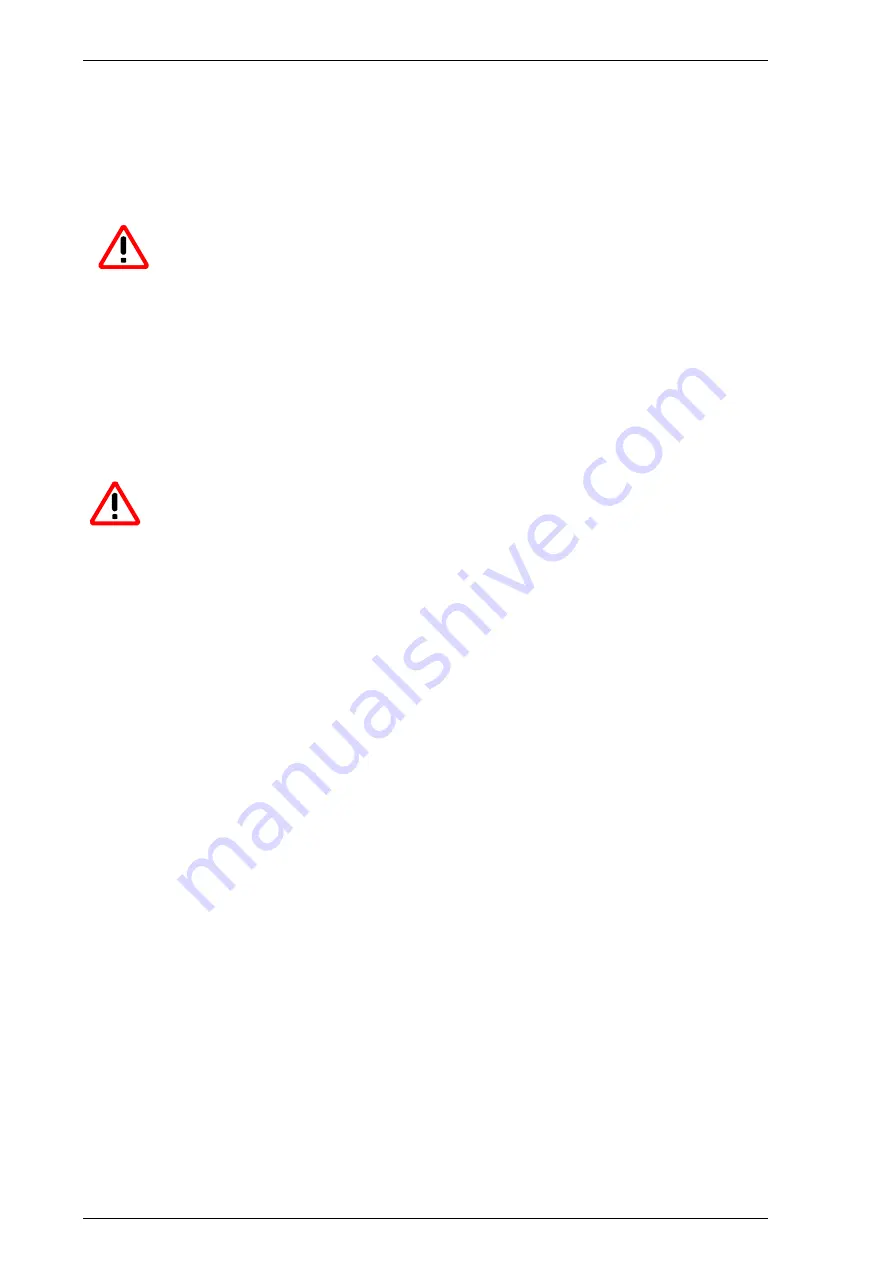
NORDAC SK 1000E Hardware description
20
BU1100 GB
2.9
Basic settings
To start-up, a data record suitable for the motor must be loaded into the corresponding controller using
the supplied NORD SERV software.
Initial test:
Check whether all cables, e.g. limit switches, are correctly connected and whether all
relevant safety precautions have been complied with.
Switch on the line voltage for the servo controller.
Ensure that the motor can start-up without danger. Enable.
Start the motor by increasing the speed, e.g. in the NORD SERV control window,
check that the motor is turning in the required direction.
2.10
Commissioning
When the power supply for the servo controller is switched on, it is operational after a few seconds
(green LED). It can then be set to the application requirements, i.e. parameterised. The motor can only
be started with the enable signal after it has been successfully commissioned initially by qualified
personnel.
The servo controller is not equipped with a line switch and is therefore always live when
connected to the power supply.
When using the incremental encoder and the corresponding hall encoder commutation (rotor position
encoder), only circa 60% of the peak torque is available for the first motor rotation after the power is
switched on.
Check the maximum permissible speed of the encoder used and its limit frequency. The encoder used
in NORD standard motors (2048 inc/rpm) has, up to 85°C, a limit frequency of 200kHz (6000 rpm)
and up to 100°C just 100kHz (3000 rpm).
Long incremental encoder connection cables lead to a not insignificant voltage drop due to the ohmic
resistance of the encoder supply circuits. The encoders used have an operating voltage tolerance of
±
5% (250mV). If this is undershot (< 4.75 V at the encoder), the encoder will operate outside its
specifications and correct function can no longer be guaranteed. The standard encoder cables from
NORD permit a cable length of 20 m. If longer cables are required, the cables must have a larger
cross-section or an external power supply must be used for the encoder. Non-compliance will lead to
pulse losses and therefore to position deviations.
This power supply problem is not critical for resolver cables. However, analog resolver signals will then
be evaluated by the servo controller. Therefore the balance quality will decrease continuously due to
interference injections.
If the data record stored in the unit matches the application and, in particular, the motor, the axis will
be immediately operational after connection. If the settings were not prepared, the axis must be made
operational via the operating interface (see next manual section). The operating interface starts up
with an assistant which can provide comprehensive help. Standard records can be loaded for
synchronous and asynchronous motors from the integrated databases.