduction of foreign matter or moisture into
the system when piping up, as this may have
an adverse effect on the longevity and
performance of the system.
Maintenance
Preventative maintenance is generally required to
ensure that the coils are maintained in a clean
condition. This has three purposes:
1.
Ensures that there is no marked increase in air
side pressure drop.
2.
Ensures that there is no significant impairment in
air side heat transfer capability.
3.
Ensures that drainage from wet coils is not
impaired over time.
Coils are virtually maintenance free, but in the
event of build up of atmospheric dust or fluff on the
fin surface, can be removed by vacuum or air blast,
taking care that all loosened debris is removed and
not carried into the distribution ductwork. In the
event of fins being pressed in, relieve with a thin
blade. Minor fin-damage has little or no effect on
coil performance.
It is normal when checking for drainage to ensure
that this occurs when the system is running, in
addition to static tests.
Cleaning
Coil drain pans extend beneath the fin block return
bends and manifolds so as to catch all moisture
condensing on the cold surfaces in the cooling
cycle. Drain pans should be inspected and cleaned
on a regular basis so as to prevent the build up of
debris and/or mould. The degree of build up is
specific to each installation and will depend largely
on the ambient contamination and class of air
filtration.
It is recommended that the drain pan be cleaned on
a 3 monthly basis, at least initially, following a
procedure broadly in line with that described below.
The drain trap to the drain pan should be
removed to allow free drainage of cleaning fluid and
a bucket or other receptacle placed below the drain
point protruding through the panel of the AHU.
Access to the coil drain pan can be gained from
either the leaving or entering air face or from the
ends of the coil after removing the necessary AHU
panel. Water or cleaning fluid can then be poured
into the drain pan or alternatively a steam spray
can be used. Take care not to flood the drain pan
during filling. Most proprietary cleaning fluids are
suitable for the galvanized steel drain pan though